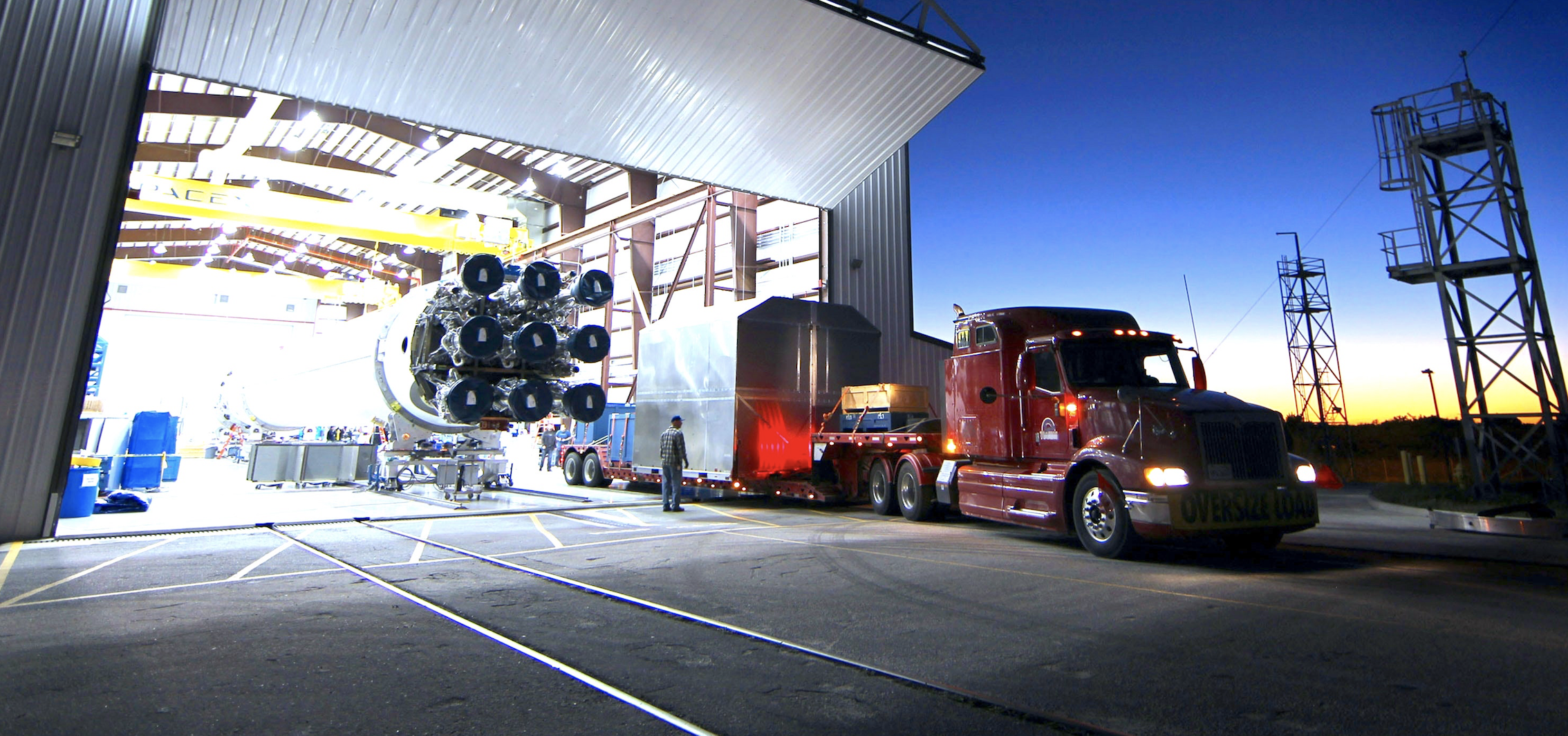
FMECA i CMMS: doskonałość utrzymania ruchu
Środa 23 grudzień 2020
> Dlaczego CMMS dla utrzymania ruchu w przemyśle?
Wdrożenie strategii CMMS, opartej na bazie wiedzy o trybach awarii, ich skutkach i krytyczności, pozwoli z jednej strony na doskonalenie projektowania urządzeń pod kątem większej niezawodności;Celem jest poprawa konstrukcji sprzętu dla większej niezawodności i bezpieczeństwa oraz ułatwienie konserwacji dla lepszego poziomu usług i redukcji kosztów.
Warto również zauważyć, że przeprowadzenie strategii FMECA jest często wymagane podczas procesu normalizacji. Przykłady obejmują ISO 9001, QS 9000, ISO/TS 16949, Good Manufacturing Practices, GMP wymagane przez amerykańską Food and Drug Administration (FDA).
Przedyskutujemy zagadnienia związane ze strategią FMECA.
W tym artykule omówimy, co dokładnie obejmuje FMECA, jak wdrożyć tę strategię doskonałości utrzymania ruchu i jak jej wartość jest zwiększona w połączeniu z oprogramowaniem CMMS.
Czym jest strategia CMMS?
Skrót FMECA oznacza Failure Modes, Effects and Criticality Analysis, występuje również pod nazwą AMDEC w języku francuskim Analyse des Modes de Défaute; de leurs Effets et de leur Criticité.
Celem jest analiza rodzajów awarii, załamań i wyłączeń urządzeń, ich skutków dla produkcji oraz prawdopodobieństwa wystąpienia takich zdarzeń w celu podjęcia działań wyprzedzających. W ten sposób do planu konserwacji zapobiegawczej można dodać działanie konserwacyjne, takie jak wymiana elementu wyposażenia, po uzyskaniu wyników analizy FMECA.
Analiza FMECA wymaga zatem określenia następujących informacji:
- O jaki sprzęt chodzi
- Jaka jest jego główna funkcja
- Lista rodzajów awarii, które mogą wystąpić, wraz z ich prawdopodobnymi przyczynami i skutkami
- Utrzymanie i kontrole już istniejące
- Zalecane działania zapobiegające przestojom
Tak wiele informacji posiada system CMMS, w którym dane techniczne zostały prawidłowo zgromadzone i scentralizowane, dzięki czemu będą mogły być łatwo udostępniane i wykorzystywane przez wszystkich graczy. Wrócimy do tego później: skojarzenie systemu CMMS ze strategią FMECA pozwoli wejść w wirtuozerskie koło utrzymania ruchu.
Jaka jest różnica między FMEA a FMECA?
Po pierwsze, zauważmy, że skrót FMEA jest również czasami spotykany dla Failure Mode and Effects Analysis. Te dwa pojęcia są bardzo bliskie: FMEA można uznać za konieczny, ale nie w pełni wystarczający podzbiór analizy. FMEA jest koniecznym, ale nie wystarczającym podzbiorem analizy, przy czym FMEA dodaje analizę krytyczności.
Kroki wdrażania strategii FMEA są następujące:
- Zidentyfikuj i wymień wszystkie tryby awarii
- Analiza skutków awarii
- Określ przyczyny awarii
- Raportuj wyniki graficznie
W celu wdrożenia kompleksowej strategii, do tego procesu należy dodać następujące istotne działania:
- Przeprowadź obliczenia krytyczności: tj. przypisz wynik do ryzyka i nadaj mu wagę zgodnie z jego prawdopodobieństwem:
- Przeprowadź obliczenia krytyczności: tj. przypisz wynik do ryzyka i nadaj mu wagę zgodnie z jego prawdopodobieństwem:
- Określ obiekty o najwyższym ryzyku
- Podejmowanie działań ograniczających ryzyko i uzasadnianie, dokumentowanie pozostałych ryzyk
- Monitorowanie wdrażania i skuteczności działań korygujących
Tak więc komponent krytyczności w FMECA polega na przypisaniu punktacji od 1 do 10 kryteriom prawdopodobieństwa awarii, konsekwencji awarii i zaufania.
Kryterium krytyczności.
Mnożąc te 3 czynniki otrzymujemy wynik 1000, znany jako risk priority score lub RPN. Sprzęt o najwyższym wyniku powinien być traktowany w pierwszej kolejności.
Punktacja priorytetu ryzyka to liczba przypadków, w których ryzyko jest najwyższe.
Ponieważ ta krytyczność jest tak istotna, można porzucić termin FMEA i mówić tylko o kompletnej strategii: FMECA.
Różne podejścia w zależności od dostępnych danych
Top-down, bottom-up, analiza krytyczności, kilka podejść jest możliwych podczas przeprowadzania FMECA.
Podejście top-down (góra - dół)
Podejście top-down jest stosowane w fazie upstream podczas projektowania i koncepcji maszyny w celu maksymalizacji jej wytrzymałości. Analiza rozpoczyna się od określenia głównych funkcji produkcyjnych i prawdopodobnych przyczyn awarii. Awarie funkcjonalne o znaczącym wpływie na produkcję są traktowane priorytetowo w wynikach analizy, ale analiza będzie musiała być zakończona na bardziej zaawansowanym etapie projektowania.
Podejście odgórne opiera się na kombinacji podejścia top-down i bottom-up.
Podejście odgórne może być również stosowane w istniejącym systemie, aby skupić się na najbardziej problematycznych obszarach lub tych, które już wykazały oznaki słabości.
Podejście oddolne.
Podejście oddolne jest stosowane, gdy projekt maszyny jest kompletny. Wszystkie komponenty są badane po kolei, zaczynając od najmniej krytycznych części, znajdujących się najniżej na drzewie maszyn. Analiza jest zakończona, gdy wszystkie elementy zostały uwzględnione.
Analiza jest zakończona, gdy wszystkie elementy zostały uwzględnione.
Analiza krytyczności
Analiza krytyczności może być przeprowadzona z zastosowaniem podejścia ilościowego lub jakościowego. Dostępność danych dotyczących konfiguracji części i wskaźnika awaryjności określi podejście do analizy. Ogólna zasada mówi o podejściu ilościowym, gdy dostępne są rzeczywiste dane o komponentach lub podzespołach, oraz o podejściu jakościowym, gdy dane nie są jeszcze dostępne lub są zbyt ogólne.
Krytyczne
Krytyka ilościowa
Celem jest określenie niezawodności lub zawodności każdego komponentu w danym momencie podczas eksploatacji oraz określenie, czy zawodność może doprowadzić do awarii, a zwłaszcza czy awaria jest prawdopodobna i/lub poważna.
Wzór obliczeniowy jest zatem następujący:
Reliability of the item x probability of failure x probability of loss or stoppage of production
Krytyczność jakościowa
Krytyczność ilościowa nie mając rzeczywistych danych o sprzęcie będzie opierać się na macierzy krytyczności, gdzie na osi x znajduje się dotkliwość potencjalnych skutków awarii, a na osi y prawdopodobieństwo wystąpienia każdej awarii.
System CMMS do przeprowadzania analizy FMECA
Z jednej strony, aby analiza FMECA była przeprowadzona efektywnie, wymaga znacznej ilości informacji o sprzęcie. Z drugiej strony, w wyniku FMECA powstaną nowe dane, które będą musiały być okresowo rejestrowane i analizowane w celu oceny pozytywnego lub negatywnego wpływu wdrożonych działań. W tych 2 nierozłącznych częściach analizy FMECA istotną rolę odgrywa system CMMS.
System CMMS jest kluczowym elementem analizy.
W rzeczywistości system CMMS wymienia urządzenia i przechowuje ich kartę techniczną, rejestruje awarie, uszkodzenia oraz wdrożone już korekcyjne i prewencyjne działania konserwacyjne.
Po zakończeniu analizy FMECA i określeniu priorytetowego sprzętu, który należy poddać obróbce, ekspert będzie mógł zaprojektować zaktualizowaną listę działań konserwacyjnych, które należy wdrożyć, aby zmniejszyć poziom ryzyka przenoszonego przez Twoje maszyny.
Te działania są z kolei automatycznie rejestrowane w systemie CMMS w miarę ich wykonywania, niezależnie od tego, czy jest to jednorazowa konserwacja korygująca, czy uzupełnienie planu konserwacji zapobiegawczej. Odtworzenie raportów z interwencji, zdjęć, poświęconego czasu i użytych części pozwala na operacyjną i finansową analizę nowych procedur.
Wreszcie, nowy eksport przeprowadzony w ciągu 6 miesięcy od wykonania FMECA pozwoli na ciągłą aktualizację listy urządzeń zagrożonych i wyciągnięcie wniosków z pierwszego wdrożenia.
Wniosek
Analiza FMECA jest absolutną bronią dla menedżerów utrzymania ruchu, którzy szukają zarówno zwiększenia wydajności i jakości usług, przy jednoczesnym obniżeniu kosztów operacyjnych. FMECA, jako główny konsument danych statystycznych dotyczących urządzeń i zdarzeń, musi zawsze towarzyszyć wykorzystaniu systemu CMMS, od początku analizy danych do badania wprowadzonych zmian. Dlatego niezbędne jest posiadanie przejrzystego, nowoczesnego systemu CMMS, ze zintegrowanym modułem FMECA, który jest w stanie w sposób ciągły wykorzystywać informacje zwrotne z obserwowanych zdarzeń do aktualizowania planów serwisowych i harmonogramów konserwacji. Obecnie bardzo niewiele systemów CMMS posiada taki moduł. A więc posłuchajmy...
Przy okazji, naszą ambicją jest zaoferowanie niezrównanego doświadczenia użytkownika. Sprawdź to natychmiast: wypróbuj CMMS za darmo. W ciągu zaledwie 2 minut, czyli czasu potrzebnego na założenie konta, odkryjesz najnowsze w tej kategorii oprogramowanie.
Możesz również skorzystać z demonstracji jednego z naszych konsultantów:zarezerwuj wideokonferencję
Powodzenia i do zobaczenia wkrótce na Yumanie.
📰 Zainteresuje Cię również lektura:
- Zarządzanie częściami zamiennymi za pomocą CMMS
- IIoT: świetlana przyszłość utrzymania ruchu
- Wypadek! Czy należy naprawiać czy wymieniać?
- Dlaczego konserwacja zapobiegawcza jest priorytetem .
.
Powrót do artykułów