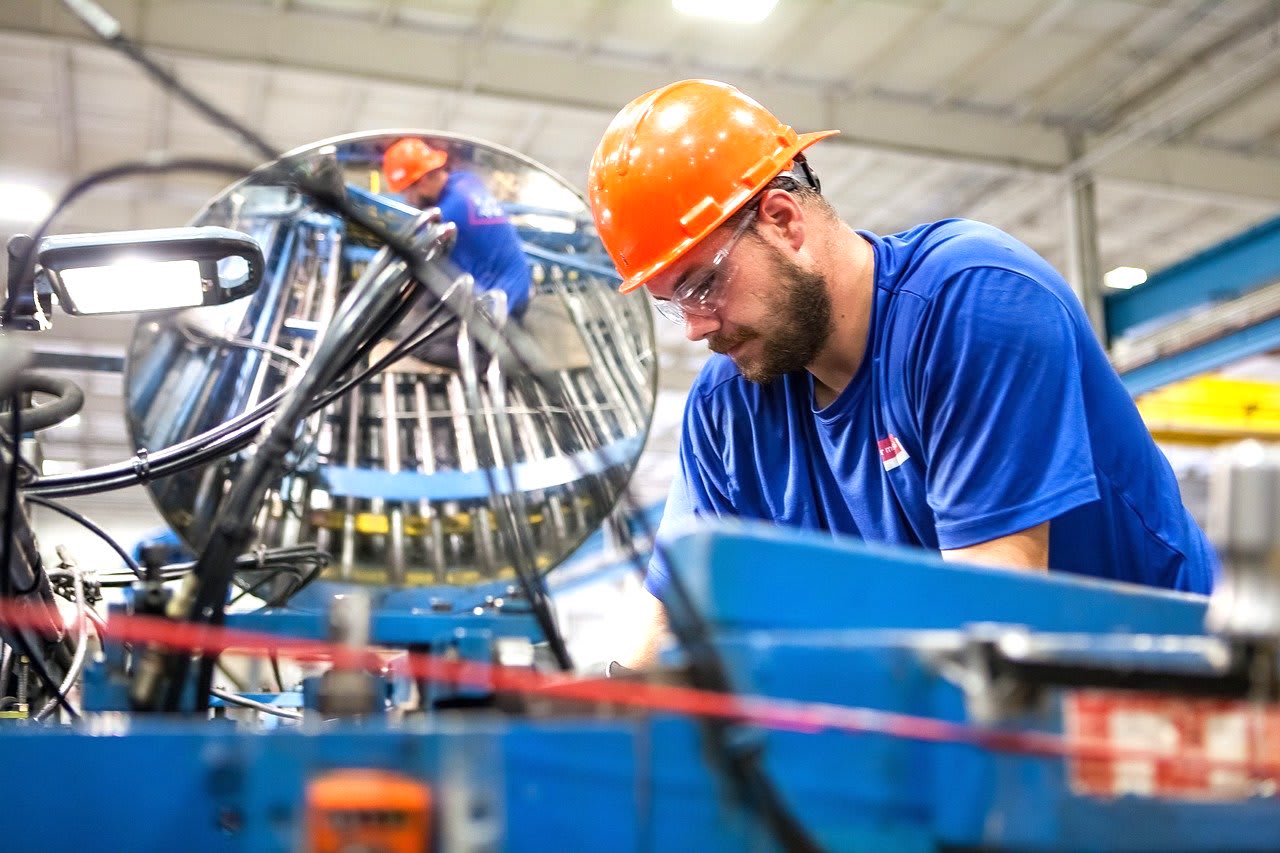
Industrial maintenance cost calculation: how to proceed?
Thursday 17 march 2022
So, when you invest in industrial maintenance software, make sure it has a powerful module that allows you to easily determine these KPIs.
What is a cost indicator in industrial maintenance?
When you invest in an industrial CMMS, think upstream about the indicators you want to monitor. There are many different types of indicators. They all measure the contribution of maintenance to the performance of your tools.
CMMS, a tool for managing industrial performance
To effectively manage your intervention teams, subcontractors, parts purchases, machine fleet monitoring, etc., there is nothing better than an ad hoc software. The CMMS gathers all the data to ensure that the production tools are in good working order. It contributes to the management of each piece of equipment and the monitoring of its operation. It provides a wealth of historical information. Let's mention the costs and repair times and the mechanical performance of the machines. Let's not forget the duration of breakdowns or the losses caused by stoppages.
What is the purpose of industrial maintenance cost indicators?
CMMS software is set up to provide key maintenance indicators. This is the case for each piece of equipment, each machine and even each component. These ratios or costs are compared with standards. Their evolution over time is also important. Thanks to the dashboards offered by CMMS tools, you have access in real time to synthetic or detailed information.
You can measure the contribution of maintenance to the performance policy of activities. These KPIs meet the needs of the company's operational staff and management.
Calculating the cost of industrial maintenance: indicator categories
You can classify the indicators into two categories. Some allow you to measure the impact of maintenance on production costs. Others are used to calculate the pure cost of industrial maintenance.
Key performance indicators
Among these KPIs that measure performance, we find indicators based on equipment in terms of :
- availability and unavailability
- efficiency
- mean time between failures
- efficiency (the SRR or synthetic efficiency rate)
- reliability with the calculation of the MTBF (mean time between failures)
- efficiency of maintenance teams
- etc.
Financial cost indicators for maintenance
Other KPIs aim at calculating the cost of industrial maintenance from a financial point of view as well as its comparison with the budget. The following indicators can be identified:
- labor costs for preventive and corrective maintenance
- energy consumption (electricity, gas, water), fluids and spare parts
- expenses related to maintenance subcontracting
- rental costs for replacement equipment
- etc.
Calculating the cost of industrial maintenance: fundamental management indicators
Let's now analyze some key indicators used to measure the performance of a site from a maintenance perspective. With CMMS software, you can easily configure the calculation of industrial maintenance costs and KPIs. You have a restitution in the form of a dashboard.
Cost of industrial maintenance and reliability: the MTBF
The MTBF is a very useful ratio to measure the reliability of an industrial equipment, as well as the failure rate. This indicator corresponds to the average of the uptime. In English, it is called mean time between failures. It calculates the time between two failures. Here is how to establish the ratio:
- in the numerator: total time elapsed between each stop and each restart
- in the denominator: number of failures
For example, on a 10-hour production day, if the downtime is two hours and there are 4 breakdowns, the MTBF is : (10-2)/4 = 2 hours.
Maintenance cost in industry and repair rate: the MTTR
With this MTRR (main time to repair) ratio, your CMMS software calculates the average repair time of an equipment. The objective is to measure if the interventions are efficient or not. It also allows you to know if your installations are easy to maintain.
The calculation of the MTTR corresponds to the total repair times divided by the number of interventions. It is interesting to monitor its evolution over time in order to take corrective measures. Multiple parameters then enter into the analysis. For example, skills, access to the machine or the availability of spare parts.
Calculation of the synthetic efficiency of the machines on a production site (TRS)
If there is one indicator that is essential for the production management of an industrial site, it is the OEE. It is the synthetic efficiency rate. It measures the rate of use of the machines in a factory. It influences the productivity of the manufacturing agents. In theory, this indicator is monitored by CMMS tools and combines
- the performance rate (net operating time divided by gross operating time)
- the operating rate (gross operating time divided by the theoretical time announced by the manufacturers)
- the quality rate (division of the optimal production time by the net operating time)
The OEE is then calculated as follows: performance rate X operating rate X quality rate. In practice, the OEE is often simpler. You divide the actual production by the theoretical maximum production. Let's take an example. The standard output of a production line is defined as 100 parts per hour. In reality, it is 90. In this case the OEE is 90/100 = 90%.
Tracking industrial maintenance costs: examples with the application of Yuman.io
With our CMMS tools dedicated to industry, the maintenance manager and company management have accurate financial tracking. Whether it is a detail by equipment or a summary report type dashboard, they have access to the total expenses either :
- the cost of technicians' interventions
- the cost of service provider interventions per installation
- the cost of consumables and spare parts assigned to each industrial equipment
Yuman.io, specialist in CMMS for industry, offers the following articles to complete your reflection:
Back to the articles