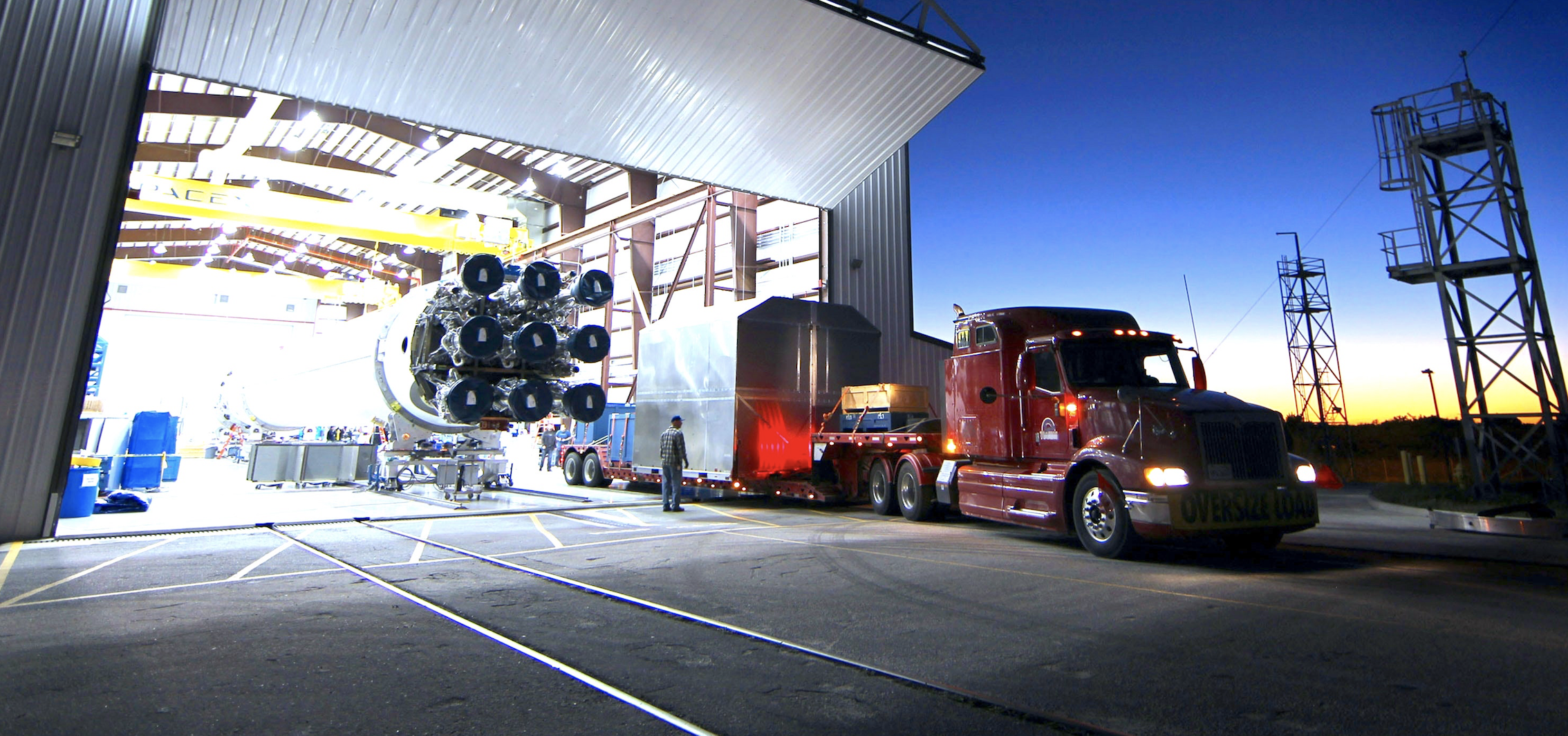
FMECA & GMAO : l'excellence de la maintenance
Mercredi 23 décembre 2020
> Pourquoi une GMAO pour la maintenance industrielle ?
La mise en place d'une stratégie FMECA, en s'appuyant sur la base de connaissances des modes de survenues de défaillance, de leurs effets et de leur criticité, va d’une part, permettre d’améliorer la conception des équipements pour une plus grande fiabilité et une sécurité accrue, et va d’autre part, chercher à en faciliter la maintenance pour un meilleur niveau de service et une réduction des coûts.
Il est également à noter que la conduite d’une stratégie FMECA est fréquemment requise lors d'une démarche de normalisation. Citons par exemple les normes ISO 9001, QS 9000, ISO/TS 16949, les Bonnes Pratiques de Fabrication, les BPF telles qu'exigées par la Food and Drug Administration américaine (FDA).
Nous allons découvrir dans cet article ce que recouvre exactement la FMECA, comment mettre en oeuvre cette stratégie d'excellence de la maintenance et en quoi son intérêt est renforcé lorsqu’elle est associée à un logiciel GMAO.
Qu’est-ce qu'une stratégie FMECA ?
L’acronyme FMECA signifie Failure Modes, Effects and Criticality Analysis, se trouve aussi sous la dénomination AMDEC en français pour Analyse des Modes de Défaillance, de leurs Effets et de leur Criticité.
Le but est d’analyser les types de défaillances, de pannes et d’arrêts des équipements, leurs effets sur la production et la probabilité que de tels évènements se produisent afin de prendre des mesures anticipatives. Ainsi, une action de maintenance telle que le changement d’un composant d’un équipement peut être ajoutée au plan de maintenance préventif, suite aux résultats de l’analyse FMECA.
L’analyse FMECA exige donc l’identification des informations suivantes :
- Quel est l’équipement concerné
- Quelle est sa fonction principale
- La liste des types de panne pouvant survenir, ainsi que leurs causes et leurs effets probables
- La maintenance et les contrôles déjà en place
- Les actions préconisées pour empêcher les arrêts de fonctionnement
Autant d’informations détenues par une GMAO dans laquelle les données techniques ont été correctement collectées et centralisées et qui vont ainsi pouvoir être facilement partagées et exploitées par l’ensemble des acteurs. Nous allons y revenir plus loin : l’association d’une GMAO avec une stratégie de FMECA va permettre de rentrer dans le cercle vertueux de la maintenance.
Quelle est la différence entre FMEA et FMECA ?
Notons avant cela que l’on trouve également parfois l’acronyme FMEA pour Failure Mode and Effects Analysis. Les deux notions sont très proches : on peut considérer la FMEA comme un sous-ensemble nécessaire mais non complètement suffisant de l’analyse. Le “C” de FMECA venant ajouter l’analyse de criticité.
Les étapes pour la mise en place d’une stratégie FMEA sont les suivantes :
- Identifier et recenser tous les modes de défaillance
- Analyser les effets de la panne
- Déterminer les causes de la panne
- Rendre compte des résultats de manière graphique
Pour mettre en place une stratégie complète, il faut ajouter à cette démarche les actions essentielles suivantes :
- Effectuer des calculs de criticité : c’est-à-dire attribuer une note par risque et la pondérer en fonction de sa probabilité
- Déterminer les équipements présentant le risque le plus élevé
- Prendre des mesures d'atténuation du risque et justifier, documenter les risques restants
- Suivre la mise en œuvre et l’efficacité des mesures correctives
Ainsi, le volet criticité de la FMECA consiste à attribuer une note de 1 à 10 aux critères de probabilité de la panne, de ses conséquences et de confiance.
Le critère de confiance est la plausibilité de détecter la défaillance à temps, c’est-à-dire avant qu’elle n’atteigne l’utilisateur final ou le client : plus elle est difficilement détectable, plus son score sera élevé et inversement plus elle est facilement détectable, à l'œil nu ou à l’aide de capteurs, plus la note attribuée sera faible.
En multipliant ces 3 facteurs, on obtient un score de 1 à 1000, appelé score de priorité du risque ou RPN pour Risk Priority Number. Les équipements ayant reçus la note la plus élevée doivent être traités en premier.
Cette criticité étant essentielle, il est possible d’abandonner le terme FMEA pour ne plus parler que la stratégie complète : la FMECA.
Différentes approches selon les données disponibles
Top-down, bottom-up, analyse de la criticité, plusieurs approches sont possibles lors de la conduite d’une analyse FMECA.
Approche descendante (top - down)
L'approche descendante est utilisée dans une phase amont au cours du design et de la conception de la machine afin d’en augmenter au maximum sa robustesse. L'analyse commence par les principales fonctions de production et les causes probables de pannes. Les défaillances fonctionnelles ayant des effets importants sur la production sont classées en priorité dans les résultats de l’analyse, mais celle-ci devra être complétée à un stade plus avancé de la conception.
L'approche descendante peut également être utilisée sur un système existant pour se concentrer sur les domaines les plus problématiques ou ayant déjà montré des signes de faiblesse.
Approche ascendante (bottom - up)
L'approche ascendante est utilisée lorsque la conception de la machine est terminée. Tous les éléments sont étudiés un à un en commençant par les parties les moins critiques, situées le plus bas sur l’arborescence de la machine. L'analyse s’achève lorsque que tous les éléments ont été pris en compte.
Analyse de la criticité
L'analyse de criticité peut être effectuée en utilisant une approche quantitative ou qualitative. La disponibilité des données relatives à la configuration des pièces et au taux de défaillance déterminera l'approche de l'analyse. La règle générale est de se tourner vers une approche quantitative lorsque des données réelles sur les composants ou les sous-équipements sont disponibles et vers une approche qualitative lorsque l’on ne dispose pas encore de données ou qu’elles sont trop génériques.
Criticité quantitative
Le but est de définir la fiabilité ou la non-fiabilité de chaque composant, à un instant T du fonctionnement et d’identifier si la non-fiabilité peut entraîner une défaillance, et surtout si l’avarie est probable et/ou grave.
La formule de calcul est donc la suivante :
manque de fiabilité de l’article x probabilité de défaillance x probabilité de perte ou d’arrêt de production
Criticité qualitative
La criticité qualitative ne disposant pas de données réelles sur les équipements va s’appuyer sur une matrice de criticité, avec en abscisse la gravité des effets potentiels de la panne et en ordonnée la probabilité d'occurrence de chaque défaillance.
Une GMAO pour conduire une analyse FMECA
D’une part, pour être conduite avec efficacité, l’analyse FMECA requiert une quantité importante d’informations sur les équipements. D’autre part la FMECA va produire de nouvelles données qui devront être enregistrées et analysées périodiquement pour évaluer l’impact positif ou non des actions mises en place. Dans ces 2 parties indissociables de l’analyse FMECA, la GMAO joue un rôle essentiel.
En effet, la GMAO recense les équipements et détient leur fiche de caractéristiques techniques, elle enregistre les pannes, les avaries et les actions de maintenance curative et préventive déjà mises en place.
En extrayant ces données de la GMAO, en format brut Excel mais aussi sous forme de ratios et de graphiques tels que le nombre de défaillances sur une période, le temps passé en intervention, le ratio préventif / curatif, le taux de couverture de l’entretien préventif, etc., l’expert maintenance va obtenir la matière première pour commencer votre analyse.
Une fois l’analyse FMECA terminée et les équipements à traiter en priorité déterminés, l’expert sera en mesure de concevoir la mise à jour de la liste des actions de maintenance à mettre en place pour réduire le niveau de risque porté par vos machines.
Ces actions sont à leur tour automatiquement enregistrées dans la GMAO au fur et à mesure de leur exécution, qu’il s’agisse d’une maintenance curative ponctuelle ou d’un ajout au plan de maintenance préventif. La restitution de rapports d’interventions, de photos, du temps passé et des pièces utilisées permettent d’analyser de manière opérationnelle et financière les nouvelles procédures.
Enfin, un nouvel export réalisé dans les 6 mois suivant l'exécution de la FMECA permettra de continuer de mettre à jour la liste des équipements à risque et de tirer les apprentissages de la première mise en place.
Conclusion
L’analyse FMECA est “l’arme absolue” dont doivent disposer les responsables de maintenance qui cherchent tout à la fois à renforcer leur efficacité et leur qualité de service, tout en réduisant leur coût de fonctionnement. Grande consommatrice de données statistiques sur les équipements et les événements survenus, la FMECA doit toujours s’accompagner de l’utilisation de la GMAO, du début de l’analyse des données jusqu’à l’étude des changements conduits. Il est donc essentiel de disposer d’une GMAO claire, moderne, disposant d’un module intégré de FMECA, en mesure d’exploiter en permanence le feedback des événements observés pour tenir à jour les gammes de services et les plans de maintenance. A l’heure actuelle, très peu de GMAO disposent d’un tel module. A bon entendeur...
Au fait, notre ambition est d’offrir une expérience utilisateur inégalée. Vérifiez-le immédiatement : essayer gratuitement la GMAO. D’ici 2 minutes, le temps de créer votre compte, vous découvrirez ce qui se fait de plus moderne dans cette catégorie de logiciels.
Vous pouvez également bénéficier d’une démonstration animée par l'un de nos consultants : booker une visioconférence
Bonne découverte et à très bientôt sur Yuman.
📰 Vous serez également intéressé par la lecture de :
- Gérer ses pièces détachées avec la GMAO
- L'IIoT : l'avenir radieux de la maintenance
- En panne ! Faut-il réparer ou remplacer ?
- Comment la GMAO aide l’Industrie cosmétique ?
- La GMAO pour l’industrie agroalimentaire
- La GMAO pour répondre aux enjeux de l'industrie pharmaceutique
- La GMAO dans le secteur médical
- Total Productive Maintenance & GMAO
- Maintenance autonome & GMAO
- Pourquoi la maintenance préventive est une priorité ?
Retour aux articles