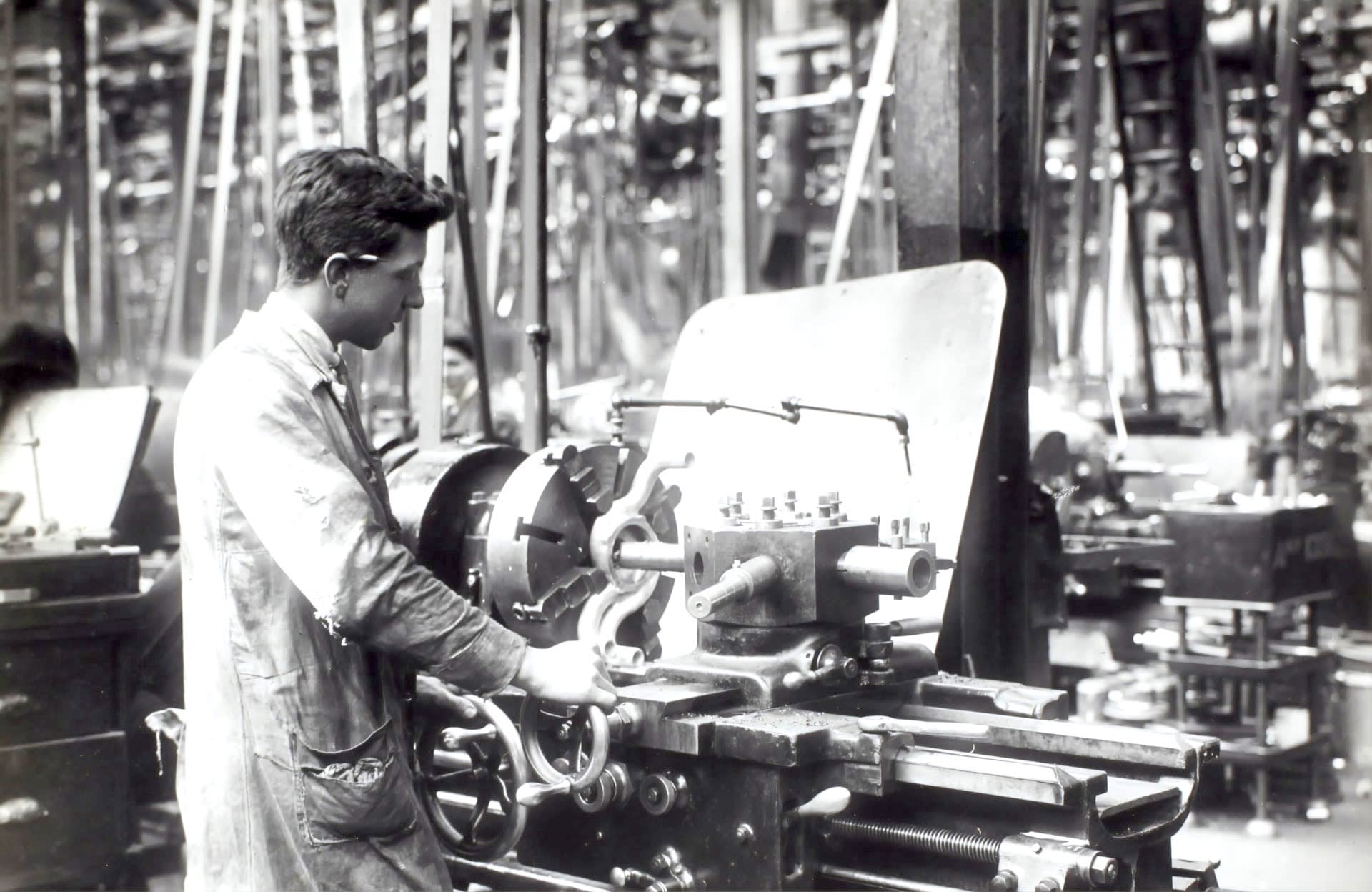
CMMS for industry offers solutions for managing work in companies
Wednesday 16 march 2022
Computer-aided maintenance management essential to business management
CMMS in the industry sector has become essential to industrial performance. It allows efficient management of a company's machines and equipment. The management of maintenance by a CMMS software allows the manager of a maintenance department to have the following functionalities.
- List of materials and equipment requiring maintenance
- Centralization of the documentation related to the equipment (technical information, purchasing data) and to the interventions (teams, quality controls)
- Provision of an up-to-date integrated maintenance log for each piece of equipment
- Planning of preventive or corrective maintenance interventions
- Management of the activity of the various internal or external maintenance services (suppliers)
A company manager can also use the software to perform the following operations
- Calculation, comparison and optimization of maintenance interventions: machine life, team involvement
- Decision support solution. The choice of suppliers can be made thanks to an approach based on the costs of maintenance-related purchases
- Comparison, analysis and processing of requests for interventions on production machines
- Spare parts inventory management
An example perfectly illustrates the benefits of the CMMS tool for the company. It is the cosmetics industry. On the border of chemistry and pharmacy, this industrial sector suffers no exception. It cannot have its production interrupted because of the failure of its production tool. The functionalities of the CMMS software guarantee better performance for the company. They improve production quality and secure preventive and corrective maintenance. They allow a better management of interventions and a "securing" of the quality of cosmetic products.
A CMMS tool for regulatory and safety compliance
There is a sector where CMMS in industry plays a crucial role. It is the food processing sector. Indeed, this sector of the industry transforms raw materials from agriculture, livestock or fishing into food products. As such, the food industry requires a CMMS that meets the standards, regulatory conditions and production constraints.
Ensure safe management of production equipment
Food production must strictly comply with numerous regulations. Any deviation from these rules can have an impact on the quality of the products and even the health of the customers. Beyond the impact on quality, it is also the company's brand that can be impacted and the responsibility of its manager. The equipment used to produce food must therefore be subject to increased surveillance. The CMMS is therefore essential for flawless management of the maintenance of production machines. The CMMS allows for the planning of cleaning, analysis and repair interventions on equipment.
Reassure customers about the quality of their products
The use of a CMMS software tool is also intended to provide consumers with peace of mind. Customers are reassured about the standards according to which their favorite products were manufactured.
Management of spare parts, stocks and consumables
Spare parts management in an industrial company's maintenance department is a time-consuming activity. However, it is essential to its performance. Managing spare parts with the CMMS allows the maintenance department to save precious time on a daily basis.
CMMS to keep parts inventories at the right level
When a company has insufficient stocks of spare parts, the availability of its assets decreases. Production may be lost or there may be significant delays in repairing the equipment concerned. On the other hand, too many spare parts in inventory result in high asset downtime costs.
The use of a CMMS software allows for a rigorous management of spare parts inventory. The following information is also provided to maintenance teams
- Live visualization of parts inventory, orders placed and possible supplier stock-outs
- Inventory management via mobile application, using QR codes or barcodes
- Issuance of alerts on low thresholds
- Analysis of the cost / lead time comparison between several suppliers
- Functionalities by equipment or by spare part: installation date, time to next replacement
CMMS to optimize supplier lead time planning
Anticipating the use of spare parts stocks is essential for maintenance teams. They must be able to manage variations in activity in real time. The CMMS software offers the following functionalities for each item
- Generate the automatic order of the part to the suppliers
- Be notified of the order follow-up
- Obtain, by scanning the article code, its position in the workshop or the warehouse
All these records are intended to improve the quality of production. An analysis of the software data will allow to list for example
- The parts of the equipment that break down the most often
- The suppliers who have a better quality rate of spare parts
- The suppliers with the best delivery times, etc.
CMMS maintenance software for industry
The role of CMMS software for industrial maintenance is largely described above. Its benefits for the management of a company are no longer to be demonstrated. The manager must be convinced of the necessity for him and his maintenance teams to have such a tool. From then on, it remains for him to choose the best CMMS software adapted to his activity.
Choice of CMMS maintenance software
The choice of the maintenance software must be made by the company manager according to the industrial activity. Different parameters are involved in the choice of your software. Yuman.io's offer is a modern, easy to use CMMS that allows you to track the equipment for which you are responsible. It allows you to manage your corrective and preventive maintenance through reports issued by on-site or mobile workers. It allows you to manage your stocks and obtain statistics on your interventions. Finally, it also offers financial modules for invoicing interventions, drawing up estimates and managing contracts. Our CMMS software is customizable. It allows you to define your account preferences and to keep only the information you need. It is also possible to add custom fields specific to your activity.
Calculation of the comparative cost of industrial maintenance
Some maintenance software automatically calculates the costs of preventive and corrective maintenance interventions. This is the case of the one proposed by Yuman.io. This calculation is made with the source data of the hourly cost of the speakers. The information of the duration of interventions must also be filled in to allow the calculation of cost.
Feel free to consult the other articles of the blog. You will find all the other areas of application of the CMMS at Yuman.io.
- Why a CMMS for property maintenance?
- CMMS software in the banking sector
- CMMS for the retail industry
- Internet 4.0: CMMS for security
- CMMS and sustainable development to protect the environment
- CMMS software for the building industry
- CMMS tools for transport
- CMMS applications in the health sector
Back to the articles