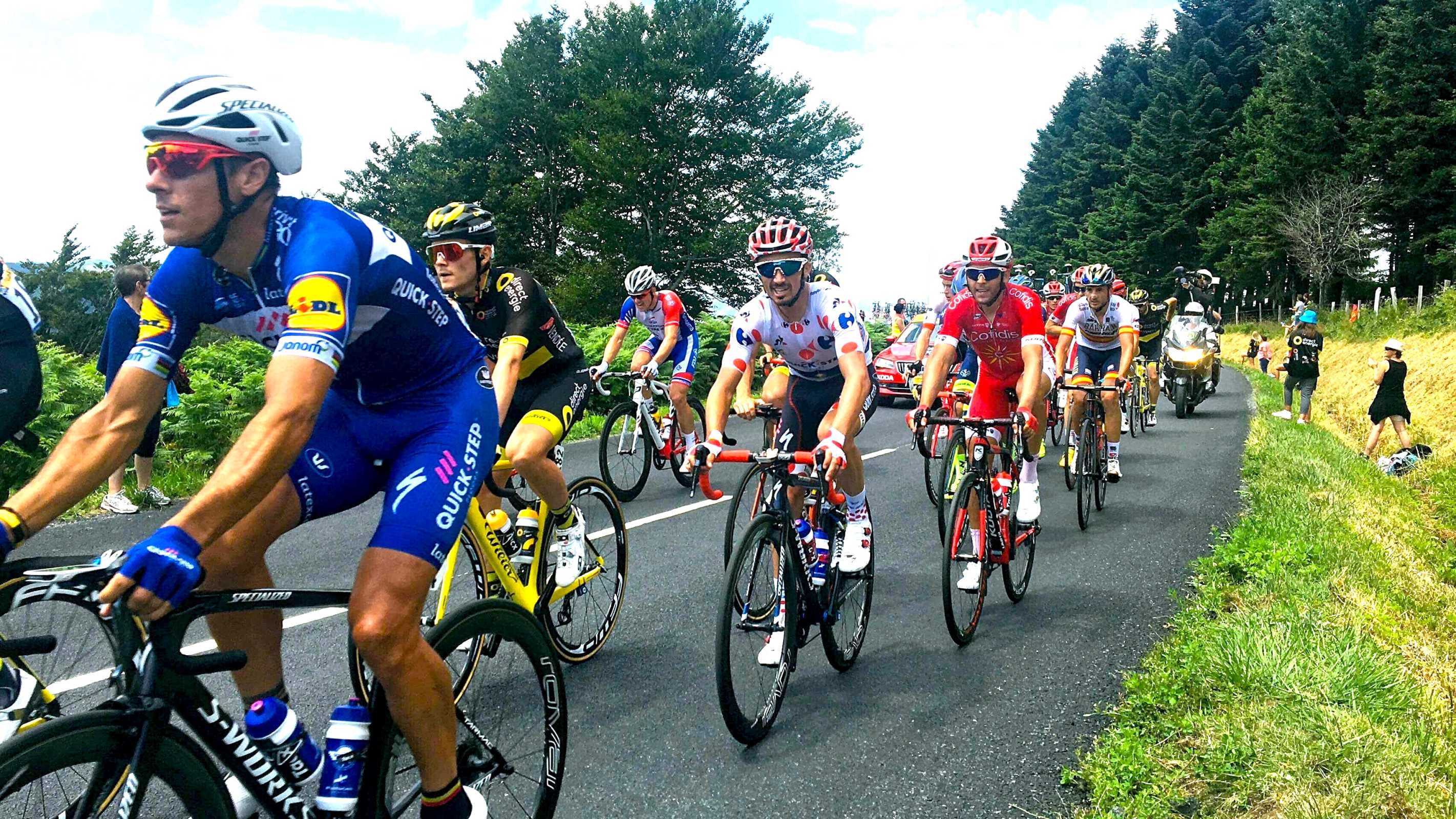
Regulatory controls and audits in Europe - Episode 4: France
Thursday 30 april 2020
After having crossed Belgium, Switzerland and the United Kingdom, whose regulations governing the maintenance and inspection of technical equipment are now no longer a secret for you, we are continuing our European tour via France. And it is without EPO or amphetamine that we are bravely attacking this new stage.
> CMMS and regulatory controls in Europe
In France, mandatory technical inspections of equipment are regulated and provided for by law. They guarantee the health and safety of the occupants of a building. Various pieces of legislation impose regulations for the periodic inspection of installations on the owner, the operator or the employer. Depending on the devices concerned in this article, we will refer to :
- Labour Code which stipulates the measures to be carried out by the employer to ensure the safety and health of workers
- Code de la Construction et de l'Habitation which defines the steps to be taken by the operator of the ERP (Établissement Recevant du Public), to guarantee public safety
- Environmental Code that defines the environmental performance requirements of equipment, in particular those related to heat production.
These inspections must be carried out by a State-recognised organisation but may also in certain cases be carried out by a competent person internal or external to the company, provided that he has received the required training. After each inspection, an action report must be kept, which will be recorded in the safety register.
Following the examination, the operator or the owner of the site is kept informed if a repair or replacement is necessary. In this case he will have to call in a maintenance company to lift the reserve. A maintenance contract fixed in advance between the two parties is strongly recommended. It will allow long-term maintenance of the equipment to ensure its compliance, and will simplify periodic inspections.
As usual, we will detail the regulations in terms of maintenance and control for the following technical installations:
- Elevators
- Heating installations
- Electrical installations
- Fire-fighting equipment
- Security devices and alarms
The regulatory framework of control obligations imposed on the owners or operators responsible for such equipment is substantial and can be difficult to manage. We will see how a CMMS will, through the many functionalities it offers, help the people in charge to monitor the equipment and comply fully with the regulations.
Regulatory controls
Compulsory roadworthiness testing is the set of checks to be carried out on equipment according to the requirements of the legislation in force, at prescribed time intervals. Its purpose is to approve the conformity of equipment whose main purpose is the safety of persons. It can be carried out in different ways: visual inspection, tests, etc.
Lifts
Article R125-2 of the Construction and Housing Code (CCH) requires a periodic technical inspection of lifts every 5 years by an approved body.
For lifts the CCH also makes it compulsory to have a maintenance contract with a maintenance company which will carry out the periodic maintenance for:
- Checking the lifts for proper functioning, every 6 weeks
- Check and control the condition of the cables every 6 months
- Carry out tests of the parachute system annually
The imperative nature of these measures, maintenance every 6 weeks and checks every 5 years, makes French regulations one of the strictest in Europe.
Heating installations
Articles L.224-1 and R.224-41-9 of the Environmental Code (EC) require an annual inspection of boilers, all combined (gas, fuel oil, biomass, multi-fuel), and whose power is less than or equal to 400 kW. The energy and environmental performance must also be assessed. The maintenance certificate must be kept for at least 2 years.
For installations with an output of more than 400 kW and less than 20 MW, the inspection must take place every 2 years. Articles R.224-31 to R.224-41 of the EC define this periodicity but also the verification criteria such as :
- The control of the boiler efficiency
- The control of measuring devices
- Checking the operating status
The concentration of air pollutants must also be measured and the maintenance manual of the heating system updated.
Underground fuel oil tanks are subject to a five-year inspection during which leakage and/or piping tests are carried out.
Boiler inspections are carried out by a competent person from a specialized company approved by the State. These technicians are most often employees of heating companies who are responsible for these inspections.
Electrical installations
The permanent electrical installations of a building and safety lighting are subject to the Labour Code (CDT) and the Building and Housing Code, which stipulate an annual periodic inspection by an approved body.
Once again, the checks must be recorded in a safety register.
Fire-fighting systems
Sprinklers or fixed water sprinkler equipment must follow the CHC requirements. They are inspected once a year by a competent professional and a thorough inspection must be carried out every 3 years by an approved external body to ensure the conformity of the equipment.
Mobile fire extinguishers are covered by the same code and are inspected annually by a competent technician.
Security and alarm installations
The CDT and the CHC again dictate the frequency of mandatory checks. For Fire Safety Systems (FSS), the audit must take place annually.
Since 2015, it has been mandatory to have at least one smoke detector in a building (all types: ERP, tertiary office building, private home, etc.) but no technical control is set by law. However, ERPs are still obliged to establish a maintenance contract with a maintenance company specialising in the field, which generally carries out functional tests of the equipment every 6 months. This maintenance contract and a description of the maintenance and operating conditions must be attached to the ISS security register.
CMMS, the appropriate tool to meet all these obligations
The purpose of these technical inspections is to ensure the safety of people on the premises by guaranteeing the conformity of the equipment essential to a building. To facilitate this maintenance, the authorities also recommend establishing a maintenance contract with maintenance companies. They then play a key role in facilitating periodic examinations.
Whether it concerns inspection or maintenance, a mandatory report must be drawn up after each intervention. It allows the maintenance follow-up of the equipment. For the technical inspection it will be recorded in the safety register and for maintenance in the maintenance logbook. They are defined by the French government as follows:
- The safety register is a document in which are recorded all the interventions carried out concerning the safety of the establishment. It is required for all ERPs
- The maintenance logbook of a piece of equipment is a file in which the parameters related to its operation and the maintenance measures carried out are recorded. It becomes mandatory whenever equipment involves the safety of people (e.g.: boiler room, lifts etc.).
It is essential to keep these files up to date. In the event of an incident, they make it possible to justify to the competent authorities that the operator, employer or owner has implemented the necessary means to guarantee the safety of the people concerned. Otherwise, it is their civil or criminal liability that may be incurred.
In the vast majority of cases, without the appropriate tools, compliance with these obligations proves to be complex or even impossible. The operator in charge of the installations must be able to keep an up-to-date record of each piece of equipment in the various buildings and to easily identify the inspection intervals imposed in order to comply with them.
Likewise, he must be able to easily retrieve the reports of the interventions carried out and make them accessible at any time to the stakeholders concerned, at the risk of receiving heavy penalties.
The solution? Equipping yourself with a CMMS tool
A CMMS solution makes it possible to centralize all the data in a single place, giving the possibility to perform :
- A history of the sites and their equipment fleets for an exact knowledge of the sites
- A regulatory form for each piece of equipment to identify the applicable requirements
- The schedule of maintenance interventions for a maintenance follow-up
- The planning of technical control interventions to comply with legislation
- Collect and share information in real time at any time from within the application for better internal communication
- An analysis report that can either be sent directly from the application to the stakeholders: owners, operators, recognised organisations, etc., or be published on a portal directly accessible to these same stakeholders.
These numerous functionalities offered by a modern, therefore mobile CMMS, make it an essential tool for meeting equipment maintenance and control obligations, as imposed by French law.
By the way, our ambition is to offer an unequalled user experience. Check it out immediately: try CMMS for free. Within 2 minutes, by the time you create your account, you'll discover what's newest in this category of software.
You can also benefit from a demonstration led by one of our consultants: book a videoconference
Good discovery and see you soon !
You will also be interested in reading :
📰 You will also be interested in reading about:
Regulatory controls and audits in Europe - Episode 1: Belgium
Regulatory controls and audits in Europe - Episode 2: Switzerland
Regulatory controls and audits in Europe - Episode 3: The United Kingdom
Keynote CMMS Yuman
Back to the articles