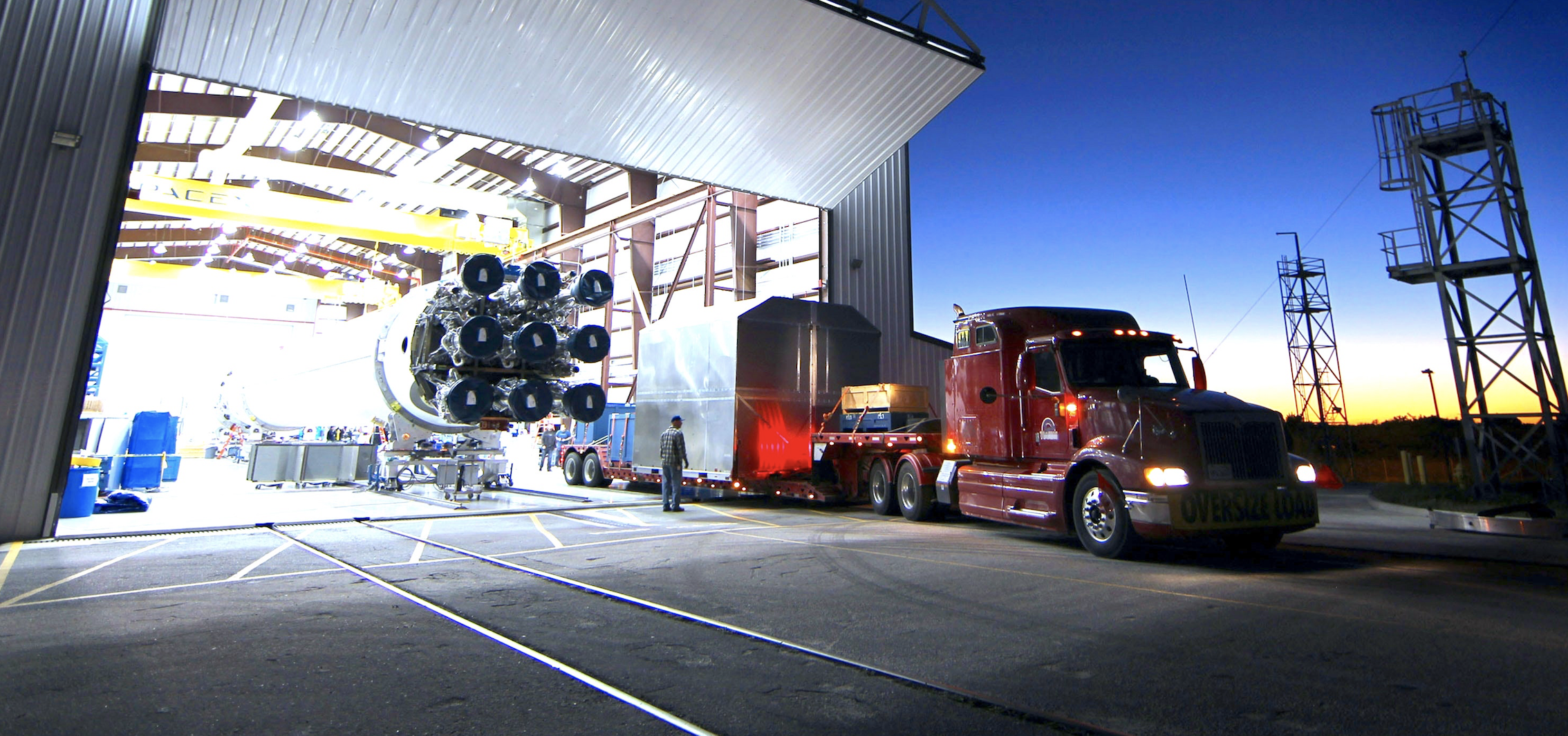
FMECA & CMMS: uitstekend onderhoud
Woensdag 23 december 2020
> Waarom een CMMS voor industrieel onderhoud?
FMECA & CMMS
De FMECA verscheen eind jaren veertig van de vorige eeuw en werd door het Amerikaanse leger gelanceerd toen het besloot zijn aanpak van het onderhoud te wijzigen. Het anticiperen op en voorkomen van storingen in plaats van te wachten tot ze zich voordoen voordat er wordt ingegrepen en gerepareerd, werd het nieuwe leidmotief. Op zijn zachtst gezegd, 80 jaar later, is deze doelstelling vandaag de dag nog steeds relevant in veel onderhoudsafdelingen.
De implementatie van een FMECA-strategie, gebaseerd op de kennisbasis van storingsmodi, hun effecten en kriticiteit, zal enerzijds het ontwerp van de apparatuur verbeteren voor een grotere betrouwbaarheid en veiligheid, en anderzijds het onderhoud vergemakkelijken voor een beter niveau van dienstverlening en kostenreductie.
Ook moet worden opgemerkt dat er tijdens een normalisatieproces vaak een FMECA-strategie nodig is. Voorbeelden hiervan zijn ISO 9001, QS 9000, ISO/TS 16949, Good Manufacturing Practices, GMP zoals vereist door de Amerikaanse Food and Drug Administration (FDA).
In dit artikel ontdekken we wat FMECA precies inhoudt, hoe we deze strategie van uitmuntendheid in onderhoud kunnen implementeren en hoe het belang ervan wordt versterkt wanneer het wordt geassocieerd met CMMS-software.
WAT IS EEN FMECASTRATEGIE?
Het acroniem FMECA staat voor Failure Modes, Effects and Criticality Analysis.
Het doel is het analyseren van de soorten defecten, storingen en stilleggingen van apparatuur, hun effecten op de productie en de waarschijnlijkheid dat dergelijke gebeurtenissen zich voordoen, om zo anticiperende maatregelen te kunnen nemen. Zo kan een onderhoudsactie zoals de wijziging van een onderdeel van een apparaat worden toegevoegd aan het preventieve onderhoudsplan, naar aanleiding van de resultaten van de FMECA-analyse.
De FMECA-analyse vereist dus de identificatie van de volgende informatie:
- Om welke apparatuur het gaat
- Wat is de belangrijkste functie
- Een lijst van de soorten defecten die zich kunnen voordoen, evenals de waarschijnlijke oorzaken en gevolgen ervan
- Onderhoud en controles reeds uitgevoerd
- Aanbevolen acties om stilstand te voorkomen
Al deze informatie wordt bijgehouden door een CMMS waarin de technische gegevens op correcte wijze zijn verzameld en gecentraliseerd en dus gemakkelijk kunnen worden gedeeld en gebruikt door alle spelers. We komen hier later op terug: de associatie van een CMMS met een FMECA-strategie zal ons toelaten om de virtueuze cirkel van het onderhoud te betreden.
WAT IS HET VERSCHIL TUSSEN FMEA EN FMECA?
Allereerst moet worden opgemerkt dat het acroniem FMEA voor Failure Mode and Effects Analysis soms wordt gebruikt. De twee begrippen liggen dicht bij elkaar: FMEA kan worden beschouwd als een noodzakelijke, maar niet geheel toereikende deelverzameling van de analyse. De "C" van FMECA voegt de kritiek-analyse toe.
De stappen voor het opzetten van een FMEA-strategie zijn als volgt:
- Identificeer en maak een lijst van alle storingsmodi
- Analyseer de effecten van het falen
- Bepaal de oorzaken van het falen
- Rapporteer de resultaten grafisch
Om een alomvattende strategie ten uitvoer te leggen, moeten de volgende essentiële acties aan deze aanpak worden toegevoegd:
- Voer de kriticiteitsberekeningen uit: d.w.z. wijs een score toe per risico en weeg deze af op basis van de waarschijnlijkheid ervan.
- Bepaal de apparatuur met het hoogste risico
- Neem risicobeperkende maatregelen en motiveer, documenteer de resterende risico's
- Toezicht houden op de uitvoering en de doeltreffendheid van de corrigerende maatregelen
De criticaliteitscomponent van de FMECA bestaat dus uit het toekennen van een score van 1 tot 10 aan de criteria van faalkans, gevolgen en vertrouwen.
Het betrouwbaarheidscriterium is de aannemelijkheid van het op tijd detecteren van de storing, dus voordat deze de eindgebruiker of klant bereikt: hoe moeilijker het te detecteren is, hoe hoger de score zal zijn, en omgekeerd, hoe gemakkelijker het te detecteren is, hetzij met het blote oog, hetzij met sensoren, hoe lager de score zal zijn.
Het vermenigvuldigen van deze 3 factoren geeft een score van 1 tot 1000, genaamd Risk Priority Score of RPN voor Risk Priority Number. De apparatuur met de hoogste score moet als eerste worden verwerkt.
Aangezien deze kriticiteit essentieel is, is het mogelijk om de term FMEA te laten vallen en alleen te verwijzen naar de volledige strategie: FMECA.
VERSCHILLENDE BENADERINGEN, AFHANKELIJK VAN DE BESCHIKBARE GEGEVENS
Top-down, bottom-up, criticaliteitsanalyse, verschillende benaderingen zijn mogelijk bij het uitvoeren van een FMECA-analyse.
Top-down benadering
De top-down benadering wordt gebruikt in een upstream fase tijdens het ontwerp en de conceptie van de machine om de robuustheid ervan te maximaliseren. De analyse begint met de belangrijkste productiefuncties en de waarschijnlijke oorzaken van storingen. Functionele storingen met significante effecten op de productie krijgen prioriteit in de analyseresultaten, maar de analyse moet in een later stadium van het ontwerp worden afgerond.
De top-down benadering kan ook worden gebruikt op een bestaand systeem om zich te richten op de meest problematische gebieden of gebieden die al tekenen van zwakte hebben vertoond.
Bottom-up benadering
De bottom-up benadering wordt gebruikt wanneer het machineontwerp is voltooid. Alle elementen worden één voor één bestudeerd, te beginnen met de minst kritische onderdelen, die zich het laagst op de machineboom bevinden. De analyse eindigt wanneer alle elementen in aanmerking zijn genomen.
Kritische analyse
De analyse van de kriticiteit kan worden uitgevoerd met behulp van een kwantitatieve of kwalitatieve benadering. De beschikbaarheid van gegevens over onderdeelconfiguratie en storingspercentage is bepalend voor de aanpak van de analyse. De algemene regel is om een kwantitatieve benadering te gebruiken wanneer feitelijke gegevens over componenten of sub-apparatuur beschikbaar zijn en een kwalitatieve benadering wanneer gegevens nog niet beschikbaar zijn of te generiek zijn.
Kwantitatieve Kritiek
Het doel is om de betrouwbaarheid of onbetrouwbaarheid van elk onderdeel te definiëren, op een tijdstip T van werking en om vast te stellen of de onbetrouwbaarheid kan leiden tot een storing, en vooral of de schade waarschijnlijk en/of ernstig is.
De berekeningsformule is daarom als volgt:
item onbetrouwbaarheid x faalkans x kans op verlies of stopzetting van de productie
Kwalitatieve kritiek
Kwalitatieve kriticiteit zonder echte gegevens over de apparatuur zal worden gebaseerd op een kriticiteitsmatrix, waarbij de abscis de ernst van de potentiële effecten van de storing en de ordinaat de waarschijnlijkheid van het optreden van elke storing aangeeft.
A CMMS OM FMECA-ANALYSE UIT TE VOEREN
Enerzijds is voor een efficiënte uitvoering van de FMECA-analyse een aanzienlijke hoeveelheid informatie over de apparatuur nodig. Anderzijds zal de FMECA nieuwe gegevens opleveren die periodiek moeten worden geregistreerd en geanalyseerd om de positieve of negatieve impact van de uitgevoerde acties te evalueren. In deze 2 onlosmakelijk met elkaar verbonden delen van de FMECA-analyse speelt CMMS een essentiële rol.
Het CMMS geeft immers een overzicht van de apparatuur en bevat hun technische karakteristieken, het registreert storingen, beschadigingen en reeds geïmplementeerde curatieve en preventieve onderhoudsacties.
Door deze gegevens uit het CMMS te halen, in ruw Excel-formaat maar ook in de vorm van ratio's en grafieken zoals het aantal storingen over een periode, de interventietijd, de preventieve/curatieve ratio, de dekkingsgraad van het preventief onderhoud, etc., verkrijgt de onderhoudsexpert het ruwe materiaal om met uw analyse te beginnen.
Zodra de FMECA-analyse is afgerond en de te behandelen apparatuur als prioriteit is vastgesteld, kan de expert de lijst met onderhoudsacties die moeten worden uitgevoerd om het risiconiveau van uw machines te verlagen, opstellen.
Deze acties worden op hun beurt automatisch geregistreerd in het CMMS terwijl ze worden uitgevoerd, of het nu gaat om een eenmalig curatief onderhoud of een aanvulling op het preventieve onderhoudsplan. De teruggave van interventierapporten, foto's, bestede tijd en gebruikte onderdelen maken een operationele en financiële analyse van de nieuwe procedures mogelijk.
Ten slotte zal een nieuwe export in de 6 maanden na de uitvoering van de FMECA het mogelijk maken om de lijst van risicoapparatuur te blijven actualiseren en te leren van de eerste implementatie.
CONCLUSIE
De FMECA-analyse is het "absolute wapen" waarover onderhoudsmanagers moeten beschikken als ze hun efficiëntie en kwaliteit van de dienstverlening willen verhogen en tegelijkertijd hun bedrijfskosten willen verlagen. FMECA is een grote afnemer van statistische gegevens over apparatuur en gebeurtenissen die zich hebben voorgedaan, en moet altijd vergezeld gaan van het gebruik van CMMS, vanaf het begin van de gegevensanalyse tot aan de studie van de aangebrachte wijzigingen. Het is daarom essentieel om een duidelijk, modern CMMS te hebben, met een geïntegreerde FMECA-module, die in staat is om de feedback van de waargenomen gebeurtenissen permanent te benutten om de servicebereiken en onderhoudsplannen up-to-date te houden. Op dit moment zijn er maar weinig CMMS'en die een dergelijke module hebben. Een goede luisteraar...
Het is overigens onze ambitie om een ongeëvenaarde gebruikerservaring te bieden. Bekijk het meteen: probeer CMMS gratis uit. Binnen 2 minuten, de tijd die nodig is om je account aan te maken, ontdek je wat het nieuwste is in deze categorie van software.
U kunt ook profiteren van een demonstratie onder leiding van een van onze consultants: boek een videoconferentie
Goede ontdekking en tot ziens!
Terug naar artikelen