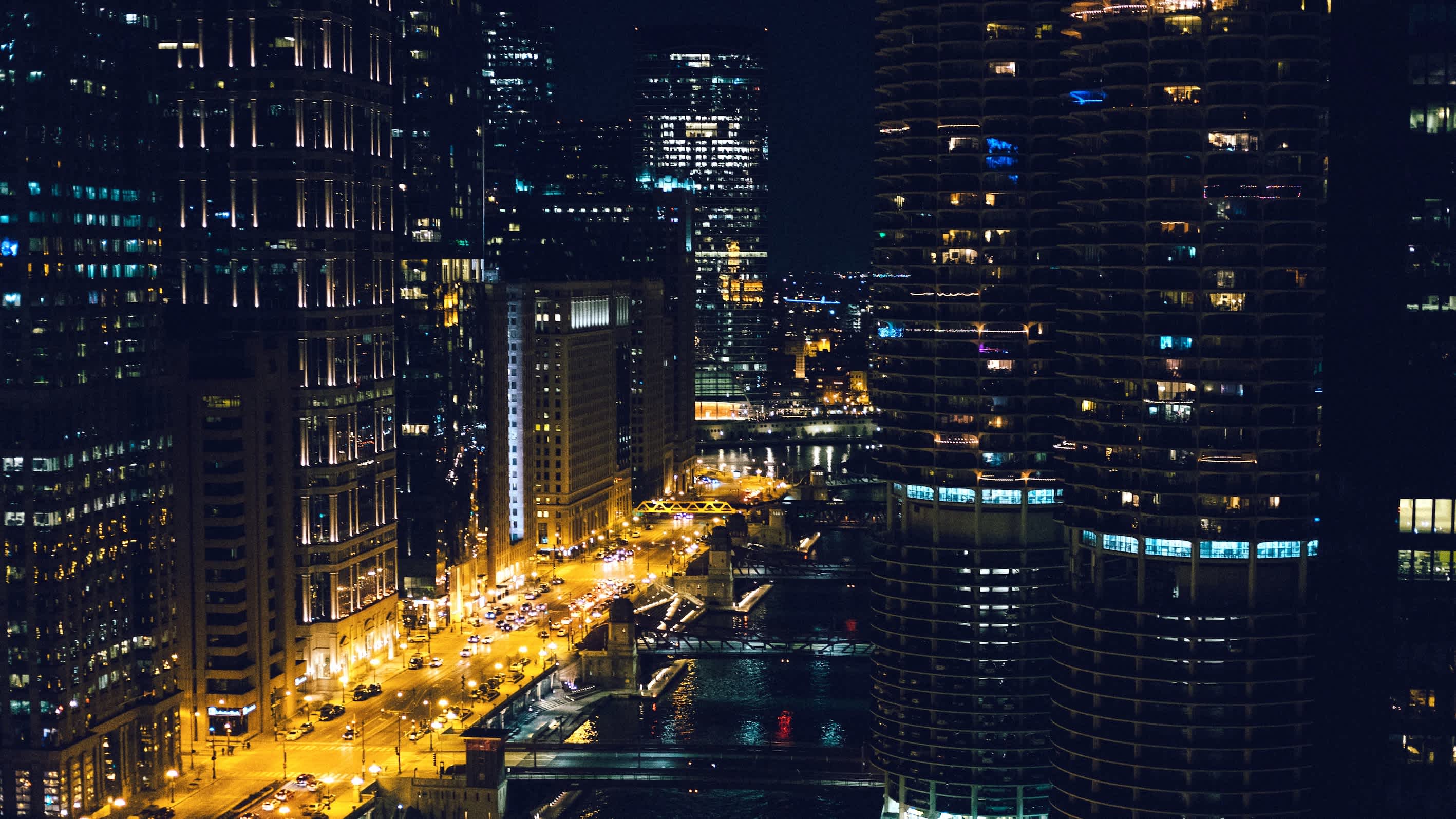
Today, I connect my CMMS to my BMS!
Saturday 12 december 2020
> Why a CMMS for property maintenance?
What is a BMS?
BMS, an acronym for Building Management System, is the set of hardware and software systems for collecting and processing data from a single site, in order to supervise all its assets and monitor energy consumption. To simplify we can say that BMS in the tertiary or collective residential sector treats the same elements as home automation for the private home and does this on a larger scale. The technical batches covered by the BMS are as follows:
- Equipment related to the comfort of the occupants: electric or gas heating, air conditioning, ventilation, lighting, blinds, shutters, etc.
- Intrusion detection systems, video surveillance, etc.
- Access control devices
- Elevators
If the FSS, for Fire Safety Systems, can be connected to the BMS via a gateway, the equipment contributing to the fire safety of the building must always be managed independently, in accordance with the standards and regulations in force in each country.
The BMS also integrates the management of consumption and the piloting of the energy performance of the building.
Thus, this solution works according to the implementations, either in read-only mode (data feedback such as alarm monitoring or visualization mimic diagrams), or in read/write mode, a mode in which it is possible to act remotely on the installation: opening or closing of a valve, switching on or off the lighting, etc.
THE DEFINITION OF CMMS
Well, let's keep it short, and I invite you to refer to the excellent article Understanding CMMS... 😉
In short, a Computerized Maintenance Management System (CMMS) is designed to manage the preventive and curative maintenance operations to be carried out on a building and on all the assets it contains and which contribute to its proper operation and to the safety and comfort of its users.
The main functionalities of a real estate CMMS are :
- Distribution of interventions in real time
- Shared calendar
- Cartography
- Photos and signatures
- Customizable work orders
- Multi-tech and multi-passage interventions
- Real-time notifications to technicians and managers
- Inventory of areas, premises, spaces on the site
- Inventory of installed equipment
- Monitoring of the life cycle of each installation
- Management of preventive maintenance plans
- Generation of preventive interventions
- Real-time monitoring of the smooth running of operations
- Construction of the digital maintenance logbook of the facilities
- Key Performance Indicators
INTERCONNECTION OF THE BMS TO THE CMMS
With the help of the BMS, technical managers of buildings can easily monitor how the main elements of their facilities are functioning on the basis of the data collected. The Building Management System enables them to remotely control and adjust all connected systems to optimize their performance, monitor the building's energy consumption and contribute to energy savings. In addition, the BMS makes it possible to easily generate reports, visualize data and create alerts to warn users when set thresholds for certain quantities are reached or when an asset fails. But in no way does a BMS repair or maintain components. Only technicians are able to perform these operations. And to organize their missions efficiently, they need a modern CMMS. That's good news. Isn't Yuman the future of CMMS?
To sum up, on the one hand we have software that records a lot of information, which is Technical Management, and on the other hand software that organizes interventions and facilitates the work of technicians. The evidence is there: technical data must be passed on to technicians and maintenance managers to increase their knowledge. And this must be done via CMMS.
Unfortunately, this is going to be painful. While the benefits of successful integration are obvious, we can only observe that very few organizations or maintenance departments have made any progress in these projects. Few companies have managed to establish a connection between the BMS and their CMMS, or even use alerts from sensor networks on a regular basis, to improve the maintenance, reliability, processing and energy performance of assets.
This raises several questions:
- Why is this data that appears on supervisory positions not transmitted to CMMS?
- Why when the field technician arrives in front of the equipment he has to maintain or troubleshoot, he does not have the technical data that would be valuable to him in order to perform his diagnosis or specifically undertake certain maintenance operations?
- Is there a real technological barrier that prevents the sharing of this information?
More and more buildings and assets are now equipped with sensors for electronic monitoring and control of operating status and performance. The data is there, available. However, the link between this equipment information and the operations of maintenance personnel, who could benefit greatly from it, is only very rarely realized.
Services usually provide short-term answers to these questions:
- Our BMS system is controlled by a separate team and it is very difficult to transmit the information to the maintenance team
- Getting the systems to talk requires a customized interface and our IT people are too busy or don't have the experience to create the gateway
- Our CMMS software is too complex, not very efficient and does not have a mobile application (if you're going to laugh, but most CMMSs are still not mobile) and therefore, anyway, technicians will not have the information on the field
- We are too busy with security on a daily basis to devote time to these projects
- The maintenance is entrusted to subcontractors to whom we do not wish to directly transmit the information we collect
Thus, in the best of cases, what we encounter is limited to the transmission of critical alerts sent by the BMS to the CMMS software, which will automatically trigger a request for intervention. This exchange is done either through an API (Application Program Interface) but most often through a message sent by e-mail or a message deposited in an FTP directory. Long live the good old days in short 😁
A CONCLUSION FULL OF PROMISE
Rest assured that at Yuman we have the skills, technologies and sense of customer satisfaction to ensure that users of our CMMS solution can benefit from this information sharing. The objective is to build together a maintenance platform based on counts, alerts/alarms and all valuable data collected by the BMS systems in place. And we won't give up, because we know from experience that this is indeed the essential condition to benefit from the return on investment of implementing technical management solutions. A successful combination of BMS and CMMS is the assurance of a maintenance and performance monitoring strategy based on the condition of the equipment. At the key: productivity gains, increased quality of service and cost reduction.
By the way, our ambition is to offer an unparalleled user experience. Check it out right away: try CMMS for free. Within 2 minutes, the time it takes to create your account, you'll discover what's newest in this category of software.
You can also benefit from a demonstration led by one of our consultants: book a videoconference
Good discovery and see you soon!
Back to the articles