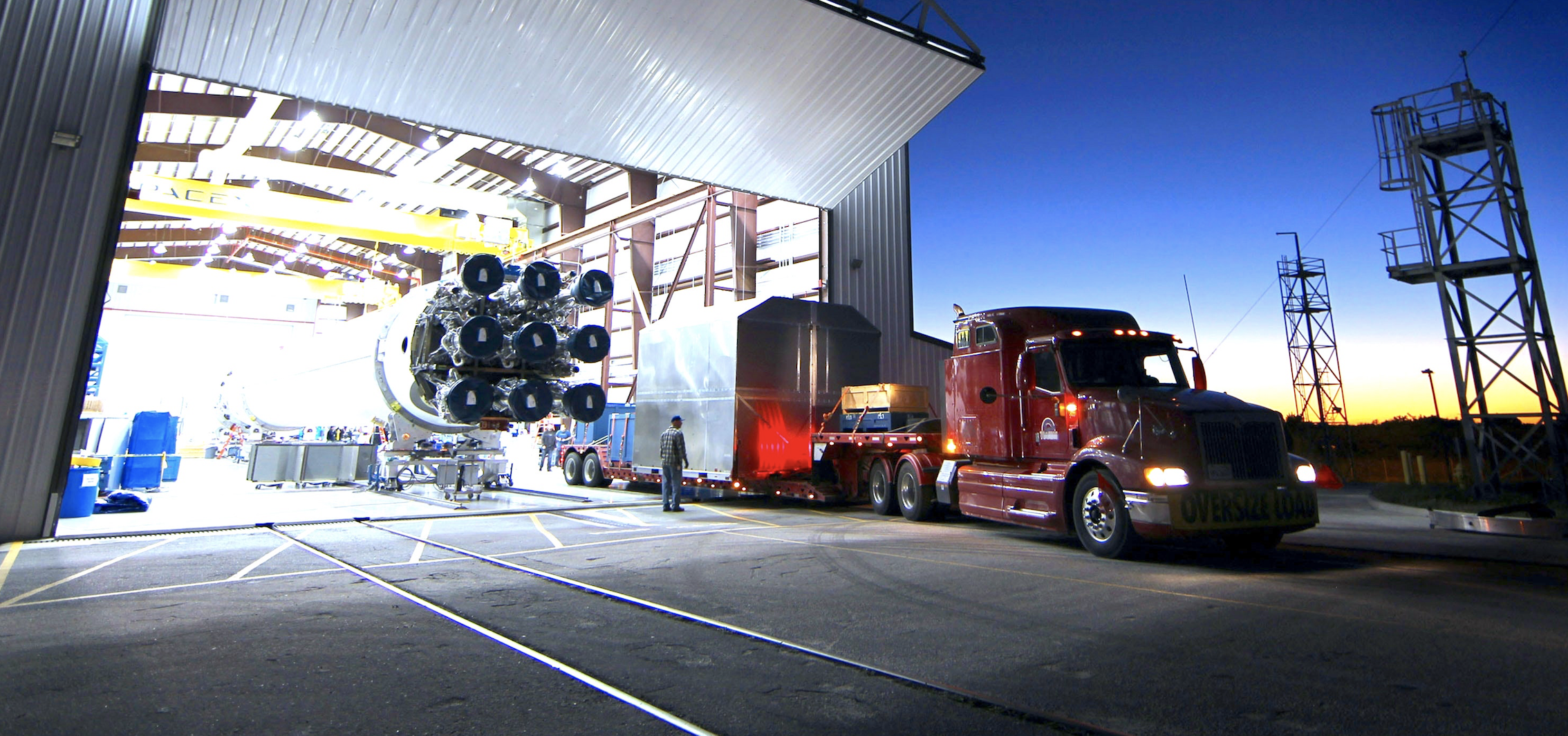
FMECA e CMMS: eccellenza nella manutenzione
Mercoledì 23 dicembre 2020
> Perché un CMMS per la manutenzione industriale?
L'implementazione di una strategia CMMS, basata sulla conoscenza delle modalità di guasto, dei loro effetti e della loro criticità, consentirà da un lato di migliorare la progettazione delle apparecchiature per una maggiore affidabilità;L'obiettivo è quello di migliorare la progettazione delle apparecchiature per una maggiore affidabilità e sicurezza, e di facilitare la manutenzione per un migliore livello di servizio e una riduzione dei costi.
Vale la pena notare che la realizzazione di una strategia FMECA è spesso richiesta durante un processo di standardizzazione. Esempi sono ISO 9001, QS 9000, ISO/TS 16949, Good Manufacturing Practices, GMP come richiesto dalla US Food and Drug Administration (FDA).
Discuteremo gli aspetti coinvolti in una strategia FMECA.
In questo articolo tratteremo cosa copre esattamente la FMECA, come implementare questa strategia di eccellenza manutentiva e come il suo valore viene potenziato se combinato con CMMS software.
Che cos'è una strategia CMMS?
L'acronimo FMECA è l'acronimo di Failure Modes, Effects and Criticality Analysis, che in francese si trova anche sotto il nome di AMDEC, ovvero Analyse des Modes de Défaute; de leurs Effets et de leur Criticité.
L'obiettivo è quello di analizzare i tipi di guasti, guasti e arresti delle apparecchiature, i loro effetti sulla produzione e la probabilità che tali eventi si verifichino, al fine di adottare misure preventive. Così, un'azione di manutenzione come la sostituzione di un componente di un'apparecchiatura può essere aggiunta al piano di manutenzione preventiva, seguendo i risultati dell'analisi FMECA.
L'analisi FMECA richiede pertanto l'identificazione delle seguenti informazioni:
- Quali sono le attrezzature coinvolte?
Qual è la sua funzione principale? - L'elenco dei tipi di guasto che possono verificarsi, insieme alle loro probabili cause ed effetti
- La manutenzione e i controlli in atto
- Le azioni previste per prevenire i tempi di inattività
Tante informazioni sono contenute in un CMMS in cui i dati tecnici sono stati raccolti e centralizzati correttamente e che quindi saranno facilmente condivisi e sfruttati da tutti gli attori. Torneremo su questo punto più avanti: l'associazione di un CMMS con una strategia FMECA permetterà di entrare nel circolo virtuoso della manutenzione
Qual è la differenza tra FMEA e FMECA?
Prima di tutto, notiamo che l'acronimo FMEA è talvolta usato anche per Failure Mode and Effects Analysis. Le due nozioni sono molto vicine: la FMEA può essere considerata un sottoinsieme necessario ma non completamente sufficiente dell'analisi. L'FMEA è un sottoinsieme necessario ma non sufficiente dell'analisi, mentre l'FMEA aggiunge l'analisi delle criticità.
Le fasi di attuazione di una strategia FMEA sono le seguenti:
- Identificare ed elencare tutte le modalità di guasto
- Analizzare gli effetti del guasto
- Determinare le cause del guasto
- Riportare i risultati in forma grafica
Per implementare una strategia completa, a questo processo vanno aggiunte le seguenti azioni essenziali:
È importante notare che le seguenti azioni dovrebbero essere intraprese
- Eseguire i calcoli di criticità: cioè assegnare un punteggio per ogni rischio e ponderarlo in base alla sua probabilità:
- Eseguire i calcoli di criticità: cioè assegnare un punteggio per ogni rischio e ponderarlo in base alla sua probabilità:
- Determinare le strutture con il rischio più elevato
- Adottare misure di riduzione del rischio e giustificare, documentare i rischi rimanenti
- Monitorare l'attuazione e l'efficacia delle azioni correttive
Quindi, la componente di criticità della FMECA consiste nell'assegnare un punteggio da 1 a 10 ai criteri di probabilità di guasto, conseguenze del guasto e fiducia.
Il criterio di criticità è lo stesso utilizzato nella FMECA.
Moltiplicando questi 3 fattori si ottiene un punteggio di 1.000, noto come punteggio di priorità del rischio o RPN. Le apparecchiature con il punteggio più alto devono essere trattate per prime.
Il punteggio di priorità del rischio è il numero di volte in cui il rischio è più alto.
Siccome questa criticità è così essenziale, è possibile abbandonare il termine FMEA e parlare solo della strategia completa: la FMECA.
Approcci diversi a seconda dei dati disponibili
Top-down, bottom-up, analisi delle criticità, sono diversi gli approcci possibili quando si conduce una FMECA.
Approccio dall'alto verso il basso (top - down)
L'approccio top-down viene utilizzato in una fase a monte, durante la progettazione e l'ideazione della macchina, al fine di massimizzarne la robustezza. L'analisi inizia con le principali funzioni di produzione e le probabili cause di fallimento. I guasti funzionali con effetti significativi sulla produzione sono prioritari nei risultati dell'analisi, ma l'analisi dovrà essere completata in una fase più avanzata della progettazione.
L'approccio top-down si basa su una combinazione di approccio top-down e bottom-up.
L'approccio top-down può essere utilizzato anche su un sistema esistente, per concentrarsi sulle aree più problematiche o su quelle che hanno già mostrato segni di debolezza.
Approccio dal basso verso l'alto
L'approccio bottom-up viene utilizzato quando la progettazione della macchina è completa. Tutti i componenti vengono studiati uno per uno, a partire dalle parti meno critiche, situate più in basso nell'albero della macchina. L'analisi è completata quando tutti gli elementi sono stati considerati.
L'analisi è completata quando tutti gli elementi sono stati considerati.
Analisi delle criticità
L'analisi della criticità può essere eseguita con un approccio quantitativo o qualitativo. La disponibilità di dati relativi alla configurazione dei pezzi e al tasso di guasti determinerà l'approccio all'analisi. La regola generale è quella di optare per un approccio quantitativo quando sono disponibili dati reali sui componenti o sulle sotto-attrezzature e per un approccio qualitativo quando i dati non sono ancora disponibili o sono troppo generici.
Criticità
Critica quantitativa
Lo scopo è quello di determinare l'affidabilità o l'inaffidabilità di ciascun componente in un determinato momento durante il funzionamento e di identificare se l'inaffidabilità potrebbe portare a un guasto, e soprattutto se il guasto è probabile e/o grave.
La formula di calcolo è quindi la seguente:
Affidabilità dell'articolo x probabilità di guasto x probabilità di perdita o interruzione della produzione
Criticità qualitativa
La criticità quantitativa, non disponendo di dati reali sull'apparecchiatura, si baserà su una matrice di criticità, con la gravità degli effetti potenziali del guasto sull'asse delle ascisse e la probabilità di accadimento di ciascun guasto sull'asse delle ordinate.
Un CMMS per condurre un'analisi FMECA
Da un lato, per essere condotta in modo efficiente, l'analisi FMECA richiede una quantità significativa di informazioni sulle apparecchiature. D'altra parte, la FMECA produrrà nuovi dati che dovranno essere registrati e analizzati periodicamente per valutare l'impatto positivo o negativo delle azioni implementate. In queste due parti inseparabili dell'analisi FMECA, il CMMS svolge un ruolo essenziale.
Il CMMS è un elemento chiave dell'analisi.
Infatti, il CMMS elenca le apparecchiature e ne conserva la scheda tecnica, registra i guasti, i danni e le azioni di manutenzione correttiva e preventiva già attuate.Estraendo questi dati dal CMMS, in formato Excel grezzo ma anche sotto forma di rapporti e grafici, come il numero di guasti in un periodo, il tempo impiegato per gli interventi, il rapporto preventivo/curativo, il tasso di copertura della manutenzione preventiva, ecc, L'esperto di manutenzione otterrà la materia prima per iniziare l'analisi.
Una volta completata l'analisi FMECA e determinata l'attrezzatura prioritaria da trattare, l'esperto sarà in grado di progettare l'elenco aggiornato delle azioni di manutenzione da implementare per ridurre il livello di rischio delle vostre macchine.
Infine, una nuova esportazione condotta entro 6 mesi dall'esecuzione della FMECA consentirà di continuare ad aggiornare l'elenco delle apparecchiature a rischio e di imparare dalla prima implementazione.
Conclusione
L'analisi FMECA è l'arma vincente per i responsabili della manutenzione che vogliono aumentare l'efficienza e la qualità del servizio, riducendo al contempo i costi operativi. Essendo un importante consumatore di dati statistici sulle apparecchiature e sugli eventi, la FMECA deve sempre essere accompagnata dall'uso del CMMS, dall'inizio dell'analisi dei dati allo studio delle modifiche apportate. È quindi essenziale disporre di un CMMS chiaro e moderno, con un modulo FMECA integrato, in grado di sfruttare continuamente il feedback degli eventi osservati per mantenere aggiornati i piani di assistenza e i programmi di manutenzione. Attualmente sono pochi i CMMS che dispongono di un modulo di questo tipo. Quindi sentiamo...
A proposito, la nostra ambizione è quella di offrire un'esperienza utente senza pari. Scopritelo subito: prova CMMS gratis. In soli 2 minuti, il tempo necessario per creare il vostro account, sarete in possesso delle ultime novità di questa categoria di software.
E' inoltre possibile usufruire di una dimostrazione da parte di uno dei nostri consulenti:prenota una videoconferenza
Buona fortuna e a presto su Yuman.
📰 Vi interesserà anche leggere:
- Gestione dei ricambi con CMMS
- IIoT: il brillante futuro della manutenzione
- Rottura! Riparare o sostituire?
- CMMS per rispondere alle sfide dell'industria farmaceutica
- CMMS nel settore medico
- Total Productive Maintenance & CMMS
- Manutenzione autonoma e CMMS
- Perché la manutenzione preventiva è una priorità