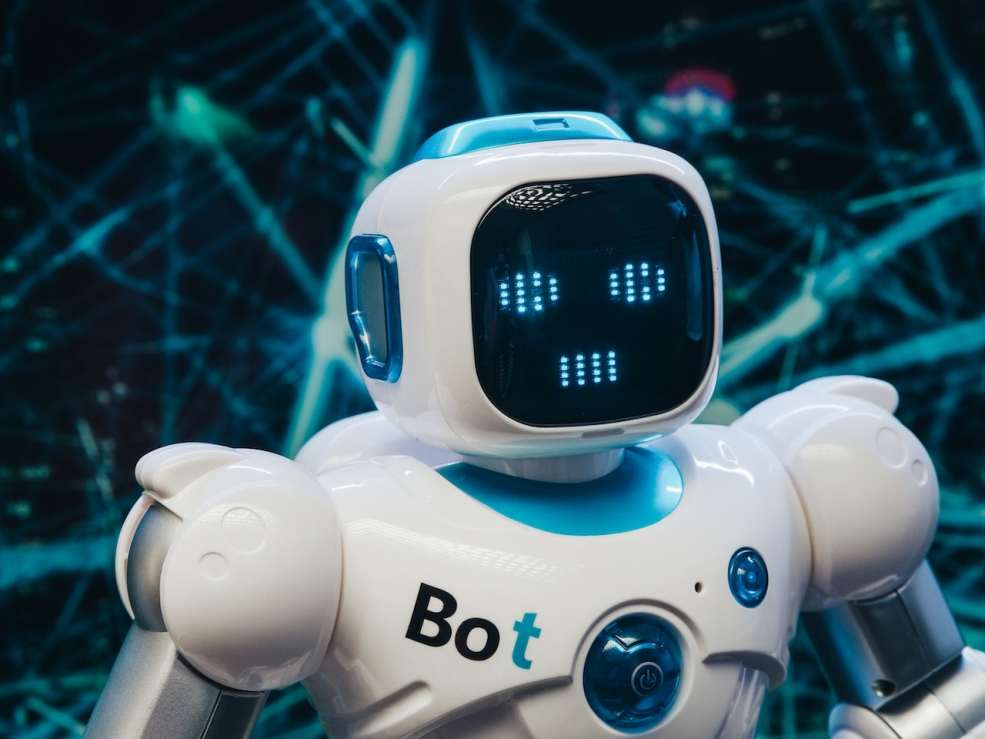
Hello ChatGPT, what do you think about Yuman ?
Thursday 26 january 2023
Hello ChatGPT, what do you think about Yuman?
Yuman is a CMMS, Computer Aided Maintenance Management, software that helps companies optimize their maintenance process. It offers features such as maintenance planning, spare parts inventory management and work order management. The flexibility of its user interface allows users to customize the features to their specific needs. In addition, it is compatible with different operating systems and can be used on mobile devices for efficient maintenance management on the go. All in all, Yuman is an effective software for efficient maintenance management.
Thank you ChatGPT, and à who is Yuman CMMS for?
Yuman is a software for companies and organizations that want to optimize their maintenance management. It is used to plan and track maintenance tasks, manage spare parts inventory and technical data, and improve communication between the various stakeholders in the maintenance process. It can address companies in various sectors such as industry, utilities, transportation services, health services, education services, among others.
What are the benefits of a SaaS CMMS?
Benefits of a SaaS (Software as a Service) CMMS include:
- Accessibility: Users can access the solution from any Internet-connected device, allowing for greater flexibility and mobility.
- Speedy implementation of CMMS
- Fast implementation: There is no need to install software on each computer individually, reducing costs and time to implement the solution.
- Automatic updates: Updates are performed automatically by the SaaS provider, ensuring that the latest version of the software is always used.
- Reduced costs: Acquisition and maintenance costs are generally lower for a SaaS solution compared to a locally installed solution.
- Scalability : It is easy to add or remove users as needed, allowing the solution to adapt to the company's evolution.
- Data accessibility : Data is stored in the cloud, allowing easy and secure access to information from anywhere.
- Data accessibility.
- Security: SaaS providers are often able to guarantee greater data security;They are often able to provide greater data security than a locally installed solution because they have dedicated resources to ensure data security.
How to access the CMMS from your mobile phone
There are several ways to access a CMMS (Computerized Maintenance Management System) from a mobile device, it depends on the solution used. Here are some examples of common methods:
- Dedicated Mobile App: Some CMMSs have a dedicated mobile app, which can be downloaded from an app store (App Store or Google Play). Users can then log in to their account to access all CMMS features.
- Introduction with collaboration tools: some CMMS can be integrated with collaboration tools such as Slack, Microsoft Teams, or even, Microsoft Sharepoint, to allow users to access maintenance information directly from these tools.
It is important to note that to access CMMS from a mobile device, the user must have secure access. It is therefore necessary to check if the access to the solution is secured by a password, a two-factor authentication, or the use of a security certificate.
Is it feasible to use an intervention management software or a CMMS?
It depends on the specific needs of the company. An intervention management software is specifically designed to plan and track maintenance tasks, while a CMMS (Computerized Maintenance Management System) is a more global solution that also covers other aspects such as spare parts inventory management, technical data management, cost management and resource management.
If the company is looking for a software solution, it is important to consider the following
If the company needs a solution that focuses primarily on scheduling and tracking maintenance tasks, job management software may be sufficient. However, if the company needs a more comprehensive solution that also covers other aspects of maintenance, a CMMS may be appropriate.
It's important to have a comprehensive solution that covers all aspects of maintenance.
It is important to note that some CMMSs also include intervention management functionality, so it is possible to find solutions that include both. It is therefore important to carefully evaluate the specific needs of the company before choosing between an intervention management software or a CMMS.
What are the different categories of maintenance interventions?
There are several categories of maintenance interventions, each with different objectives and methods. Common categories include:
Preventive maintenance: this category aims to reduce the risk of equipment failure by performing regular inspections and preventive maintenance. It allows potential problems to be identified and corrected before they cause failures.
Corrective maintenance: the maintenance of a system's performance.
Curative maintenance: this category is designed to repair equipment that has failed. It is often used to repair failed equipment and restore its functionality.
Preventive maintenance
Predictive maintenance: this category aims to use advanced technologies to predict potential problems and plan maintenance interventions accordingly. It extends the life of equipment and reduces maintenance costs.
Conditional maintenance: the most effective way to reduce maintenance costs.
Conditional maintenance: this category aims to use sensors and monitoring technologies to monitor equipment conditions and plan maintenance interventions based on this data.
Adaptive maintenance: this category aims to adapt maintenance interventions according to the actual use of the equipment. It allows to reduce maintenance costs by avoiding unnecessary interventions.
It is important to have a clear understanding of the maintenance process.
It is important to note that each category of maintenance intervention can be combined to maximize benefits and minimize costs. Companies can also choose to prioritize one category of maintenance interventions based on the specific needs of their business.
What is a maintenance range?
A maintenance task list is a set of predefined maintenance tasks that are used to maintain a particular piece of equipment or facility. It is generally based on the technical specifications of the equipment and the manufacturer's recommended maintenance requirements.
A range of maintenance services is available for all equipment.
A maintenance schedule may include various maintenance tasks, such as regular inspections, safety checks, part replacements, adjustments and adjustments, etc. It may also include information on recommended frequencies for each task, as well as required tools and spare parts.
The range is based on the following criteria
Maintenance routings are typically used to plan and organize maintenance tasks, as well as to track the performance of equipment and facilities. They can also be used to identify trends and common problems and to evaluate the effectiveness of maintenance interventions.
It is important to have a clear picture of the current state of the plant.
It is important to note that maintenance ranges can be tailored to meet the specific needs of each company, depending on their business, equipment, facilities and maintenance needs.
What KPIs does Yuman offer?
Yuman CMMS offers several key performance indicators (KPIs) to evaluate maintenance efficiency. These indicators can include:
Availability rate: this indicator measures the proportion of time an asset is available to be used relative to the total time. It provides a measure of the reliability of the equipment and helps to identify common problems.
Performance rate: this indicator measures the proportion of time an equipment is available for use in relation to the total time.
Output rate: this indicator measures the proportion of time an equipment is used to produce finished products relative to the total time. It provides a measure of the efficiency of the equipment and identifies problems that affect production.
The MTB Index: this indicator measures the proportion of time that an equipment is used to produce finished products relative to the total time.
MTBF (Mean Time Between Failure) Index: this indicator measures the average time between two failures of an equipment. It is used to measure the reliability of the equipment and to detect common problems.
MTTR Index
Mean Time To Repair (MTTR) Index: this indicator measures the average time required to repair a failure in a piece of equipment. It allows us to measure the speed of maintenance interventions and to detect problems that affect the availability of the equipment.
Maintenance costs: this indicator measures the costs associated with equipment maintenance, such as spare parts costs, labor costs and intervention costs. It helps measure the effectiveness of maintenance interventions and reduce maintenance costs.
It is important to have a clear understanding of the maintenance process.
It is important to note that these KPIs are examples and CMMS can include other indicators depending on the company's needs.
Is it possible to make estimates with Yuman CMMS?
Yuman CMMS allows you to plan, track and manage maintenance tasks. It also has quote management functionality. However, this depends on the version used. It can include the ability to create quotes for planned or unplanned maintenance interventions, as well as the ability to track accepted quotes and invoices.
The system can also be used to create and track invoices.
Quotes for maintenance interventions can be created using data stored in the CMMS, such as spare parts costs, labor costs and intervention costs. It can also include information on delivery times and warranties. This allows for accurate and detailed quotations to be provided to customers, and facilitates the management of maintenance projects.
Is it possible to invoice with Yuman CMMS?
Yuman CMMS does include billing functionality for maintenance interventions. This depends on the specific features of the version used. The software can include the possibility to generate invoices for planned or unplanned maintenance interventions. It can also include information on accepted quotes, spare parts costs, labor costs and intervention costs. This makes it easier to manage maintenance projects and provide accurate and detailed invoices to customers.
It's important to have a clear picture of the cost of maintenance.
It is important to note that invoicing depends on the specific functionality of the CMMS version used, so it is important to check the functionality of Yuman CMMS before using it to manage invoices for maintenance interventions. It is important to note that the invoicing module complies with the legislation in force in the countries where Yuman is present.
What is Total Productive Maintenance?
The Total Productive Maintenance (TPM) is a maintenance method that aims to improve the availability, quality and productivity of equipment by involving all employees in maintenance activities. This method is based on the idea that all employees, whether they are operators, engineers or technicians, can contribute to improving the performance of equipment by keeping it in good condition.
The TPM method is based on the idea that all employees are involved in the maintenance of equipment.
TPM focuses on eight key areas to improve equipment performance:
- Maintenance planning and scheduling: this includes preventive maintenance planning, corrective maintenance planning and ameliorative maintenance planning.
- Training and education: this includes training employees in the skills necessary to maintain and improve equipment.
- Equipment management: this includes analyzing equipment, reducing waste and improving equipment availability.
- Employee participation: this involves employee participation in the maintenance and improvement of equipment.
- Performance indicator management: this includes monitoring and analysis of key performance indicators related to maintenance.
- Inventory management: this includes managing inventory of spare parts and maintenance supplies.
- Safety, quality and environment: this includes implementing safety, quality and environmental practices to improve equipment performance.
- Continuous improvement: this involves putting processes in place to identify and resolve problems and continuously improve equipment performance.
For maintenance management is it ready to use Excel or Yuman?
There are many advantages to using a CMMS such as Yuman for maintenance management.
Excel is a popular spreadsheet tool that can be used for planning and tracking maintenance tasks. It is easy to use and can be customized to meet specific business needs. However, Excel can quickly become complex and difficult to manage for companies with high maintenance requirements. It can also be difficult to track data and establish key performance indicators (KPIs) with Excel.
A CMMS like Yuman is maintenance management software designed to manage a company's maintenance tasks. It is often more comprehensive than Excel, and can include features such as preventive maintenance planning, inventory management, quotation and invoice management, downtime tracking, KPI management and more. It also allows you to centralize a company's maintenance information and make it accessible to all relevant employees.
It's a great way to manage your maintenance activities.
It is therefore prerequisite to use a CMMS like Yuman for companies with large maintenance needs and wishing to have a comprehensive tool to manage maintenance tasks, while tracking key performance indicators. While for lesser maintenance needs, Excel may be sufficient. It is important to choose the tool that best suits your specific needs.
The key to success is to choose the tool that best suits your specific needs.
To conclude, ChatGPT, the Yuman CMMS in two words, what is it?
Efficient optimization.