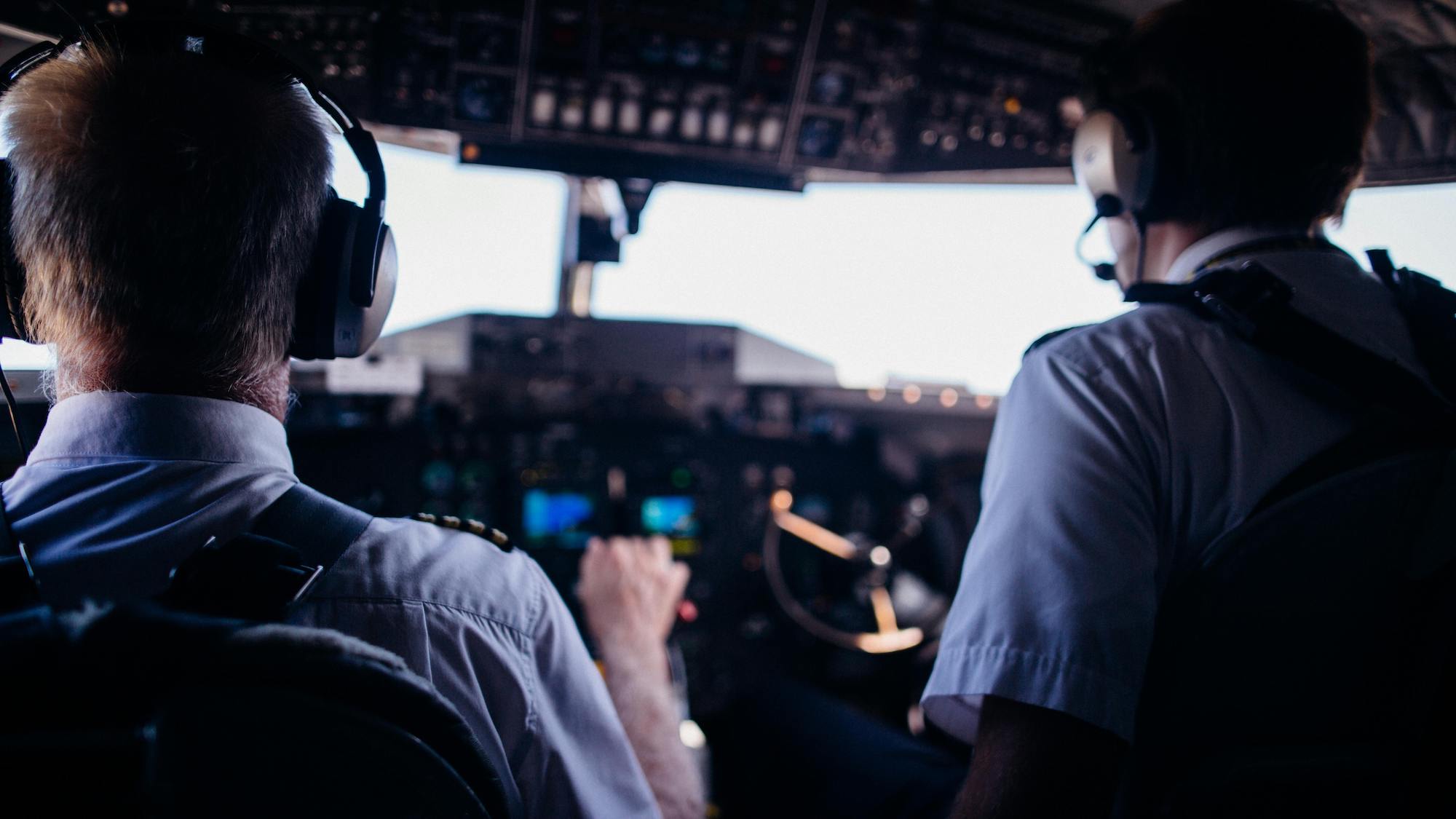
AI at the service of maintenance companies
Friday 17 january 2025
Artificial intelligence (AI) has transformed many sectors, and maintenance is no exception. For maintenance companies, the integration of AI represents a unique opportunity to improve efficiency, service quality and profitability. By combining advanced technologies with well-honed processes, companies can not only anticipate failures, but also optimize resources, reduce costs and deliver a better experience for their customers. Here's a top 10 look at how AI can transform the maintenance industry, and how an advanced CMMS like Yuman can contribute to these uses.
1. Predictive maintenance: anticipating breakdowns before they happen
AI enables real-time analysis of data from IoT sensors placed on equipment. These sensors monitor parameters such as temperature, vibration and energy consumption. By identifying anomalies or early warning signs of a breakdown, companies can intervene before a major failure occurs. AI models, trained on historical data, can accurately predict when a component is likely to fail, enabling better planning and avoiding unplanned downtime that costs the company dearly.
With Yuman: CMMS collects, centralizes and analyzes IoT sensor data, enabling seamless integration between predictive alerts and intervention planning. Sensor data is directly linked to work orders, guaranteeing rapid, targeted intervention.
Benefit: Reduced incidents, lower unplanned downtime costs and increased equipment reliability.
2. Optimizing technician rounds
With sophisticated algorithms, AI can generate the most efficient routes for technicians, taking into account intervention priorities, time constraints and geographical locations. Route management is often a complex task for maintenance companies operating on several remote sites. Poor planning can lead to delays, unnecessary travel and a loss of overall efficiency. AI helps avoid these problems by proposing optimal schedules, adapted to changing needs in real time.
With Yuman:Yuman's native tour optimizer, powered by a powerful algorithm, calculates the best routes in real time, adjusting schedules in the face of unforeseen events such as cancellations or emergencies. This enables technicians to reduce travel times while increasing productivity, resulting in greater customer satisfaction and better management of internal resources.
Benefit:Time savings, fuel savings, and improved productivity.
3. Automatic and assisted diagnostics
AI can analyze databases of breakdown history and symptoms to offer accurate diagnoses. This analysis avoids human error and speeds up problem resolution. For example, if a technician observes a drop in performance on a piece of equipment, AI can provide suggestions based on similar cases, indicating likely causes and corrective steps to follow. This also increases the reliability of interventions, especially in complex cases.
With Yuman: Intervention reports and equipment history integrated into Yuman provide actionable data to feed assisted diagnostics. The platform also enables recommendations to be centralized for fast, efficient decision-making in the field.
Benefit:Reduced repair time and increased intervention accuracy.
4. Automated intervention reports
After each intervention, AI can automate the writing of intervention reports using data collected in the field and incorporating technician feedback. This ensures standardized, accurate reports, essential for equipment monitoring and customer communication. For example, a technician can simply enter a few key words, and the AI completes the rest of the report by generating a detailed description of the actions performed.
With Yuman: CMMS automatically generates complete, clear reports, customizable according to customer needs. These reports can include photos, technical data, and recommendations for future interventions.
Benefit: Fewer administrative tasks, improved customer follow-up and significant time savings.
5. Intelligent preventive maintenance scheduling
AI can evaluate maintenance histories and equipment life cycles to automatically schedule preventive interventions at the right time. This limits wear and tear and preserves assets by avoiding interventions too early or too late. By analyzing data such as frequency of use or operating conditions, AI can accurately determine the ideal times to carry out preventive maintenance.
With Yuman:The preventive maintenance schedules integrated into Yuman are enriched by predictive analytics, guaranteeing optimal anticipation. Managers can clearly visualize deadlines and coordinate teams accordingly.
Benefit: Fewer unexpected breakdowns and improved equipment durability.
6. Improved inventory management
With predictive models, AI can optimize spare parts management by forecasting future needs based on usage and wear data. This avoids stock-outs that could delay interventions. For example, if a certain component is often replaced after a certain number of operating hours, AI can alert to order that part in advance.
With Yuman:Yuman's inventory management module automatically monitors stock levels and sends alerts for replenishment. It also tracks order history to adjust volumes according to trends.
Benefit: Assured availability of critical parts and reduced storage costs.
7. Performance analysis and decision support
AI can provide dashboards and analytical reports to help managers track KPIs (key performance indicators) and identify areas for improvement. By analyzing data in depth, companies can make strategic decisions to allocate resources efficiently and avoid bottlenecks.
With Yuman:Yuman's dynamic, intuitive dashboards highlight team and equipment performance. Managers can easily spot trends, recurring problems and adjust maintenance strategies accordingly.
Benefit:Better strategic decision-making based on reliable data.
8. 24/7 automated customer interaction
AI-powered chatbots can respond to customer queries at any time, handle routine requests and schedule interventions. This automation offloads human teams while maintaining quality customer service, even outside business hours.
With Yuman:The Yuman platform integrates features to automate customer communication, such as appointment confirmations, intervention updates and critical milestone reminders.
Benefit:Improved customer satisfaction and enriched user experience.
9. Technician training via AI tools
AI tools can provide customized tutorials or immersive simulations to train technicians on specific equipment and procedures. This enables rapid upskilling and reduces errors made in the field.
With Yuman:Integrated documentation and interactive guides give technicians quick access to the information they need.
10. Improved traceability and compliance
Traceability is a major issue for maintenance companies, particularly in regulated sectors such as industry, healthcare or renewable energies. AI can automatically record and organize all maintenance activities, guaranteeing clear and accessible documentation. For example, every intervention, from the creation of the work order to its closure, is tracked in real time. This facilitates not only the tracking of operations, but also compliance with current standards and regulations.
AI-based technologies also make it possible to analyze historical data to identify discrepancies or anomalies that could cause problems during audits. Companies can thus demonstrate their seriousness to customers and the authorities, by proving that interventions have been carried out on time and to the required standards.
With Yuman:Yuman's CMMS automates the traceability of every step in the maintenance process. It archives intervention reports, equipment histories, and the critical data required for audits. Thanks to its intuitive interface, managers can generate comprehensive reports to demonstrate regulatory compliance, with just a few clicks.
Furthermore, Yuman offers automatic reminders for periodic inspections and certifications, ensuring that nothing is left to chance. History is organized centrally, preventing information loss and simplifying interactions with auditors.
Benefit:Enhanced traceability, simplified standards compliance and reduced risk of audits or litigation.
Back to the articles