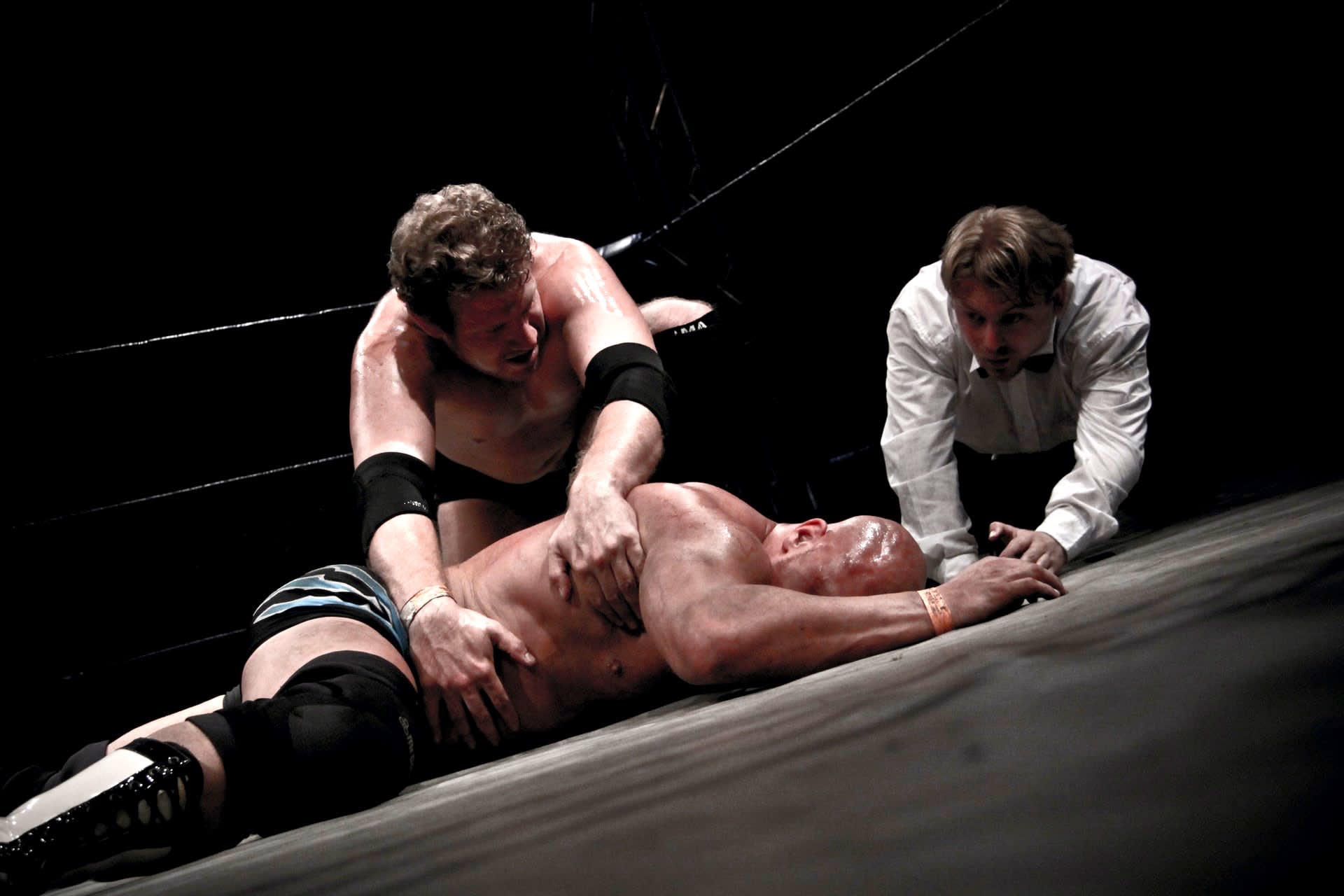
CMMS wins Excel by KO!
Tuesday 31 march 2020
With the invention of Visicalc in 1979 by Dan Bricklin, a program that will be at the origin of the success of the Apple II, a new family of software is born. According to Wikipedia: "A spreadsheet is a table (or grid) of information of all kinds: industrial, scientific, commercial, accounting, financial, statistics, business data, etc.. “. Lotus, Multiplan and then Excel, which definitively took over the market in 1985, participated in their time in the immense adoption of spreadsheets by millions of companies of all sizes throughout the world.
But beware! Spreadsheets, which are now more than forty years old, have since been largely overtaken by the latest generation of business solutions. Continuing to use them for what they're not made for can pose a real danger to the enterprise: compartmentalization and disorganization of scattered information, lack of collaboration, no mobility, rudimentary functionalities, limited multimedia capabilities, leading to a lack of productivity, major data security risks and loss of competitiveness.
We will see in this article that this is particularly true in the maintenance world where the latest generation web & mobile CMMS solutions have definitively retired spreadsheets.
The 8 limits of Excel
1. Centralize data: sites, installed equipment, spare parts, etc.
One of the main drawbacks of Excel is the perpetual transcription of data. Someone has to constantly collect and transmit all the information to be stored whether it is a phone call, a paper work order, a fax or a conversation in the field. Thus, the number of re-entries in Excel is incredibly high: even having automated some tables and formulas, it remains a very tedious step where the risk of error is high, especially when large amounts of data have to be processed. Not only do you lose precious time, but this leads to desynchronization of information, which leads to forgetting and losing data.
And with a CMMS: The real-time transmission of information via a centralized database means that you do not have to continuously manage the flow of information and requests because users can consult and feed all essential data from sites, equipment and spare parts themselves. For example, for a service request from an occupant or site manager, the system will send the request to the manager who will automatically receive a notification. The manager will then be able to consult, respond and immediately assign the task to the nearest, most competent, readily available technician to deal with the request as quickly as possible, via his user interface.
2. Optimize the planning of maintenance missions
Planning maintenance work in advance is essential to be able to organise your planning and manage your staff optimally. It is also important to be able to react quickly to unforeseen events. At this level, Excel is only good for serving as a fixed calendar where you can note the dates of upcoming interventions.
And with a CMMS: By connecting to a dynamic schedule, you can add and move your interventions according to your constraints. Teams are then automatically informed via their mobile phones of any changes to their schedule. The smooth running of your operations can be consulted in real time, with each technician constantly updating the status of his tasks on his mobile.
3. Communicate with the field in real time
Communicating with your teams in the field is essential to coordinate your actions and transmit direct orders. Using Excel, it is impossible to establish an effective communication method.
And with a CMMS: No more forgetfulness and loss of time! You can send all the information you want via the application to make life easier for your technicians: equipment manuals, advice and specific indications, estimates and forms, etc. They will then be immediately alerted of your messages by a notification.
4. Collecting information from the field
When a maintenance operation is in progress or completed, it is essential to provide the information and documents necessary for its closure, photos, balance sheet, list of actions carried out, measurements taken, spare parts or consumables used, customer signatures, but also invoices, customer feedback, specific forms or the need to order new spare parts or draw up a quote. For all this Excel will not be of any use. Everything will have to be written down on a paper document and then re-typed!
And with a CMMS: By using a recent CMMS software, you have a mobile application allowing the technician to collect all this information from the field. He can do it connected or not from a simple mobile phone. The difference between Excel and CMMS is immense here ...
5. Communicates with customers and requesters
Good customer relations are essential. For this, an active communication between your company and the requesters must be established by giving them access to the intervention schedules on their site, to their quotations and their contracts. With Excel, it is only possible to send them the files by e-mail. This represents a huge amount of work since all files must be retransmitted each time a document is modified or added to the folder.
And with a CMMS: It is possible to create a specific account for each customer allowing them to access all the information you want to share with them. All they have to do is access their account online to track and manage their service requests.
6. Historize and capitalize on the interventions carried out
With Excel you will continue to use paper work orders that will very often be thrown away or stored in a cabinet with thousands of others. Finding them to reuse information or an associated document becomes very quickly complicated. Even if you save these data in Excel, they are still subject to errors or deletions. This can become even more of a concern when it comes to quotes, contracts or warranties for your equipment.
And with a CMMS: all information is recorded and stored online, guaranteeing its traceability, durability and future reuse. The interventions carried out update the maintenance plan, the items used are decremented from stock, and the indicators and statistics are built automatically. Moreover, as the data are always linked to each other, their quality is automatically reinforced. In this way, you can record past tasks without additional processing, easily manage work in progress, look to the future and anticipate future needs directly in the system with complete peace of mind.
7. Access information anywhere, from any device, at any time
The need to access his schedule, the history of an equipment, the user manuals, the database of materials, stocks and customers is permanent for any technician on the move. Finding this information on an Excel file when you are on an intervention without having access to a fixed workstation is almost impossible and very frustrating. For you, it means extra trips back and forth, constant phone calls with your technicians or the use of a multitude of disparate tools to explain what needs to be done.
And with a CMMS: With CMMS, whether you are a manager or a technician, you can connect to your user interface from any fixed or mobile device. This gives you access to all the information you need, anytime and anywhere, and with the best mobile applications you can access it even off the network. So you and your team have all the essential data to manage interventions and requests autonomously.
8. Generate reports and have KPIs at your disposal
Having an overview of all the indicators of your business is essential if you want to be sure you are making the best decisions for your company. Gaining a global view of your business is not easy - if not almost impossible - from Excel. Even if you are able to produce reports and dashboards, they will need to be continually updated and recreated when new data enters the system.
The CMMS answer: reports and dashboards can be generated automatically, in real time, from data collected from the field. KPIs, Key Performance Indicators, are thus permanently accessible. You can use these reports to facilitate your decision-making and adapt your maintenance or investment strategy. Managing your teams, monitoring your equipment, analyzing the overall performance of the service and the contribution of each individual becomes child's play with a CMMS offering these functionalities. You can even consult these statistics and dashboards when you are in the field, further strengthening your control.
CMMS, the best value-added solution
So yes, if Excel can still be used to make basic schedules or equipment lists, it can only be a short-term temporary solution that should quickly lead you to adopt a true CMMS. Software must be used for what it was designed for. And to manage your maintenance operations, nothing can replace dedicated software specially designed for that purpose: CMMS?
However, it must be said that not all companies have yet taken the plunge. The time needed to choose a solution, implement it, load data and train teams are the major obstacles. And it is true, although they are supposed to facilitate the work of maintenance operators, that some older generation solutions, not very adaptable, with rudimentary mobility, complex and cumbersome, will not be able to meet the expectations of users.
CMMS stands out thanks to its functional completeness, its great ease of use and the quality of its user experience. The startup phase has been particularly careful to make it simple and fast. The possibility of carrying out a complete test before any decision is made, the best maintenance practices it offers, online help, videos, extended configuration that can be directly managed by the administrator, follow-up, advice and support from an expert if necessary, ensure smooth onboarding, allowing the company to fully use the tool in a few days maximum.
In offline mode, the mobile application remains functional with uninterrupted background synchronization, guaranteeing technicians a perfectly fluid use. All information entered, photos, documents, materials used are automatically saved, without having to manually re-enter them in a spreadsheet or CMMS without mobility.
These are essential possibilities, absent from spreadsheets, which give the CMMS a victory by KO and send Excel to the ground!
By the way, our ambition is to offer an unparalleled user experience. Check it out right away: try CMMS for free. Within 2 minutes, the time it takes to create your account, you'll discover what's newest in this category of software.
You can also benefit from a demonstration led by one of our consultants: book a videoconference
Good discovery and see you soon.
📰 You will also be interested in reading :
- CMMS vs. ERP, the Match!
- Do we have to distinguish EAM and CMMS solutions?
- Investing in CMMS in times of crisis
- CMMS: back to the future
- Understanding Computer Assisted Maintenance Management System
- Computer Aided: a whole program!
- No connection? No problem!