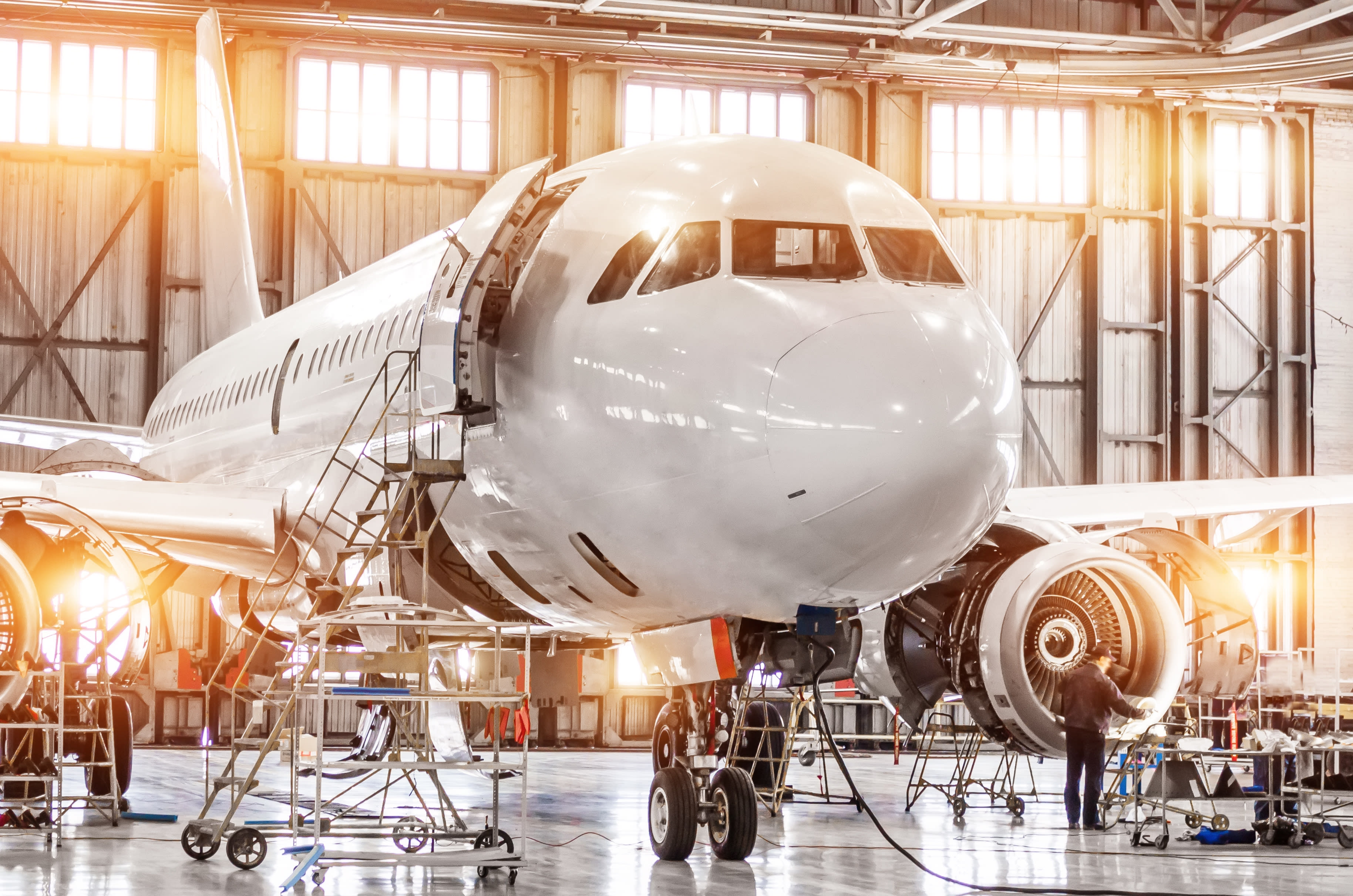
The Yuman maintenance glossary
Tuesday 07 may 2019
Meets another maintenance service provider...
What do they tell each other?
Maintenance stories...
Identify the different categories of maintenance
Maintenance is the set of actions performed during the life cycle of equipment in order to keep it in optimal working order. It is divided into 3 main categories: curative, preventive and predictive. The correct balance of these 3 approaches makes it possible to optimize the costs incurred in relation to the rate of proper operation.
Curative maintenance also called corrective maintenance or reactive maintenance. Comes after the detection of a problem generally observed by a user or site manager: a water leak, heating failure, elevator failure, blocked automatic gate, electrical issue, etc., the list of problems is endless. Curative maintenance consists of restoring the equipment to working order. The challenge is then to treat the emergency by assigning the repair to the technician closest to the place of intervention and most likely to respond. Yuman accelerates your curative maintenance interventions through planning, mapping, assets and mobility management for the technicians in the field.
Preventive maintenance: it is the periodic and anticipated control and maintenance of equipment (e. g. weekly, every 6 months, every year, every 300 hours of use) in order to reduce the probability of failure or breakdown. Avoid operating interruptions or malfunctions that may cause discomfort or even danger to residents and users. In this area, it is essential to respect the frequency of the planned visits. But the large volume of interventions to be carried out, the territory to be covered, the size of the teams can quickly become a real brain twister. Yuman will handle this complexity for you by managing the equipment list, maintenance ranges, maintenance plans, skills, teams, load/capacity. Generating, planning and allocating interventions will become a child's play. We will come back to the best practices of preventive maintenance in detail in a future article.
Predictive maintenance consists of the precise monitoring of equipment, via sensors and the transmission of technical data directly from the machine to the cloud, in order to anticipate failures as much as possible and mitigate technical problems before they occur. Machine monitoring makes it possible to adjust the timing of the intervention as closely as possible, in order to reduce costs as much as possible and to carry out "just in time" maintenance to avoid interruptions in operation while limiting travel. The ultimate in maintenance, so to speak. This is the domain of the IoT (Internet of Things). The alerts triggered go directly to Yuman and can either directly trigger the intervention of a technician or allow remote diagnosis and arbitration.
As you may have understood, Yuman can be used as a simple intervention management software, but also perfectly covers the more complex maintenance processes. Our application perfectly combines the simplicity of intervention management with all the richness of a real computer-aided maintenance management system (CMMS).
Find your bearings amongst the diverse and varied software programs: MWM, CMMS, EAM...
Property maintenance companies that install, maintain and repair equipment, have the specificity of having their staff work at sites far from each other and must cover a territory on the scale of an agglomeration, a region, a country, etc. As a result, they have their own problems of organization and remote management of people. 3 categories of software try to meet these needs.
First of all, intervention management software (FSM Software for Field Service Management Software or MWM for Mobile Workforce Management). These are software dedicated to the management of employees who work in mobility. They are in charge of planning and monitoring the teams in the field.
Next, come Enterprise Asset Management software (EAM). These software programs are dedicated to the life cycle of the company's assets, whether they are buildings, technical installations or industrial machines. Used alone, they will only provide a partial answer to the challenges of property maintenance.
The real answer is in CMMS (Computerized Maintenance Management System). CMMS performs a dual function: on the one hand, they support the operations of technical teams and, on the other hand, the life cycle of the equipment. Yuman is a complete, natively mobile, latest-generation CMMS that covers all the functionalities expected by a maintenance service provider.
Understand the main performance indicators
Whether in industrial maintenance or property maintenance, equipment and infrastructure failures can have costly consequences for the company concerned, impact the comfort or safety of residents or users and lead to a decrease in service quality and customer satisfaction. This is why it is essential to have precise indicators that will help to maximize the rate of proper operation of equipment.
MTTR for Mean Time To Recovery is the time that elapses from the time the failure is triggered until the equipment returns to a normal operating state. It includes fault recognition, technician travel, diagnosis, repair itself and return to service. Facilitated collaboration between the planner, the manager and the technician(s) involved is essential to improve this global indicator.
Be careful not to confuse it with Mean Time To Repair (MTTR too, no luck!) or Average Repair Time which is limited to the repair time. The improvement of this indicator will be made possible by training actions for personnel, but also by making available on site all the information necessary for the successful completion of the intervention, such as equipment history, operating instructions, etc.
MTBF for Mean Time Between Failures: it is the average time that elapses between two failures of the same equipment. It is calculated by dividing the operational operating time by the number of failures. This makes it possible to analyze the level of reliability of the asset and possibly highlight a larger problem if the same failure occurs successively.
MTTF for Mean Time To Failure: mainly used for non-repairable equipment, which requires straightforward replacement, this indicator determines the expected service life until the failure occurs. Analyzing this measure facilitates the anticipation of orders and replacements of the asset concerned, thus avoiding prolonged downtime.
OEE stands for Overall Equipment Effectiveness: it is an indicator mainly used in industrial maintenance to analyze the availability, performance, and quality of equipment production. It makes it possible to evaluate the productivity of a machine and determine what could be improved, for example, the use of preventive maintenance or the replacement of spare parts.
At Yuman, we are perfectly familiar with the technical issues and terms of the maintenance sector. Thanks to this experience and our proximity to our customers, we have developed a complete software package that covers all maintenance categories, records and capitalizes on the knowledge of the technical equipment to be maintained and manages the performance indicators.
By the way, our ambition is to offer an unparalleled user experience. Check it out right away: try CMMS for free. Within 2 minutes, the time it takes to create your account, you'll discover what's newest in this category of software.
You can also benefit from a demonstration led by one of our consultants: book a videoconference
Good discovery and see you soon.
📰 You will also be interested in reading :
- 8 actions for the successful implementation of CMMS
- Why it is so important to outsource your CMMS?
- CMMS specifications
- Keynote Yuman CMMS
- The 10 key points of CMMS
- When a Field Service Management Software becomes essential
- A mobile CMMS, or nothing!
- The digitalization of maintenance interventions
- Why should you buy your CMMS online?