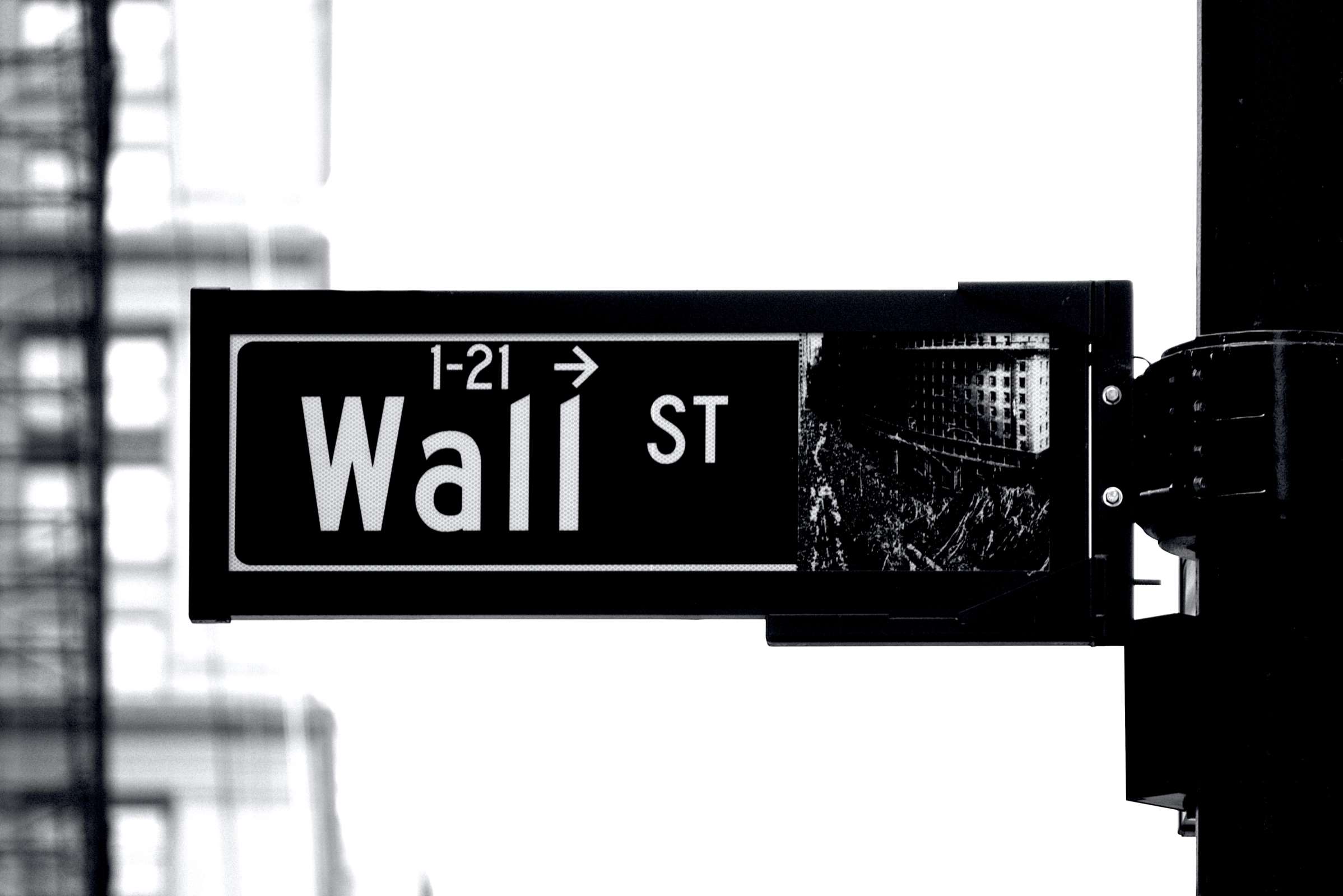
The ROI of a CMMS
Sunday 05 december 2021
INTRODUCTION
One of the KPIs - Key Performance Indicators - that is particularly followed by management teams is the company's return on assets. Simply put, return on assets measures a company's earnings divided by the total value of its assets, a calculation actually used by many Wall Street financiers when examining the value and stability of a company. Higher return on assets figures indicate more profitable, well-run and stable companies. However, since we're talking about maintenance and reliability, what impact do they have on the return on assets calculation? Is it better to reduce expenses or increase revenues? These two strategies are the key to profitability. Wouldn't the implementation of a CMMS allow to win on these 2 fronts?
REDUCTION OF EXPENSES
This method is familiar to most maintenance and reliability departments. The main areas of expense control are labor, spare parts management and good control of maintenance contracts. A related expense control is the company's energy consumption. Since savings become profits, expense control is a key factor in increasing profitability. However, it obviously cannot be the only way.
INCREASING REVENUES
Revenue can be increased by increasing capacity while maintaining fixed costs. Since the company has already invested in assets, increasing the availability and efficiency of those assets while controlling fixed costs will directly increase profitability. This path has a very positive effect on increasing the return on assets. This is especially true in markets where demand is high and all products produced can be sold. It also has an impact in markets where demand is capped. In this case, increasing efficiency and effectiveness will lower fixed costs.
If an organization is maintenance-driven, it can still contribute to profitability by controlling expenses. However, the impact may be greater if the organization focuses on equipment uptime. In fact, the contribution to profitability can increase fourfold if an organization focuses on equipment availability or uptime rather than controlling maintenance costs.
A maintenance department can have a significant financial impact on a company's profitability. If an organization can adopt the right focus, maintenance and reliability can become a business asset, through the increased competitiveness it can enable.
In short, focusing on maintenance controls, as well as maintenance and reliability expenses, eliminates waste, which is the premise of a lean operation. The next step in the evolution is to focus on equipment uptime or availability. This increases the company's capacity. As a result, the company can do more with the same resources or the same thing with fewer resources. Focusing on EAM, or increasing equipment efficiency, maximizes capacity and finances. Understanding this is important for companies wanting to remain competitive in the coming decades.
Some companies are beginning to understand this clearly, as evidenced by some of the latest maintenance KPIs they are using. For example, they are measuring maintenance costs (or MC) as a percentage of estimated replacement value (or ERV) of assets. The cost of maintenance compared to the estimated replacement value is calculated by dividing the total maintenance costs by the total asset value. This percentage is then used to assess whether the appropriate level of expenditure is being made on maintenance and reliability.
UNDERSTANDING MAINTENANCE & GMAO
Maintenance and reliability are major issues for companies that many managers have not yet fully taken into consideration. To complicate the situation even more, they think they have understood the maintenance function... This lack of understanding is highlighted by the large number and diversity of methods currently used to organize and perform maintenance in companies. Most company and plant managers have focused on managing operations or manufacturing, while the management of more technical disciplines such as maintenance has been ignored or placed on the back burner. Maintenance, for example, has been seen as a necessary evil, like an insurance policy, where the money involved is merely an expense in their eyes.
When companies looked more closely at the maintenance function, they discovered that maintenance represents between 15 and 40 percent of the total cost of the product. They then deduced that the savings made in maintenance were an important lever for reducing production costs. If we take the typical profit margins of manufacturing companies, we can conclude that one euro saved on maintenance costs contributes as much to the company's profits as 3 euros of new sales. Scaling up, in large companies, reducing maintenance expenses by one million euros contributes as much to profits as increasing sales by 3 million euros. In the competitive markets that all companies face, it is much easier to improve maintenance and reduce unnecessary maintenance expenses by €1 million than to find €3 million in new sales.
The implementation of software, through the cost reductions it will bring, will be a considerable asset for organizations in increasing their productivity.
We will now present guidelines for estimating the possible financial benefits that a company can obtain by implementing improved maintenance policies and practices, starting with the implementation of a CMMS system.
MAINTENANCE COST REDUCTION
This section analyzes cost reduction in four areas necessary to manage the maintenance of an organization's equipment:
- Reduction of labor costs
- Reduction of spare parts costs
- Reduction of project costs
- Reducion of downtime and unavailability costs
Reduction of labor costs
Maintenance productivity in most companies averages 20-30%. This translates to about 2 hours per 8-hour shift of hands-on activity. Most productivity losses can be attributed to the following reasons:
- Waiting for parts
- Waiting for information, drawings, instructions, etc.
- Waiting for equipment to stop
- Waiting for rental equipment to arrive
- Waiting for other trades to finish their part of the job
- Running from one emergency to the next
While 100% productivity is an unrealistic goal for any maintenance department, a more realistic 80% is perfectly achievable.
Maintenance technician productivity can be improved by focusing on basic management techniques, such as:
- Planning work in advance
- Planning jobs and coordinating schedules with production
- Scheduling parts for just-in-time replacement
- Coordinating tools, rental equipment, etc.
- Reducing emergency work to below the 15% level by implementing perfectly matched periodic maintenance plans
With the help of IT, the planning time per job is reduced, allowing more jobs to be planned and coordinated. This directly allows more time to be spent on preventive maintenance activities, thus helping to reduce the number of emergency activities and breakdowns. The result is increased productivity through reduced downtime.
Organizations that successfully implement a CMMS solution report an increase in productivity of up to 30%!
Reduction of spare parts costs
Spare parts costs are related to the frequency and size of repairs performed on company equipment. The number of parts, as well as stocking policies, purchasing policies and general inventory management practices, contribute to overall spare parts costs. With little attention paid to spare parts in some companies, inventories can be 20-30% higher than necessary. This amount increases inventory carrying costs and makes spare parts management unnecessarily expensive. The inability of stores to meet maintenance department needs leads to the creation of "pirate" or "illegal" depots for spare parts just in case. With spare parts costs accounting for 50% of total maintenance costs, there is a need to improve this area.
Good inventory control allows companies to reduce the value of inventory while maintaining a high level of service. In this area, users of CMMS solutions have seen an average 20% reduction in the cost of storing and managing spare parts.
Reduction of project costs
In many companies, maintenance is involved in project, shutdown or refurbishment activities. These activities, if not properly controlled, can have a significant impact on a company's production capacity. This is because these activities are typically performed with the equipment in a shutdown state, when there is no production. Therefore, any time that can be eliminated from the project, shutdown or refurbishment can be converted back into production time. In the refining or power generation sector, for example, the cost of an extended shutdown is prohibitive.
Improved planning and coordination can be achieved through a CMMS/EAM system. These efforts will often reduce downtime, even if the company is currently using a project management system. Users of CMMS/EAM systems have reported an average 5% reduction in downtime.
Reduction of downtime and unavailability costs
These costs represent the real savings for a company committed to improving its maintenance policies and practices. The cost of equipment downtime can range from several thousand dollars per hour to hundreds of thousands of dollars per hour. For example, for a company with several production lines in its plant, the downtime for each of them can be worth €1 million for 24 hours.
In some companies, downtime levels can reach 30% or more. Downtime results in lost sales opportunities and unnecessary capital equipment expenditures. It typically places the company in a weak competitive position. By dedicating the company to implementing good maintenance policies and practices and using the CMMS/EAM system as a tracking tool, equipment downtime can be dramatically reduced. CMMS/EAM users have been able to reduce equipment downtime losses by an average of 20%.
CONCLUSION
There is a clear relationship between maintenance and company profitability. Thus, the implementation of a web-based, mobile, efficient CMMS, which all members of your maintenance team quickly adopt due to its ease of use and intuitiveness, will very quickly be able to reduce maintenance-related expenses, while improving the quality of service offered to production in terms of responsiveness and availability of technical assets. This will increase the profitability of the organization.
Back to the articles