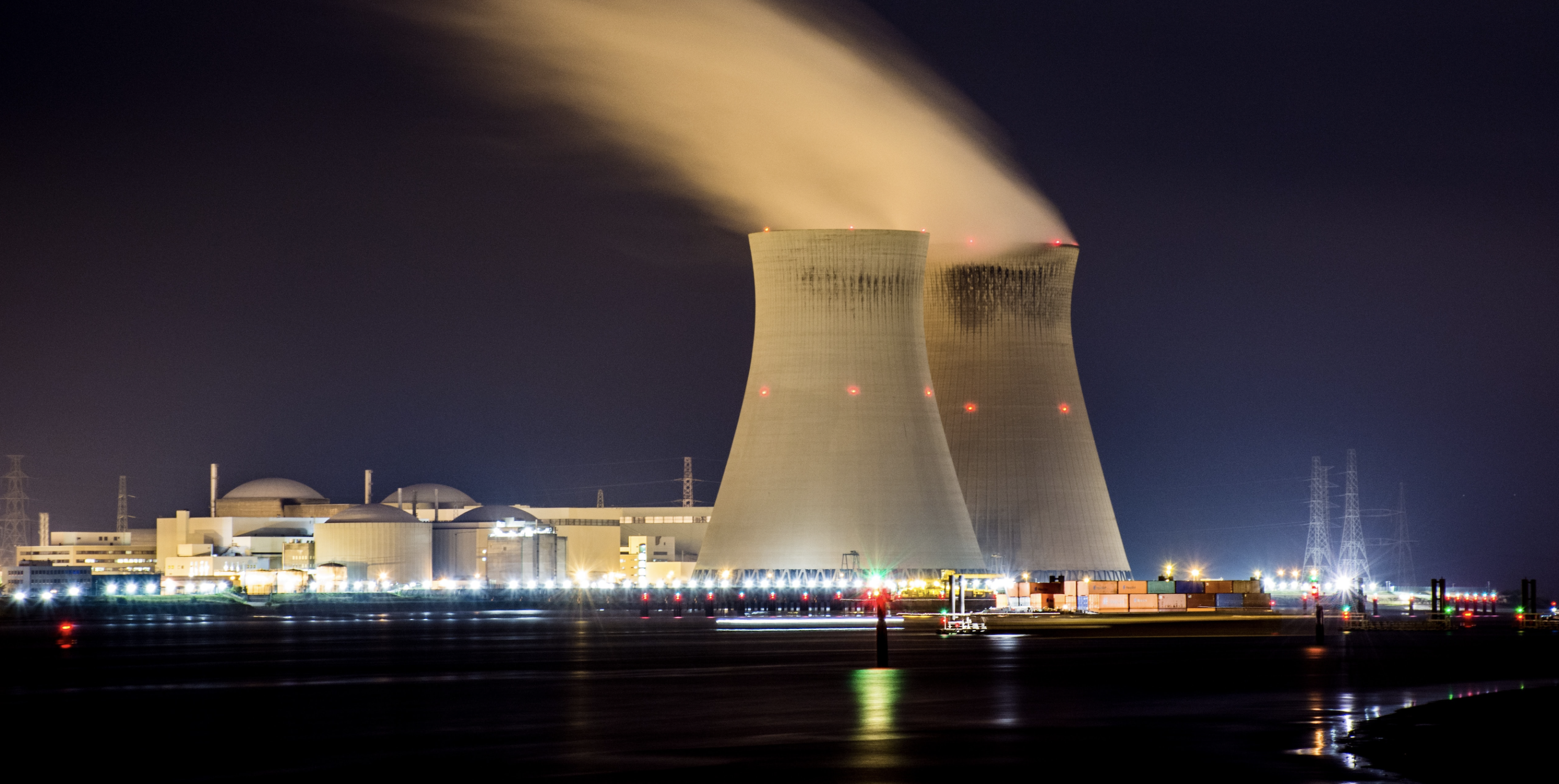
CMMS and Reliability-Centered Maintenance
Wednesday 27 april 2022
TRADITIONAL MAINTENANCE VS. RELIABILITY-CENTERED MAINTENANCE
The best way to summarize the relationship between Reliability-Centered Maintenance (RCM) and traditional maintenance practices is that "facilities and equipment are installed and used to do what users want them to do. Maintenance is performed in a variety of forms to ensure that facilities and equipment continue to do what users want them to do. Reliability Centered Maintenance determines very precisely the maintenance to be performed, the tests to be conducted and the checks to be carried out to support this maintenance strategy".
The results of an RCM analysis almost always lead to in-depth changes to pre-existing preventive maintenance, the use of condition-based maintenance, inspections and functional tests, and the addition or elimination of these tasks. It will also lead to the implementation of the CMMS or the replacement of the pre-existing CMMS. The result is cost optimization, improved productivity, quality, and increased efficiency of maintenance services,
When used effectively, it contributes to improving the safety and reliability of facilities and equipment and optimizes operations and maintenance activities.
It should be noted, however, that RCM is not a process that produces short-term benefits, and those who adopt it must be prepared for a period of two to five years before reaping its full benefits.
THE RCM FOR THE OPTIMIZATION OF MAINTENANCE ACTIVITIES
The RCM is a decision-making tool that leads to changes in maintenance and operating programs. Here are a few examples:
- The execution of the RCM decision-making process brings an advantage by promoting better cooperation between all the actors involved in the process.
- The process requires that all established tasks be questioned in order to justify their continued use or to remove/replace them with other tasks, thereby fostering a healthy questioning attitude.
- The process raises awareness of the functions of the systems involved, the consequences of a failure of these functions, and the economics of their operation and maintenance.
The objectives of Reliability Centered Maintenance are to improve the reliability and optimize the profitability of maintenance activities. When carried out effectively, it results in the elimination of unnecessary maintenance tasks and the introduction of measures to correct omissions and deficiencies in maintenance programs.
THE PRINCIPLES OF THE RCM
The RCM analysis process focuses on the functions of facilities and equipment, the consequences of failures, and measures to prevent or cope with functional failures. The process must establish answers to the following questions and an effective response to them :
- What are the functions of the facility?
- What are the performance standards of the facility?
- How is it failing to perform its functions?
- What are the causes of each functional failure?
- What happens when each failure occurs?
- Why is each failure important?
- What can be done to predict or prevent each failure?
LEAD AN RCM PROJECT
RCM is not a stand-alone process, it must be an integral part of maintenance operations and programs. The introduction of the RCM process involves changes to established processes and wokflows. Successful introduction of these changes requires that management demonstrate its commitment to the changes, possibly in the form of a policy statement and personal involvement, and that steps are taken to establish the commitment of those who will be involved or affected by the changes.
Implementation of the RCM method is most smoothly achieved when it is used as a bottom-up or bottom-up process, involving those who work directly in the operation and maintenance of facilities and equipment.
Preparation
The preparatory phase consists of a number of steps that essentially consist of selecting the systems to be analyzed and collecting the data required for the analysis. In addition, the ground rules or criteria to be used in the selection and analysis process must be established. For example, key assumptions, criticality evaluation criteria, non-critical evaluation criteria, and the establishment of a review process. The use of a CMMS to collect, model and record all of this information will be critical at this stage of the project.
The steps can be summarized as follows:
- Selection of systems
- Selection of criticality/non-criticality criteria
- Acquisition of documentation and equipment
- Interviews with plant personnel
Analysis
Once the systems have been selected for analysis and preparations are complete, the analysis can begin. Experience in the analysis process is important to ensure mature decision making. This experience can either be found in the maintenance department or can be acquired with expert consultants specialized in this field.
The data contained in the information systems, in this case CMMS, are essential but not sufficient and must always be complemented by the experience acquired by the technical services in the field. For this reason, it is essential that staff with local experience in operations and maintenance be involved in the analysis process.
The first step in the analysis process is the establishment of the project team with the skills, qualifications and experience to carry out the task. The analysis consists of the following steps:
- Identification of system functions
- Functional Failure Analysis
- Equipment identification
- Identification of failure modes
- Identification of the effects of failures
- Determination of the criticality of the components concerned
Task Selection
Once the analysis is complete, the next step in the process is to assign maintenance tasks to each system and equipment identified in the analysis process, based on their assigned importance and criticality level. This step consists of establishing the most cost-effective means of achieving safety, reliability, environmental and economic objectives.
The task selection process uses various forms of logical decision making. The results may include :
- Preventive maintenance
- Conditional maintenance
- Inspection and functional tests
- "Run to failure" strategy for less critical components
These results will then be logged and recorded in the CMMS software in the form of maintenance plans. The selected software solution must be able to offer, on the one hand, a mobile solution that facilitates the easy collection of data in the field by technicians and, on the other hand, a solution for aggregating and retrieving this information in the form of relevant KPIs, Key Performance Indicators.
Comparison with current maintenance status
Once the task selection has been completed and reviewed, the recommendations from the selection process will be compared to current maintenance practices. The purpose of this comparison is to identify necessary changes to the maintenance program and the impact on both the human and material resources involved.
The results of the analysis will lead to a modification of the maintenance program. It is important that these changes are compatible with the company's maintenance philosophy and with regulatory and social obligations. For this reason, it is important that both the process and the results are subject to a final review.
TRACEABILITY AND CONTINUOUS IMPROVEMENT
RCM must be part of a program that is constantly adapting and improving. The results of the analysis process and the implementation of the recommendations will have a long-term impact on the effectiveness of operations and maintenance programs. It is therefore essential that all decisions, the principles that led to them, and the actors who participated in their development are effectively recorded, so that this information is available to those who will have to carry out subsequent reviews and will be responsible for adapting the maintenance strategy initially developed in the future.
CONCLUSION
Reliable equipment must remain in perfect condition for a long time and not break down. The unexpected occurrence of breakdowns is indeed a major cause of a company's reduced performance, particularly in the industrial sector where the permanent availability of production tools represents a major challenge. These breakdowns due to various reasons, such as misuse, maintenance and inefficient operational actions, difficult working environments can largely be anticipated and avoided with the help of an adapted RCM program. The detailed analysis of possible system failures, their criticality, their condition of occurrence will allow the identification of the main factors influencing the operation and performance of the equipment. This analysis associated with a cost/benefit estimate will ensure the optimization of preventive, conditional and even curative maintenance plans. A maintenance management software or CMMS with functionalities able to accompany the expert team during the analysis phases and then deliver to the technical maintenance team, the interventions to be carried out, via a perfectly adapted planning, is one of the key factors of success of such a project.
By the way, our ambition is to offer an unparalleled user experience. Check it out right away: try CMMS for free. Within 2 minutes, the time it takes to create your account, you'll discover what's newest in this category of software.
You can also benefit from a demonstration led by one of our consultants: book a videoconference
Good discovery and see you soon!
Back to the articles