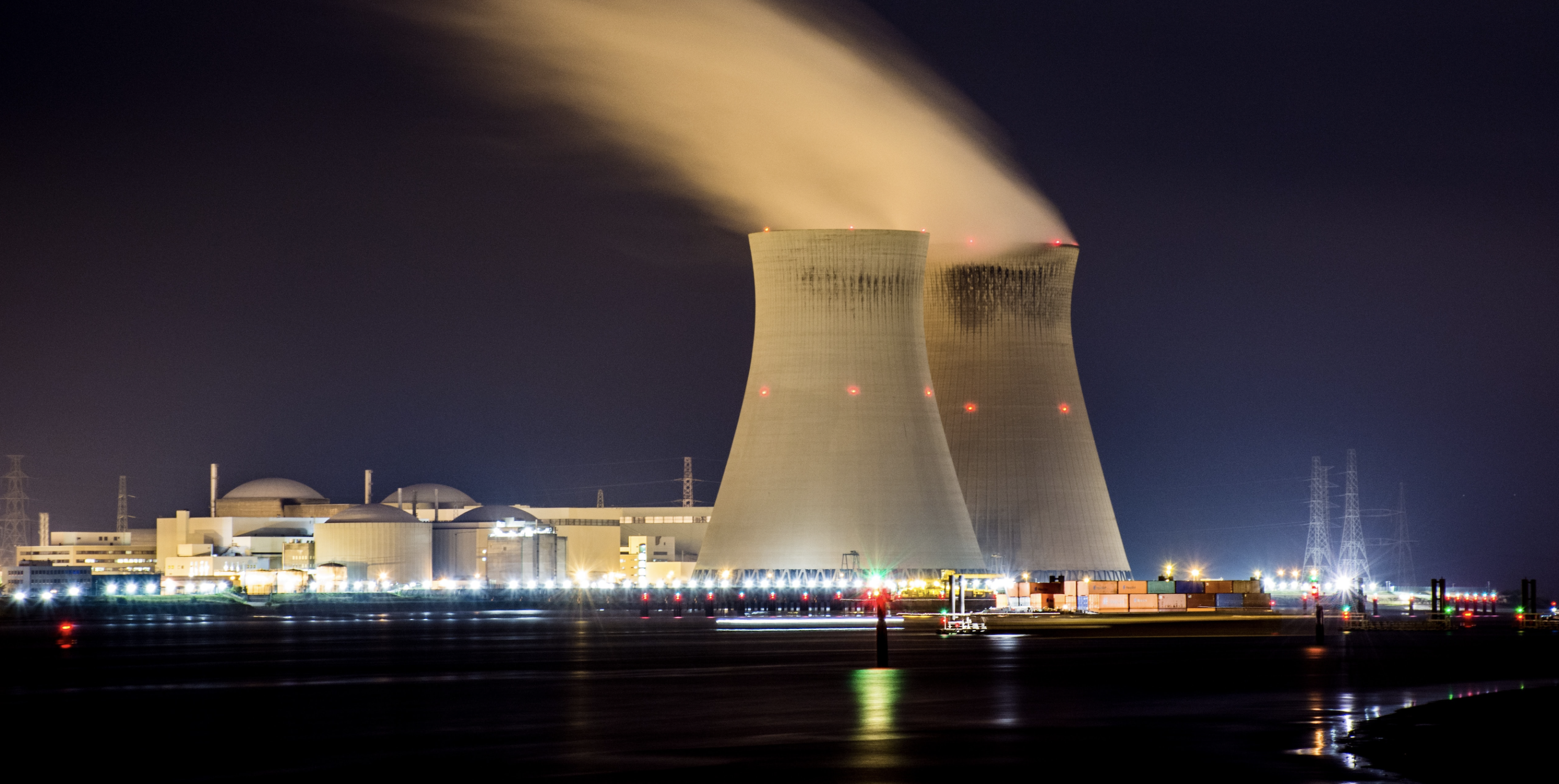
Maintenance Centrée sur la Fiabilité et GMAO
Mercredi 27 avril 2022
Maintenance classique vs Maintenance Centrée sur la Fiabilité
La meilleure façon de résumer la relation entre la Maintenance Centrée sur la Fiabilité (MCF) ou en anglais, Reliability-Centered Maintenance (RCM) et les pratiques traditionnelles de maintenance est la suivante : "les installations et les équipements sont installés et utilisés pour faire ce que les utilisateurs veulent qu'ils fassent. La maintenance est effectuée sous différentes formes, afin de garantir que les installations et les équipements continuent à faire ce que les utilisateurs veulent qu'ils fassent. La maintenance centrée sur la fiabilité détermine très précisément l'entretien à effectuer, les essais à conduire et les contrôles à réaliser pour soutenir cette stratégie de maintenance".
Les résultats d'une analyse MCF entraînent quasi systématiquement des modifications en profondeur de la maintenance préventive pré-existante, l'utilisation de maintenance conditionnelle, des inspections et des essais de fonctionnement, l'ajout ou l'élimination de ces tâches. Elle conduira aussi à la mise en place de la GMAO ou au remplacement de la GMAO pré-existante. A la clé, optimisation des coûts, amélioration de la productivité, de la qualité, augmentation de l’efficacité des services de maintenance,
Lorsqu'elle est utilisée efficacement, elle participe à l'amélioration de la sécurité et de la fiabilité des installations et des équipements et optimise les activités d'exploitation et de maintenance.
Il est à noter toutefois que la MCF n'est pas un processus qui produit des bénéfices à court terme, et ceux qui l'adoptent doivent être préparés à un délai de deux à cinq ans avant d’en tirer pleinement tous les bénéfices.
La MCF pour l'optimisation des activités de maintenance
La MCF est un outil de prise de décision qui entraîne des changements dans les programmes de maintenance et d'exploitation. En voici quelques exemples :
- L'exécution du processus décisionnel de la MCF apporte un avantage en promouvant une meilleure coopération entre tous les acteurs impliqués dans le processus
- Le processus exige que toutes les tâches établies soient remises en question dans le but de justifier la poursuite de leur utilisation ou les supprimer/remplacer par d'autres tâches, ce faisant, il favorise une saine attitude de questionnement.
- Le processus sensibilise aux fonctions des systèmes concernés, aux conséquences d'une défaillance de ces fonctions et aux aspects économiques de leur fonctionnement et de leur maintenance.
Les objectifs de la Maintenance Centrée sur la Fiabilité sont d'améliorer la fiabilité et d'optimiser la rentabilité des activités de maintenance. Lorsqu'elle est exécutée efficacement, elle aboutit à l'élimination des tâches de maintenance inutiles et à l'introduction de mesures visant à remédier aux omissions et aux lacunes des programmes de maintenance.
Les principes de la MCF
Le processus d'analyse de la MCF est centré sur les fonctions des installations et des équipements, les conséquences des défaillances et les mesures visant à prévenir ou à faire face aux défaillances fonctionnelles. Le processus doit établir des réponses aux questions suivantes et une réponse efficace à celles-ci :
- Quelles sont les fonctions de l’installation ?
- Quelles sont les normes de performance de l’installation ?
- De quelle manière ne remplit-elle pas ses fonctions ?
- Quelles sont les causes de chaque défaillance fonctionnelle ?
- Que se passe-t-il lorsque chaque défaillance se produit ?
- En quoi chaque défaillance est-elle importante ?
- Que peut-on faire pour prévoir ou prévenir chaque défaillance ?
Conduire un projet de MCF
Le MCF n'est pas un processus autonome, il doit faire partie intégrante des opérations et programmes de maintenance. L'introduction du processus de MCF implique des changements dans les processus et les wokflows établis. Pour Réussir l’introduction de ces changements, il est indispensable que la direction démontre son engagement envers les changements, éventuellement sous la forme d'une déclaration de politique et d'une implication personnelle, et que des mesures soient prises pour établir l'engagement de ceux qui seront impliqués ou affectés par les changements.
L'implémentation de la méthode MCF est réalisée de façon plus fluide lorsqu'elle est utilisée comme processus ascendant ou bottom-up, impliquant ceux qui travaillent directement dans l'exploitation et la maintenance des installations et des équipements.
Préparation
La phase préparatoire comporte un certain nombre d'étapes qui consistent essentiellement à sélectionner les systèmes à analyser et à recueillir les données nécessaires à l'analyse. En outre, les règles de base ou les critères à utiliser dans le processus de sélection et d'analyse doivent être établis. Par exemple, les hypothèses clés, les critères d'évaluation de criticité, les critères d'évaluation non critiques et l'établissement d'un processus d'examen. L’utilisation d’une GMAO permettant de collecter, modéliser et enregistrer l’ensemble de ces informations va se révéler déterminante à ce stade du projet.
Les étapes peuvent être résumées comme suit :
- Sélection des systèmes
- Sélection des critères de criticité/non criticité
- Acquisition de documentation et de matériel
- Interviews avec le personnel de l'usine
Analyse
Une fois que les systèmes ont été sélectionnés pour l'analyse et que les préparatifs sont terminés, l'analyse peut commencer. L'expérience dans le processus d'analyse est importante pour assurer une prise de décision mature. Cette expérience peut soit se trouver dans le service de maintenance soit être acquise auprès de consultants experts spécialisés dans ce domaine.
Les données contenues dans les systèmes d'information, donc ici la GMAO sont essentielles mais non suffisantes et doivent toujours être complétées par l’expérience acquise par les services techniques sur le terrain. Pour cette raison, il est indispensable que le personnel ayant une expérience locale de l'exploitation et de la maintenance soit impliqué dans le processus d'analyse.
La première étape du processus d'analyse est la constitution de l’équipe projet disposant des compétences, des qualifications et de l’expérience pour mener à bien cette tâche. L'analyse comporte les étapes suivantes :
- Identification des fonctions du système
- Analyse des défaillances fonctionnelles
- Identification des équipements
- Identification des modes de défaillance
- Identification des effets des défaillances
- Détermination de la criticité des composants concernés
Sélection des tâches
Une fois l'analyse terminée, l’étape suivante du processus consiste à attribuer les tâches de maintenance à chaque système et équipement identifié lors du processus d'analyse, en fonction de l'importance qui leur a été attribuée et de leur niveau de criticité. Cette étape consiste à établir les moyens les plus rentables pour atteindre les objectifs de sécurité, de fiabilité, d'environnement et d'économie.
Le processus de sélection des tâches utilise diverses formes de prise de décision logique. Les résultats peuvent comprendre :
- Entretien préventif
- Maintenance conditionnelle
- Inspection et tests fonctionnels
- « Run to failure » stratégie pour les composants les moins critiques
Ces résultats seront alors consignés et enregistrés dans le logiciel de GMAO sous forme de plans de maintenance. La solution logicielle retenue devant être en mesure d’offrir d’une part, une solution mobile facilitant aux techniciens la collecte aisée de données sur le terrain et, d’autre part, une solution d’agrégation et de restitution de cette information sous forme de KPI, Key Performance Indicators, pertinents.
Comparaison avec l’état actuel de la maintenance
Une fois la sélection des tâches terminée et examinée, les recommandations découlant du processus de sélection seront comparées aux pratiques actuelles de maintenance. Cette comparaison a pour but d'identifier les changements nécessaires au programme de maintenance et l'impact sur les ressources tant humaines que matérielles engagées.
Les résultats de l'analyse entraîneront une modification du programme de maintenance. Il est important que ces changements soient compatibles avec la philosophie de maintenance de l’entreprise et avec des obligations réglementaires et sociales. Pour cette raison, il est important que le processus et les résultats soient soumis à un examen final.
Traçabilité et amélioration continue
La MCF doit faire partie d'un programme en perpétuelle adaptation et amélioration. Les résultats du processus d'analyse et de la mise en œuvre des recommandations aura un impact à long terme sur l'efficacité des programmes d'exploitation et de maintenance. Il est donc essentiel que toutes les décisions, les principes qui y ont conduits et les acteurs ayant participé à leur élaboration soient effectivement enregistrés, de sorte que ces informations soient disponibles pour ceux qui auront à procéder à des examens ultérieurs et seront en charge d’adapter, dans le futur, la stratégie de maintenance initialement élaborée.
Conclusion
Un équipement fiable doit rester durablement en parfait état et ne pas tomber en panne. L'apparition inattendue de pannes constitue en effet une cause majeure de la baisse de performance d’une entreprise, particulièrement dans le domaine de l’industrie pour lequel la disponibilité permanente de des outils de production représente un enjeu majeur. Ces pannes dues à des raisons diverses, telles que mauvaises utilisations, maintenance et actions opérationnelles inefficaces, environnements de travail difficiles peuvent en grande partie être anticipées et évitées à l’aide d’un programme de MCF adapté. L’analyse fine des défaillances possibles d'un système, de leur criticité, de leur condition de survenue va permettre d'identifier les principaux facteurs d'influence sur le fonctionnement et les performances de l'équipement. Cette analyse associée à une estimation coûts / bénéfices va assurer l’optimisation des plans de maintenance préventive, conditionnelle, voire même, curative. Un logiciel de gestion de maintenance ou GMAO disposant des fonctionnalités en mesure d’accompagner l’équipe d’expert lors des phases d’analyse et de délivrer ensuite à l’équipe de maintenance technique, les interventions à réaliser, via une planification parfaitement adaptée, est un des facteurs clés de succès d’un tel projet.
Au fait, notre ambition est d’offrir une expérience utilisateur inégalée. Vérifiez-le immédiatement : essayer gratuitement la GMAO. D’ici 2 minutes, le temps de créer votre compte, vous découvrirez ce qui se fait de plus moderne dans cette catégorie de logiciels.
Vous pouvez également bénéficier d’une démonstration animée par l'un de nos consultants : booker une visioconférence
Bonne découverte et à très bientôt sur Yuman.
Retour aux articles