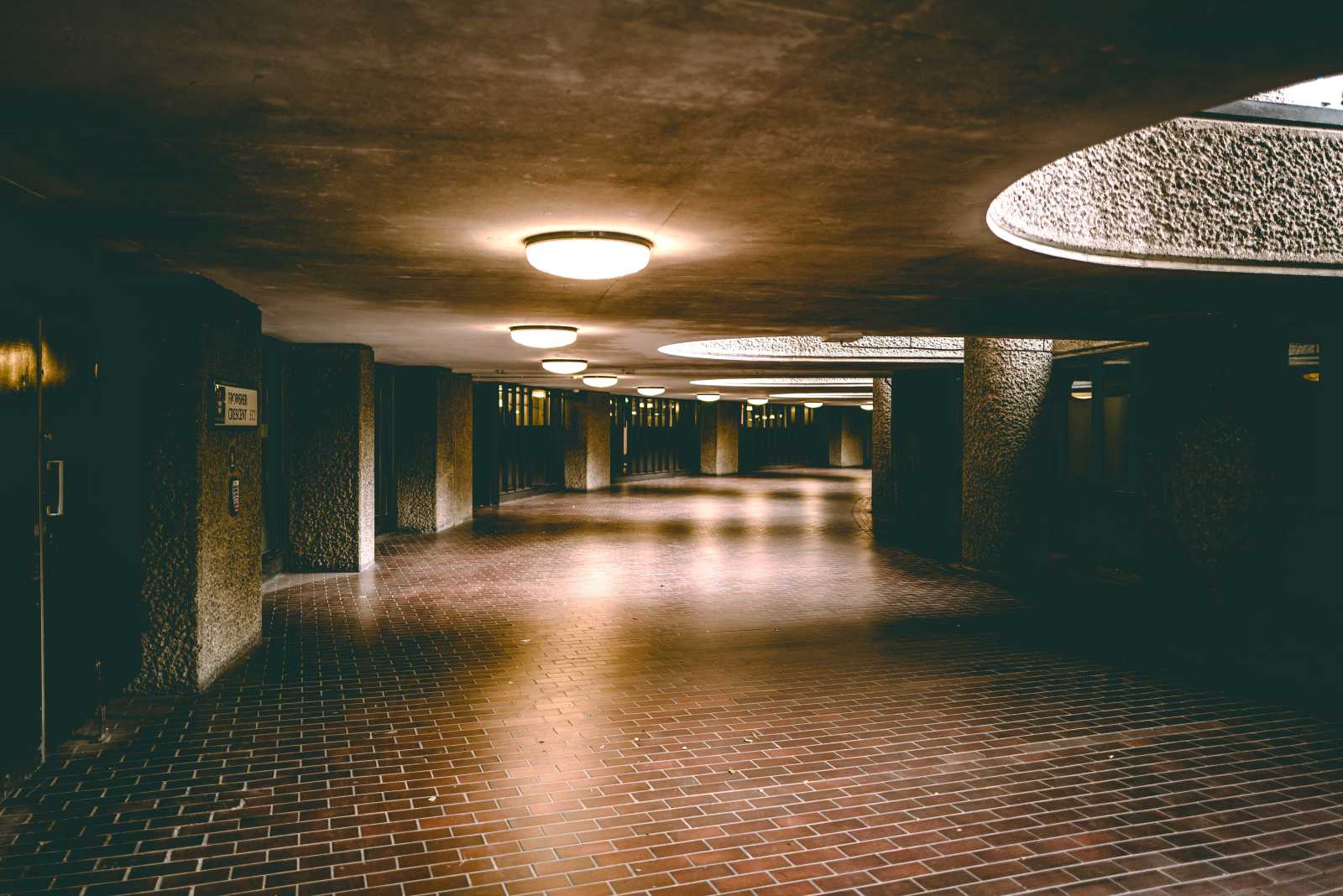
Regulatory controls and audits in Europe - Episode 1: Belgium
Wednesday 08 april 2020
Controls, audits, regulatory inspections of technical installations in buildings... sometimes difficult to find your way around. However, the property manager must ensure that they are properly carried out by a body with the necessary authorisations and that they are carried out at regular intervals.
Which law applies to each technical installation? Which inspection body is competent? How often are inspections carried out? How will CMMS promote compliance with regulations?
Our European tour of real estate regulations starts in its heart, Belgium. We will focus on the technical installations that are essential to the functioning of a building:
1. Lifts and freight elevators
2. The heating
3. Fire-fighting devices
4. Electrical installations
5. Security installations and alarms
Belgian law defines work equipment as all machines, appliances, tools and installations used in the workplace and in the course of work. Their use includes commissioning or decommissioning, transport, repair, transformation, maintenance and servicing, including cleaning. These activities are regulated by the law mentioned in Book IV of the Code of Wellbeing at Work.
In order to prevent incidents and avoid any consequences for the safety and productivity of workers, these installations are subject to periodic technical inspection regulations, which subsequently lead to regular maintenance.
However, the vast diversity of the devices also implies variability in the regulations concerning the nature and periodicity of inspections, specific to each device. This is difficult to understand, especially since the regulations may differ slightly in our three regions.
Being equipped with a CMMS solution will enable the facility manager to reference all his obligations in relation to his installed equipment base, and to check at any time in the blink of an eye whether they are being properly complied with and, if necessary, to quickly remove any alarms or delays.
List of regulatory controls by equipment
The control of a piece of equipment is the set of checks to be carried out on all its constituent parts that may wear out, deteriorate or see their behaviour drift over time. In the vast majority of cases, this inspection must be carried out by an approved organisation, expert in its field and independent of the maintenance company that has been entrusted with the maintenance and repair of the technical asset.
In this document, we offer you a list of the main installations that must undergo a periodic inspection, carried out by the installation manager or the authorised representative. For each inspection carried out, a report must be drawn up and entered in the safety register, which contains the dates of the inspection and the findings made. The register must be permanently accessible to the Mayor and the competent authorities.
1. Elevators and hoists
The Royal Decree of March 2003 concerning the safety of lifts requires a technical inspection to be carried out by an External Service for Technical Inspections in the workplace (SECT). It is carried out every 6 months if the maintenance company is ISO 9001 certified, otherwise every 3 months. A risk analysis is also carried out every 10 years.
Lifting equipment, cranes, hoists and other elevators are subject to quarterly inspections in accordance with articles 280-281 of the General Regulations for the Protection of Work (RGPT).
When these devices are rarely used and exclusively intended for the transport of goods, the SECT in charge reduces the frequency of inspections by adapting to the rate of use of the equipment. However, the interval between two visits must not exceed 12 months.
2. Heating installations
In Flanders:
The decree of the Flemish Government of December 2006 requires periodic control:
- Once a year for liquid fuel installations.
- Every two years for gas boilers.
- An external audit must also be carried out every 5 years if the power of the installation is less than or equal to 100 kW and every 4 years if the power is greater than 100kW.
☞ Fuel oil tanks of less than 6000 litres:
- Only once during commissioning for aerial tanks. However, Article 6.5.5.4 of Vlarem requires the operator to ensure that the installation is in good working order and that any contamination of the environment is prevented.
- Every 5 years for underground tanks. Tanks with a capacity of less than 5,000 litres that are not equipped with a permanent leak detection system are subject to an annual inspection.
☞ Fuel oil tanks of more than 6000 litres:
- A visual inspection must be carried out for aerial tanks every 3 years.
- Every year for tanks installed in a prevention zone for steel and reinforced thermosetting plastic tanks. Every 2 years for tanks located outside the prevention zone.
In Wallonia:
The Walloon Government's decree of January 2009, in turn, provides for periodic inspection obligations, which are as follows:
- Once a year for liquid fuel installations
- Twice a year for gas boilers if the output is > 100kW and 3 times a year if ≤ 100 kW. A thorough diagnosis is required if the boiler is more than two years old, but also two years after any modifications.
☞ Fuel oil tanks:
In the Walloon Region, the inspection of fuel oil tanks is compulsory only for those over 3,000 litres. The periodicity varies according to the type of tank:
- Aerial: visual inspection every 10 years
- Aerial but not accessible and underground piping: every 10 years
- Buried single-walled and aged 10 to 20 years: every 10 years
- Buried single-walled and aged 21 to 30 years: every 5 years
- Buried single wall over 30 years old: every 3 years
- Buried double wall: Every 10 years
For underground tanks, an ultrasonic leakage test must be carried out no later than 10 years after the operating permit.
Brussels Region:
The Government Decree of Brussels Capital of June 2010 stipulates the following control frequencies:
- Once a year for liquid fuel installations
- Every 2 years for gas boilers
- A single in-depth diagnosis is required for devices 15 years of age or older.
☞ Fuel oil tanks:
- Aircraft not equipped with a double wall: every year
- Aircraft equipped with a double wall: every 5 years
- Underground not equipped and over 10,000 litres: Every year
- Underground unequipped and less than 10,000 litres: Every year
- Buried equipped and above 10,000 litres: Every 3 years
- Underground not equipped and less than 10,000 litres: Every 3 years
In Flanders, Wallonia or the Brussels region, these checks must be carried out by a certified technician. In the case of fuel oil tanks, they result in the creation of a certificate to be given to the owner as well as the placing of a coloured plaque on the tank.
3. Fire-fighting devices
Fire extinguishers must be checked annually by the maintainer.
For other first intervention equipment, monthly visual checks on the reels must be carried out internally by the First Intervention Team (FIT). However, every 3 years, the Regional Fire Service carries out a check of the axial feed reels and hydrants on the site. This audit becomes annual if the installation is supplied by a booster set.
Similarly, an inspection of the installations takes place once a year by a specialised company where the valves and seals are examined as a whole.
As you may have guessed, these regulations are dictated by the RGPT.
4. Electrical installations
According to the Royal Decree of 28 April 2017 establishing Book III of the code of well-being at work, those responsible for electrical installations in the workplace are obliged to:
- Possess a compliance report from an approved body
- Conduct a risk analysis and assessment
- Provide for the necessary preventive measures
- Provide for periodic inspections
In all high-voltage installations, an accessible register shall specify the previous checks carried out. They are carried out once a year by a SECT, art. 262 of the RGPT. A monthly surveillance visit must also take place, according to article 265 of the RGPT.
Article 267 of the General Regulation on Electrical Installations (RGIE) provides that a member of staff may carry out a quarterly surveillance visit, provided that he or she is authorised to enter high-voltage installations by obtaining BA4/BA5 training.
Low-voltage installations: Every 5 years a SECT carries out a legal inspection of the entire electrical installation, including the heating system.
Domestic low-voltage installations: The RGIE expects domestic installations to be inspected every 25 years and also when a house is sold.
5. Security installation and alarms
Control of an anti-intrusion alarm system: annual control by a company specialized in this sector of activity. The inspection will cover the verification of control systems, battery charger-battery systems and warning means.
Inspection of fire detectors: once a year by a specialised body, the inspection will follow NBN S21-100 with the testing of detectors, push-buttons and warnings, as well as a review of the operating flow chart.
A CMMS for perfect compliance with controls
Thus, the owner or manager in charge of the technical installations of a building is confronted with a wide range of regulations. The latest-generation Computer-Aided Maintenance Management Solutions (CMMS), like Yuman, will considerably lighten the burden of responsibility on the manager, with regard to compliance with these legal obligations. Otherwise, the risk is that the company may incur substantial financial penalties or even civil and criminal liability.
The various pieces of equipment and the mandatory controls associated with them constitute a considerable amount of information that must be easily manageable. Without the contribution of specialized tools such as CMMS, which will record, centralize and share it, the facility manager will quickly find himself overwhelmed, putting his company, its users and himself at risk.
A CMMS solution will provide an overview of the equipment fleet, a history of events that have occurred, maintenance tracking and control schedules:
- Inventory of equipment for a perfect knowledge of the park
- An up-to-date calendar of maintenance actions for good maintenance
- Updated schedule of compliance checks
- Collecting and sharing this information in real-time
- Easier communication with audit firms
- Facilitated communication with all stakeholders
- Writing analytical reports accessible to all stakeholders
Yuman can also be used to digitise regulatory forms of any kind: boiler maintenance certificate, tank leakage control, lift compliance, electrical installation audit, etc.
This essential functionality makes it possible to fill in the form on the move, directly from the field. Once completed, the document, attached to the equipment, is instantly accessible via the application for all concerned and authorized parties. It can also be sent by email. No information needs to be re-entered. No risk of loss or alteration of the document. No need to scan a paper document for archiving.
The essential benefits of a state-of-the-art CMMS such as Yuman include the creation of recurring control schedules, direct recording of actions carried out, real-time monitoring and sharing of audit reports.
In the regulatory field, as well as in the maintenance field, Yuman becomes essential.