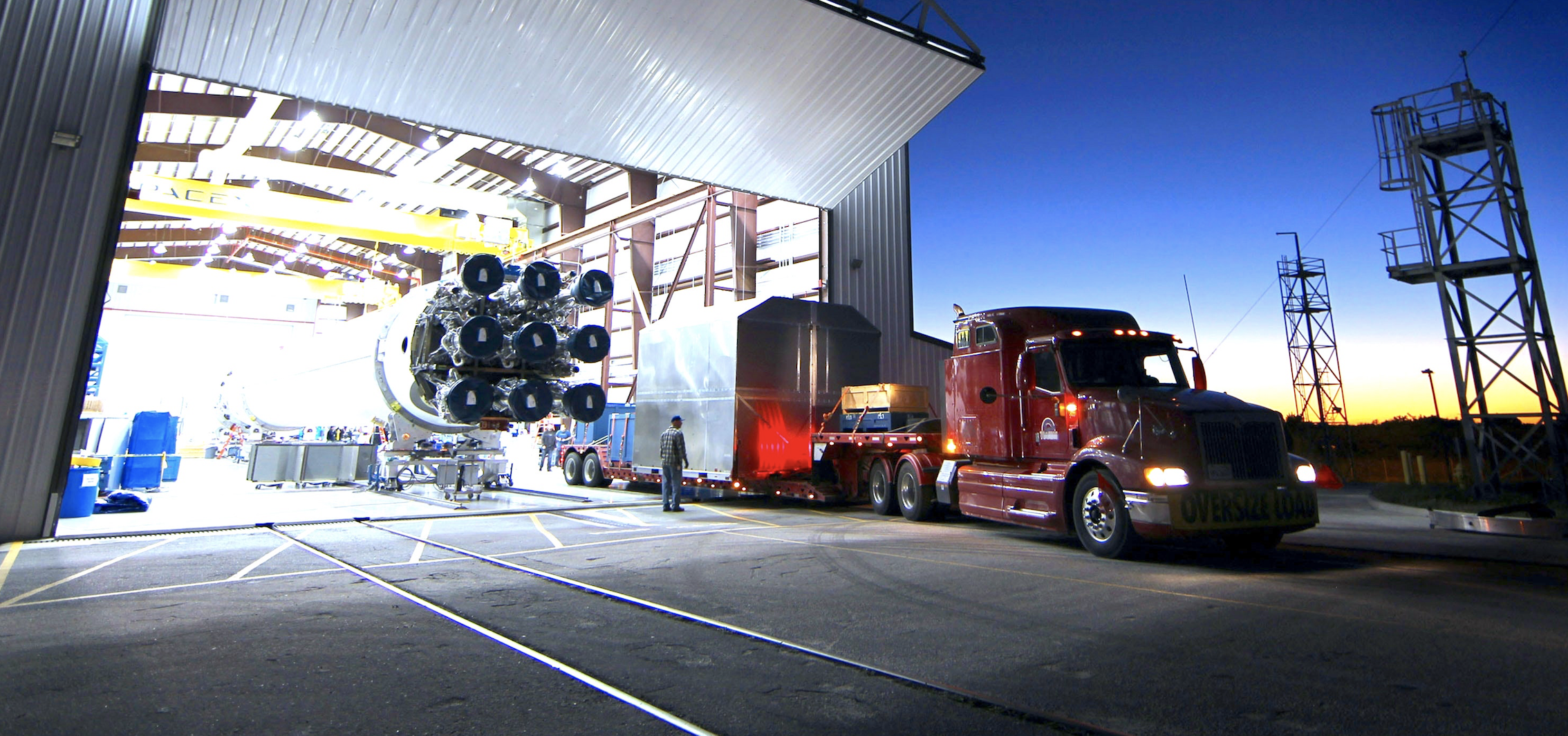
FMECA & CMMS: Exzellenz in der Instandhaltung
Mittwoch 23 dezember 2020
> Warum ein CMMS für die industrielle Instandhaltung?
Die Einführung einer FMECA-Strategie, die sich auf die Wissensbasis der Ausfallarten, ihrer Auswirkungen und ihrer Kritikalität stützt, wird es einerseits ermöglichen, die Konzeption der Anlagen zu verbessern und die Sicherheit der Anlagen zu erhöhen;Der Schwerpunkt liegt dabei auf der Verbesserung der Konstruktion von Anlagen, um deren Zuverlässigkeit und Sicherheit zu erhöhen, sowie auf der Erleichterung der Wartung, um ein höheres Serviceniveau und eine Reduzierung der Kosten zu erreichen.
Es ist auch anzumerken, dass die Führung einer FMECA-Strategie häufig im Rahmen eines Normungsprozesses erforderlich ist. Beispiele hierfür sind die Normen ISO 9001, QS 9000, ISO/TS 16949, die Gute Herstellungspraxis (GMP), wie sie von der amerikanischen Food and Drug Administration (FDA) gefordert wird.
Was genau unter FMECA zu verstehen ist, wie man diese Strategie für exzellente Instandhaltung umsetzt und wie sie in Verbindung mit einer CMMS-Software noch interessanter wird, erfahren Sie in diesem Artikel.
Was ist eine FMECA-Strategie?
Das Akronym FMECA steht für Failure Modes, Effects and Criticality Analysis, findet sich auch unter der Bezeichnung AMDEC im Französischen für Analyse des Modes de Défaillance, de leurs Effets et de leur Criticité.
Das Ziel ist es, die Arten von Fehlern, Pannen und Ausfällen von Anlagen, ihre Auswirkungen auf die Produktion und die Wahrscheinlichkeit, dass solche Ereignisse eintreten, zu analysieren, um vorausschauende Maßnahmen zu ergreifen. So kann eine Wartungsmaßnahme, wie z. B. der Austausch einer Komponente einer Anlage, aufgrund der Ergebnisse der FMECA-Analyse in den vorausschauenden Wartungsplan aufgenommen werden.
Die FMECA-Analyse erfordert daher die Identifizierung der folgenden Informationen:
- Was ist die betroffene Ausrüstung;
- Was ist seine Hauptfunktion
- Die Liste der Arten von Ausfällen, die auftreten können, sowie deren Ursachen und wahrscheinliche Auswirkungen
- Die vorhandenen Wartungs- und Kontrollmaßnahmen
- Vorgesehene Maßnahmen zur Vermeidung von Betriebsunterbrechungen
So viele Informationen werden von einem CMMS bereitgestellt, in dem die technischen Daten korrekt gesammelt und zentralisiert wurden, sodass sie von allen Beteiligten leicht geteilt und genutzt werden können. Wir werden später noch darauf zurückkommen: Die Kombination eines CMMS mit einer FMECA-Strategie wird es ermöglichen, in den positiven Kreislauf der Instandhaltung einzutreten.
Was ist der Unterschied zwischen FMEA und FMECA?
Zunächst sei angemerkt, dass man émanchmal auch das Akronym FMEA für Failure Mode and Effects Analysis findet. Die beiden Begriffe sind sehr ähnlich: FMEA kann als eine notwendige, aber nicht vollständig ausreichende Teilmenge der Analyse betrachtet werden. Das “C” von FMECA fügt die Kritikalitätsanalyse hinzu;;
Die Schritte für die Einführung einer FMEA-Strategie sind wie folgt:
- Identifizieren und erfassen Sie alle Ausfallarten
- Analysieren Sie die Auswirkungen des Ausfalls
- Die Ursachen des Ausfalls ermitteln
- Über die Ergebnisse in grafischer Form berichten
Um eine umfassende Strategie zu entwickeln, muss man à diese Vorgehensweise um die folgenden wesentlichen Maßnahmen erweitern:
- Kritikalitätsberechnungen durchführen: d.h. jedem Risiko eine Bewertung zuweisen und diese nach der Wahrscheinlichkeit gewichten;
- Die Ausrüstungen mit dem höchsten Risiko fertigstellen;
- Maßnahmen zur Risikominderung ergreifen und begründen, dokumentieren Sie die verbleibenden Risiken
- Überwachung der Umsetzung und Wirksamkeit von Korrekturmaßnahmen
So besteht die Kritikalität der FMECA darin, dass die Kriterien Wahrscheinlichkeit des Ausfalls, Folgen des Ausfalls und Vertrauenswürdigkeit mit 1-10 bewertet werden.
Das Vertrauenskriterium ist die Plausibilität, den Fehler rechtzeitig zu erkennen, d.h. bevor er den Endbenutzer oder Kunden erreicht: Je schwieriger sie zu erfassen ist, desto höher ist die Punktzahl; und umgekehrt, je leichter sie zu erfassen ist, sei es durch das bloße Auge oder durch Sensoren, desto niedriger ist die Punktzahl
Die Multiplikation dieser drei Faktoren ergibt eine Punktzahl von 1 à 1000, die als Risikoprioritätspunktzahl oder RPN (Risk Priority Number) bezeichnet wird. Die Geräte mit der höchsten Bewertung sollten zuerst behandelt werden.
Die Geräte mit der höchsten Bewertung sollten zuerst behandelt werden.
Die Geräte mit der niedrigsten Bewertung sollten zuerst behandelt werden.
Da diese Kritik so wesentlich ist, ist es möglich, den Begriff FMEA aufzugeben und nur noch von der kompletten Strategie zu sprechen: FMECA.
Verschiedene Ansätze je nach den verfügbaren Daten
Top-down, Bottom-up, Kritikalitätsanalyse - bei der Durchführung einer FMECA-Analyse sind verschiedene Ansätze möglich.
Top-down-Ansatz
Der Top-Down-Ansatz wird in einer vorgelagerten Phase während des Designs und der Konstruktion der Maschine verwendet, um ihre Robustheit so weit wie möglich zu erhöhen. Die Analyse beginnt mit den wichtigsten Produktionsfunktionen und den wahrscheinlichen Ursachen für Ausfälle. Funktionsausfälle mit erheblichen Auswirkungen auf die Produktion werden in den Ergebnissen der Analyse priorisiert, aber die Analyse muss in einem späteren Stadium des Designs vervollständigt werden.
Der Top-Down-Ansatz kann auch bei einem bestehenden System verwendet werden, um sich auf die Bereiche zu konzentrieren, die am problematischsten sind oder Anzeichen von Schwäche gezeigt haben.
Bottom-up-Ansatz
Der Bottom-up-Ansatz wird verwendet, wenn das Design der Maschine abgeschlossen ist. Alle Elemente werden einzeln untersucht, beginnend mit den am wenigsten kritischen Teilen, die in der Baumstruktur der Maschine am weitesten unten liegen. Die Analyse ist abgeschlossen, wenn alle Elemente berücksichtigt wurden.
Die Analyse ist abgeschlossen, wenn alle Elemente berücksichtigt wurden.
Kritikalitätsanalyse;
Die Kritikalitätsanalyse kann mithilfe eines quantitativen oder qualitativen Ansatzes durchgeführt werden. Die Verfügbarkeit von Daten über die Konfiguration der Bauteile und die Ausfallrate bestimmt den Ansatz der Analyse. Die allgemeine Regel ist, dass man sich für einen quantitativen Ansatz entscheiden sollte, wenn tatsächliche Daten über Bauteile oder Unterbaugruppen verfügbar sind, und für einen qualitativen Ansatz, wenn noch keine Daten verfügbar sind oder diese zu allgemein sind.
Quantitative Kritik
Das Ziel ist es, die Zuverlässigkeit oder Unzuverlässigkeit jeder Komponente zu einem Zeitpunkt T im Betrieb zu bestimmen und zu identifizieren, ob die Unzuverlässigkeit zu einem Ausfall führen kann, und vor allem, ob der Ausfall wahrscheinlich und/oder schwerwiegend ist.
Die Berechnungsformel lautet daher wie folgt:
Zuverlässigkeitslücke des Artikels x Ausfallwahrscheinlichkeit x Wahrscheinlichkeit des Produktionsverlusts oder der Produktionsunterbrechung
Qualitative Kritik
Die qualitative Kritik beruht auf einer Kritikalitätsmatrix, bei der auf der Abszisse die Schwere der potenziellen Auswirkungen des Ausfalls und auf der Ordinate die Wahrscheinlichkeit des Auftretens jedes Ausfalls angegeben ist.
Ein CMMS zur Durchführung einer FMECA-Analyse
Die FMECA-Analyse erfordert eine große Menge an Informationen über die Geräte, damit sie effizient durchgeführt werden kann. Andererseits wird FMECA neue Daten erzeugen, die aufgezeichnet und periodisch analysiert werden müssen, um die positiven oder negativen Auswirkungen der durchgeführten Maßnahmen zu bewerten. In diesen beiden untrennbaren Teilen der FMECA-Analyse spielt das CMMS eine wesentliche Rolle.
Das CMMS erfasst die Ausrüstungen und erstellt ihre technischen Datenblätter, es registriert Störungen, Schäden und die durchgeführten kurativen und präventiven Wartungsmaßnahmen.
Durch die Extraktion dieser Daten aus dem CMMS im Excel-Rohformat, aber auch in Form von Kennzahlen und Diagrammen, wie z. B. die Anzahl der Ausfälle innerhalb eines Zeitraums, die für die Intervention aufgewendete Zeit, das Verhältnis zwischen vorbeugender und kurativer Wartung, der Deckungsgrad der vorbeugenden Wartung usw., werden die Daten in das CMMS eingelesen, Der Wartungsexperte wird das erste Material erhalten, um mit Ihrer Analyse zu beginnen.
Nachdem die FMECA-Analyse abgeschlossen ist und die vorrangig zu behandelnden Geräte bestimmt wurden, kann der Experte eine aktualisierte Liste der Instandhaltungsmaßnahmen erstellen, die zur Verringerung des Risikoniveaus Ihrer Maschinen durchgeführt werden müssen.
Diese Maßnahmen werden automatisch in das CMMS eingetragen, sobald sie ausgeführt werden, unabhängig davon, ob es sich um eine einmalige Wartung oder um eine Ergänzung des Wartungsplans handelt. Die Wiedergabe von Berichten, Fotos, Zeitaufwand und verwendeten Teilen ermöglicht eine effiziente und kosteneffiziente Analyse der neuen Verfahren.
Schließlich wird ein erneuter Export innerhalb von 6 Monaten nach dem Auslaufen der FMECA die Liste der Risikoausrüstungen weiter aktualisieren und die Lehren aus der ersten Einführung ziehen.
Schlussfolgerung
Die FMECA-Analyse ist die absolute Waffe für Instandhaltungsmanager, die ihre Effizienz und Servicequalität steigern und gleichzeitig ihre Betriebskosten senken wollen. Da FMECA einen hohen Bedarf an statistischen Daten über die Anlagen und die eingetretenen Ereignisse hat, muss es immer mit der Verwendung von CMMS einhergehen, vom Zweck der Datenanalyse bis hin zur Untersuchung der durchgeführten Änderungen. Daher ist es wichtig, ein übersichtliches, modernes CMMS mit einem integrierten FMECA-Modul zu haben, das in der Lage ist, ständig Rückmeldungen über beobachtete Ereignisse zu nutzen, um die Servicepläne und Wartungspläne auf dem neuesten Stand zu halten. Derzeit verfügen nur sehr wenige CMMS über ein solches Modul. Lassen Sie sich überraschen...
Unser Anspruch ist es übrigens, eine unvergleichliche Benutzererfahrung zu bieten. Testen Sie es gleich: Kostenlos ausprobieren das CMMS. Innerhalb von 2 Minuten, der Zeit, die Sie brauchen, um Ihr Konto einzurichten, werden Sie das Modernste in dieser Software-Kategorie entdecken.
Sie können auch von einer Vorführung profitieren, die von einem unserer Berater geleitet wird: Videokonferenz buchen
Gute Erholung und à sehr bald auf Yuman.
📰 Sie werden auch interessiert sein an der Lektüre von:
- Verwalten Sie Ihre Ersatzteile mit dem CMMS
- IIoT: Die strahlende Zukunft der Instandhaltung
- Ausfallend! Müssen Sie reparieren oder ersetzen?
- Wie hilft CMMS der Kosmosindustrie?
- CMMS für die Lebensmittelindustrie
- CMMS zur Bewältigung der Herausforderungen in der Pharmaindustrie
- CMMS in der Medizinbranche
- Total Productive Maintenance & CMMS
- Eigenständige Instandhaltung & CMMS
- Warum die vorausschauende Wartung eine Priorität ist;
Zurück zu den Artikeln