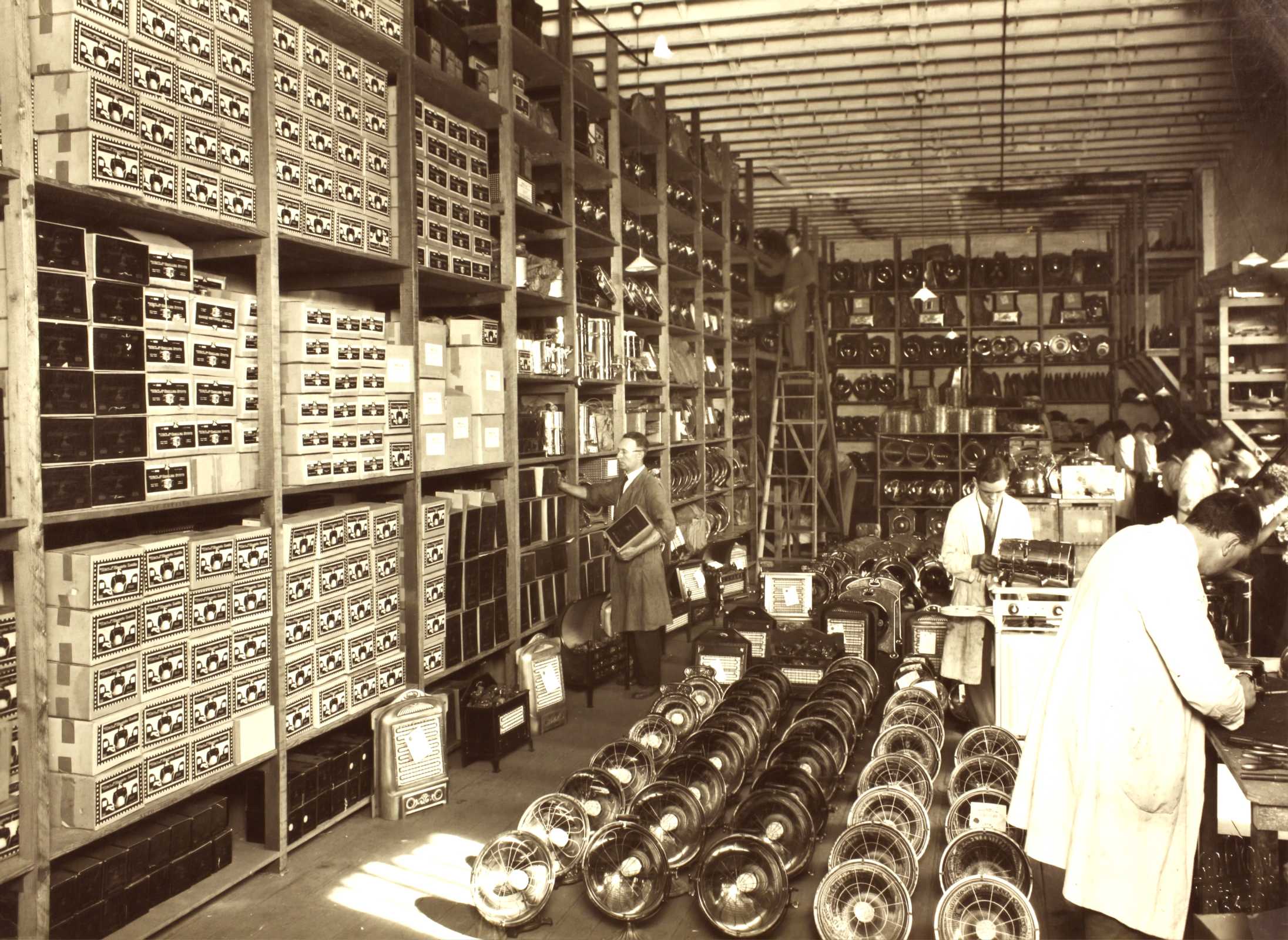
Manage your spare parts with CMMS
Monday 04 may 2020
Spare parts management? Nothing better to occupy your day! This task takes up a considerable amount of managers' and technicians' time and, if badly managed, can put a strain on a maintenance department. Mobile CMMS will once again prove to be a must.
> Why a CMMS for industrial maintenance?
The time it takes for equipment to return to service after failure depends, in most cases, directly on the time it takes to make a part available. The optimisation of spare parts management will therefore be a major lever of maintenance performance.
In addition, inventory and purchasing management represents a major item in the budget, both in terms of ownership and logistics costs: ordering, tracking, administration, transport, reception, storage, handling, etc.
CMMS, or Computer-Aided Maintenance Management, will reduce these costs, while speeding up the availability of parts at the site of the intervention.
Stock coverage: too little or too much
Insufficient stock coverage can lead to a decline in asset availability, resulting in production losses at manufacturing sites or significant delays in the repair of technical equipment such as heating, elevators, access doors in the real estate maintenance world. Conversely, storing a large quantity of parts quickly becomes very expensive, both in terms of storage space and fixed assets.
Reducing these expenses while having sufficient inventory to keep pace with business activity and shortening replenishment lead times are the challenges facing companies' maintenance divisions. In fact, more than 50% of a maintenance budget is spent on spare parts and consumables, of which 20% is wasted on average. These unnecessary expenses are considerably reduced thanks to the implementation of a management system controlling the main areas for improvement :
- Storage of spare parts to be replaced most frequently
- Storage of the right quantities
- Reliability analysis of spare parts
- Optimization of the provision to the technician
- Reduced operational processing times
- Reduced administrative processing times
That's where CMMS comes in.
CMMS to optimize stock levels
CMMS will help companies to manage their stocks, thanks to the real-time updating of incoming and outgoing spare parts, allowing them to anticipate any breakdowns.
Essential for preventive and curative interventions, parts and consumables must be scrupulously referenced in the CMMS with in particular :
- Real-time visibility of the spare parts stock: alert in case of breakage, order in progress, installation on the equipment concerned, etc.
- Precise location in the warehouse
- Management by QR codes with mobile application allowing direct scanning
- Barcode management
- Multi-stock management: stock per site, per vehicle or even specific to each technician.
- Automatic decrementing of the stock when the intervention is carried out
- Alert if the minimum threshold is reached
- Automatic triggering of supplier orders
- Creation of the order item repository
- Detection of the most reactive suppliers
- Automatic valuation of the stock at purchase and sale price
- Comparison of suppliers' prices and delivery times
- Triggering automatic tenders
- History of the parts used on each equipment with their characteristics: date of installation, guarantee, replacement to be provided, etc.
The most modern CMMS are capable of anticipating the need for replacement parts by comparing the state of stocks at a given moment with the forecast of preventive interventions to be carried out. This information comes directly from the maintenance plans.
CMMS knows how to transform a spare part into a component of an equipment, as soon as it is used on a machine to replace the defective part. This new element is then an integral part of the equipment and can be referenced as such, with location, photos, controls, measurements, etc. and if necessary it is possible to associate preventive actions to it.
CMMS to reduce procurement lead times
Nothing is more frustrating for a technician than not finding the item he needs in the warehouse, or finding out that the part he needs for his job has not been delivered on time. There is also an urgent need to eliminate any possibility of countertop pickup, which causes significant loss of time. Of course, judgemental management is not enough to guarantee its customers an optimal quality of service or seamless production. Anticipating the consumption of spare parts is a permanent concern and the stock level must be able to respond to variations in activity. This is particularly true for the mobile teams that most often intervene in emergencies.
Each item in the catalogue is associated with alert thresholds and replenishment quantities that anticipate the replenishment decision before reaching the stock shortage. The CMMS generates the purchase order, sends it to the suppliers and you receive notification at each stage: sent, received, dispatched, received, refused, etc. You then have the same level of information at your disposal as when you place an order on an e-commerce site. You get used to it quickly, don't you? But here, it's completely integrated with your CMMS and your maintenance operations.
The part is in stock, but where? The CMMS has a dynamic search function that will easily find the part and its location. Scanning the QRcode or a barcode will remove the item from stock. This operation will then be automatically recorded and the stock level updated in the application. Rather than wasting a lot of time with a tedious system of recording stock entries and exits, CMMS ensures that technicians have the parts they need for their interventions. Intuitive and immediate, the operation is carried out from the CMMS from its mobile phone.
KPIs for better decisions
- Which parts are most likely to cause a failure?
- Which parts need to be replaced most often?
- Which brands are the most reliable?
- Which suppliers are the most reactive on a certain category of spare parts?
It is essential for maintenance teams to have relevant KPIs that are shared and simple to analyse. Thanks to this enriched information, the team manager will be able to make the best decisions to save and reduce the costs associated with the stocks and purchases of parts.
Analysis of the origin of breakdowns provides essential information on the part in question, the date of its installation and the technician who carried out the intervention. By consolidating information on equivalent equipment, you are able to detect if a specific type of part is causing repeated breakdowns and can act accordingly. In this way, by determining the level of reliability and the cost of the various spare parts, CMMS helps you to modify your supply methods or possibly change suppliers if they do not meet your requirements.
Increase your competitiveness
By entrusting the management of your stocks to your CMMS you are able to :
- Standardize your installed base
- Standardizing suppliers
- Low stock levels and anticipating purchases thanks to the forecasting system
- Position the stores in strategic locations: central, sites, vehicles, etc.
- Reduce or eliminate obsolete spare parts
- Identify frequently defective parts
Standardization of equipment, supplies and suppliers is proving to be an important source of savings and efficiency for organizations. By reducing inventories, procurement lead times and repair times with the help of a stock and purchasing module integrated into your CMMS, you directly increase your competitiveness.
By the way, our ambition is to offer an unparalleled user experience. Check it out right away: try CMMS for free. Within 2 minutes, the time it takes to create your account, you'll discover what's newest in this category of software.
You can also benefit from a demonstration led by one of our consultants: book a videoconference
Good discovery and see you soon !
📰 You will also be interested in reading :
- CMMS & Total Productive Maintenance
- IoT: the bright future of maintenance
- Cosmetic Industry and CMMS
- CMMS for the Food Industry
- CMMS to meet the challenges of the pharmaceutical industry
- CMMS in the medical sector
- Aeronautics industry and CMMS
- FMECA and CMMS: maintenance excellence
- Autonomous maintenance & CMMS
- Why is preventive maintenance a priority?
Back to the articles