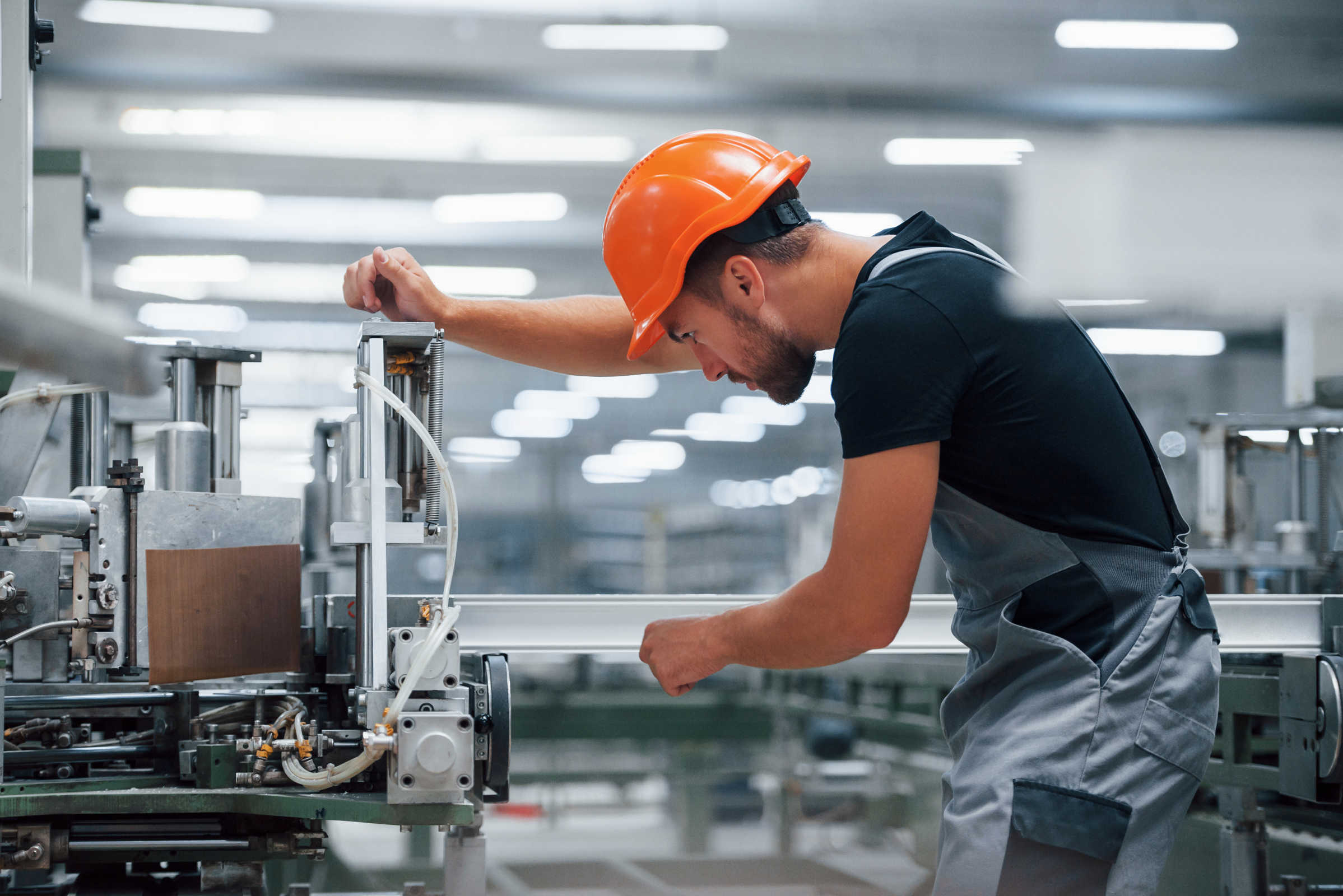
CMMS & Total Productive Maintenance
Monday 13 april 2020
In the industry, the concept of Total Productive Maintenance (TPM), focuses on involving and empowering all company employees in the maintenance of production unit equipment and emphasizes preventive and proactive maintenance techniques. We will discover the importance of CMMS for the success of its implementation.
> Why a CMMS for industrial maintenance?
The objective of Total Productive Maintenance is to improve productivity by reducing machine downtime. Such a program will thus make it possible to move towards a 100% equipment availability rate: elimination of faults, stoppages, breakdowns, degraded operation and, last but not least, accidents.
The TPM, which essentially consists of moving from reactive maintenance to preventive and proactive maintenance, will have the following benefits:
- Reduction of unplanned downtime
- Increased employee confidence levels
- Reduced customer complaints
- Establishment of a clean and orderly workplace
- Reduction of accidents at work
- Increased sense of belonging among employees
- Reduction of production costs
- Better control of the pollution generated
- Increase in product quality
- Sharing of knowledge and experience between departments
Let's find out how it works...
The 8 pillars of Total Productive Maintenance (TPM)
The Total Productive Maintenance concept was developed by Japan's Seiichi Nakajima. The results of his work on the subject led to the TPM process in the late 1960s and early 1970s. Denso, a Japanese company specializing in the manufacture of parts and systems for automobile manufacturers and a supplier to Toyota, was one of the first organizations to implement such a TPM program.
It is based on the so-called 5S system built from five Japanese words :
- Seiri to organize: to eliminate the superfluous present around the workspace
- Seiton to order: to perfectly position the remaining elements: "a place for everything and everything in its place"
- Seiso for cleaning: cleaning the workspace and keeping it clean
- Seiketsu to standardize: standardize work processes and make them consistent
- Shitsuke to formalize: constantly reinforcing the first four points
Based on these five postulates, the TPM is based on eight principles that must be implemented and respected: these are commonly referred to as the eight pillars of Total Productive Maintenance:
- Pillar 1: targeted improvement (kaizen)
- Pillar 2: Autonomous maintenance
- Pillar 3: Planned maintenance
- Pillar 4: Improving knowledge and know-how
- Pillar 5: Early equipment management
- Pillar 6: Quality maintenance
- Pillar 7: TPM in Administration
- Pillar 8: Safety, working conditions and the environment
Let's detail what each of these 8 principles covers and how CMMS will facilitate their implementation and acceptance within the company.
1 - targeted improvement
The targeted improvement is based on the Japanese term "kaizen". In manufacturing processes, kaizen requires continuous improvement of functions and processes. Targeted improvement examines the process as a whole and seeks ideas on how to improve it. It is essential for TPM to ensure that small teams work together proactively to implement regular, incremental improvements in processes related to equipment operation.
Diversification of team members is to be encouraged in this area. Indeed, it enables recurring problems to be identified through cross-functional brainstorming. It also makes it possible to combine the contributions of the whole company so that teams can see how the modification of a process can impact other departments.
Targeted improvement increases efficiency by reducing product defects and the number of processes, while increasing safety by analyzing the risks of each individual action. Finally, targeted improvement ensures that improvements are standardized, making them repeatable and sustainable.
The contribution of CMMS to targeted improvement
On this 2nd pillar, one of the greatest advantages of CMMS is its ability to capture repair history and record all equipment data. This functionality is invaluable. Not only is it easier for maintenance technicians to accurately and quickly diagnose a breakdown by referring to equipment history, but it would be very difficult, if not almost impossible, to accurately determine which technical assets have the most downtime without relying on the historical data held in the CMMS.
The use of a CMMS allows for better identification of problems and rapid deployment of new strategies to eliminate the occurrence of defects or incidents in the future.
2 - autonomous maintenance
Autonomous maintenance means that the machine operators are responsible for performing routine maintenance such as cleaning, lubrication, replacement of wearing parts and inspection, and that this is their sole responsibility. This allows operators to take better ownership of their equipment and increase their knowledge of its operation. It also ensures that the machines are always clean, lubricated and in perfect working order. Problems are also detected at an early stage before they develop into failures. Finally, maintenance personnel are freed up for higher-level tasks.
The operator must of course be trained to have the technical skills to perform a routine inspection based on the machine manual. Once trained, the operator establishes the inspection schedule with the maintenance manager. Standardization ensures that everyone follows standardized procedures and processes.
The contribution of CMMS to autonomous maintenance
The CMMS will provide considerable assistance in setting up autonomous maintenance, in particular for :
- Recording of activities performed: maintenance managers or supervisors are thus perfectly aware of the maintenance work performed and the time spent on maintenance tasks by machine operators. With CMMS, it becomes extremely easy to effectively control the process and see who did or did not do what
- The simplicity and speed of this recording, which is done with a minimum of training and without disrupting their normal workflow, operators have a better understanding of what is expected of them, are more motivated to set up the device, making the transition to TPM much easier
-
Work order management: Thanks to this CMMS function, operators can immediately issue work orders to report a breakdown or alert on the probability of its occurrence, when they feel they are not able to manage them by themselves.
3 - preventive maintenance
Planned maintenance involves studying parameters such as failure rates and historical downtime and then planning maintenance tasks based on these failure rates or planned or measured downtime. In other words, because there is a specific time to perform maintenance on the equipment, you can schedule maintenance around the time when the equipment is unused or produced at low capacity, rarely interrupting production.
In addition, planned maintenance makes it possible to anticipate and procure repairable spares that can be replaced at the time when the scheduled task takes place. Since you will know when each piece of equipment is scheduled for maintenance activities, this stock build-up helps to mitigate any drop in production due to maintenance.
This proactive approach significantly reduces unplanned downtime by allowing most maintenance operations to be scheduled at times when machine production is not scheduled. It also allows you to plan inventory more thoroughly by giving you the ability to better control parts that are subject to wear and tear and breakdowns. Other benefits include the gradual reduction of breakdowns resulting in uptime and reduced capital investment in equipment as it is used to its full potential.
The contribution of CMMS to planned maintenance
Proactive maintenance involves precise planning of recurring maintenance operations. CMMS, with its ability to organize and schedule each step of a preventive maintenance plan extremely easily, to manage an unlimited volume of information, and to replicate standard maintenance methods throughout the company's fleet, will prove to be an indispensable ally in this field.
📰 Read also: Find out more about Yuman CMMS
4 - improvement of knowledge and know-how
The lack of knowledge of the maintenance actors can hinder a TPM program. This pillar therefore focuses on training and education for machine operators, maintenance technicians and managers. Reinforcing knowledge through appropriate training programmes aims to ensure that everyone shares the same objective regarding the TPM process, that technicians are fully trained, autonomous, versatile and become experts in the equipment they maintain, and to increase the motivation and level of contribution of everyone.
Operators acquire the skills needed to proactively maintain equipment and identify emerging problems, the maintenance team learns to follow preventive and proactive maintenance programs, and managers strengthen their skills in TPM principles and employee coaching.
The contribution of CMMS to improving knowledge and know-how
In doing so, the company will benefit from the advantages of a service filled with experts capable of minimizing downtime, and CMMS will help achieve this goal in a number of ways:
- Firstly, by measuring the contribution of everyone involved, the tool will be able to indicate which employees should receive additional training
- Secondly, the CMMS will have a digitized knowledge base consisting of detailed maintenance instructions, manuals, plans, images, video and tutorials, which can be consulted by anyone at any time, either from a fixed station or on the move from a smartphone or tablet.
This shared knowledge base can both be automatically enriched or completed by the actors themselves from the information collected in front of the equipment.
5 - early management of equipment
The so-called "early" management of equipment consists of taking into account feedback from equipment maintenance in order to develop and improve the design of new equipment that will replace the production systems in place.
The design of equipment benefiting from feedback from its users and maintainers makes it possible to improve its maintainability and operation. It is therefore essential to anticipate ease of cleaning and lubrication, accessibility of parts, ergonomic placement of controls so that they are comfortable for the operator, as well as safety features.
This approach increases efficiency, as new equipment already meets the desired specifications and increases reliability and safety of use.
The contribution of CMMS to early equipment management
Here again, the CMMS's recording and centralization capabilities combined with its reporting capabilities will prove decisive. Through the succession of information gathering from the interventions carried out by technicians, it becomes easy to determine precisely where problems occur, when they occur, how often they occur and what are the main elements that cause them.
All that is needed is to make this information available in real time, following or during debriefing meetings, to the equipment designers so that it can be taken into account in the evolution of machine manufacturing.
6 - Qualitative maintenance
Optimal maintenance planning and strategy, which is essential in the implementation of a TPM, will not be of any use if the quality of the maintenance carried out is insufficient. Maintenance operators must therefore have the capacity to maintain the equipment in operational conditions.
Quality maintenance is implemented in two phases. The first phase aims to eliminate quality problems by analyzing defects in order to define new maintenance conditions that will eliminate their recurrence. Then the current condition is examined and improvements can be made again. In this way, the second phase ensures that quality is maintained by standardizing parameters and methods to achieve a zero-defect system.
The contribution of CMMS to quality maintenance
While planned maintenance is necessary to ensure that quality is maintained through routine manual inspections, it may not be sufficient because there is still room for human error. It must then be reinforced by a predictive maintenance strategy deployed within the CMMS: real-time monitoring sensors will detect potential problems and trigger the intervention of a technician in advance, before a defect or breakdown occurs.
Quality maintenance is implemented in two phases. The first phase aims to eliminate quality problems by analyzing defects in order to define the optimal conditions that will prevent the occurrence of defects. Then, the current condition is examined and improvements are implemented.
The second phase ensures that quality is maintained by standardizing parameters and methods to achieve a zero-defect system. Whatever method they choose to adopt, CMMS is essential to be able to correctly capture and analyze data, whether it comes from sensors or human intervention.
7 - TPM in administration
To be fully and successfully deployed across the enterprise, TPM must extend beyond the manufacturing chain by identifying and eliminating wasted time in administrative support functions, such as parts order processing, supply management, inventory and stock management.
It is essential that these back-office functions are streamlined and efficient. With more streamlined order processing procedures, spare parts arrive more quickly, and the necessary resources and materials are always available to maintenance teams, limiting potential downtime in the event of an incident.
The contribution of CMMS to TPM in administration
CMMS operates as a platform for exchanging information and sharing processes between maintenance actors on production lines and administrative staff. Through these mobility functions (mobile application) the technician receives and transmits information in real time without having to move in front of a computer to access a document, an instruction, or having to re-enter the data collected in front of the equipment.
CMMS also takes care of document management, spare parts catalog management, consumables management, inventory management: thus the CMMS inventory management module allows users to manage supplies and monitor replenishment levels, whether from the office or from the production line.
8 - Safety and working conditions
Maintaining a safe work environment means that employees can perform their duties in a place that is safe for their health.
While it is important to create an environment that makes production more efficient, it is a priority not to jeopardize the safety and health of employees. It is also notable that when employees come to work every day in a safe environment, their attitude is more relaxed and more conducive to social harmony.
Furthermore, companies that show complacency can be subject to heavy fines and severe penalties.
The contribution of CMMS to improving safety in the workplace
CMMS allows users to develop security plans for specific projects and tasks and to follow their instructions more easily. Safety information such as safety data sheets, standard operating procedures, mechanical and electrical safety checklists, etc. can be stored and retrieved at any time. As an example, an instruction to be followed can be displayed on the mobile phone and its correct consideration must be confirmed by the technician before he can start his maintenance task.
Proof of inspections: external control and audit offices may request safety inspection records at any time as part of their routine checks. The CMMS can instantly present the inspection records as proof of compliance.
By the way, our ambition is to offer an unparalleled user experience. Check it out right away: try CMMS for free. Within 2 minutes, the time it takes to create your account, you'll discover what's newest in this category of software.
You can also benefit from a demonstration led by one of our consultants: book a videoconference
Good discovery and see you soon!
📰 You will also be interested in reading :
- Managing your spare parts with CMMS
- IoT: the bright future of maintenance
- Cosmetics Industry and CMMS
- CMMS for the Food Industry
- CMMS to meet the challenges of the pharmaceutical industry
- CMMS in the medical sector
- Aeronautics industry and CMMS
- FMECA and CMMS: maintenance excellence
- Autonomous maintenance & CMMS
- Why is preventive maintenance a priority?
Back to the articles